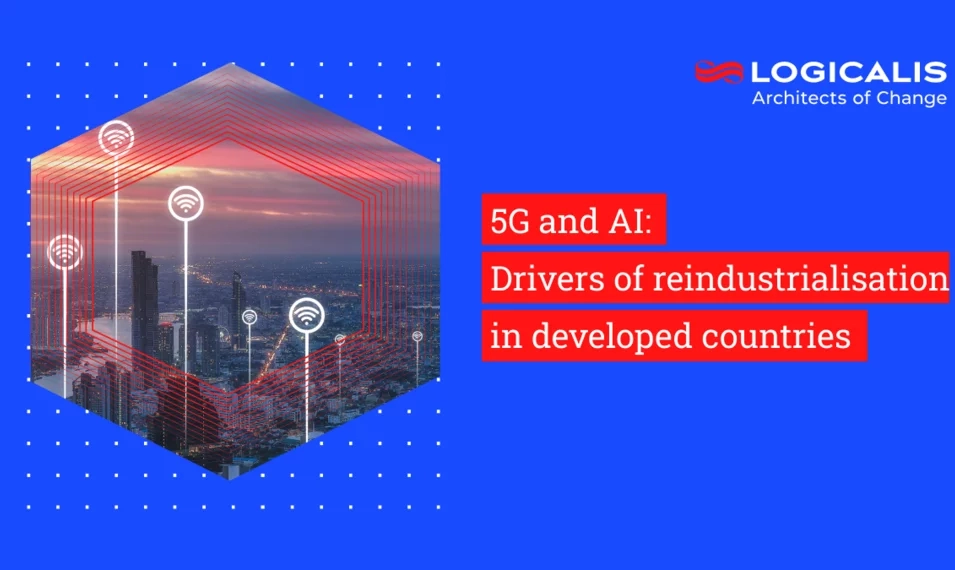
Global, Oct 16, 2023
Article by Rodrigo Parreira, CEO LATAM, Logicalis
View original article on Digitizeme
It's not futurism. Emerging technologies, such as 5G, IoT and Artificial Intelligence (AI), have the potential to promote profound transformations in the way global industry is organised. Integrated with robotics, these innovations enable a potential drastic reduction in the volume of labour involved in manufacturing in general and can drive a strong reindustrialisation movement in developed countries, impacting the entire organisation of global production chains and also the global geopolitical dynamics itself.
This change means the potential reversal of a phenomenon that began in the 90s. With labour costs reduced in certain regions, such as Asia, we have seen an intense movement of migration of manufacturing production, which changed the global economic organisation and promoted a a hitherto unlikely reality: the industry's separation from major consumer hubs, namely the United States and Europe.
Over the decades, China and other Asian countries have gained more and more space on this industrialisation map. Furthermore, supported by diversified manufacturing and with the ability to operate at very low costs, the Chinese took a step forward and large marketplaces with global operating capacity emerged, thus also shaking the foundations of international retail.
Now, technology can change this scenario by making the industry less dependent on labour and allowing manufacturing plants to return closer to large consumer centres. The advancement of 5G has everything to do with this transformation.
5th generation mobile networks provide very high data transmission speeds and very low latency (response time). This translates into faster communication between machines, which begin to work more autonomously and collaboratively. Artificial Intelligence, in turn, is capable of automating repetitive tasks, increasing their accuracy, anticipating possible failures and reducing them. Robots, already present in the industry, gain agility and, by integrating with these platforms, become capable of “making decisions”, becoming much more efficient and expanding the range of tasks they can perform.
Geoeconomic impacts
A major hub of factory production, Asia is not standing still and has already accelerated its pace in the technological race, investing heavily in robotics and research, and development to ensure its competitiveness in the new scenario that is emerging. Data from the International Robotics Federation illustrate this effort and show, for example, that South Korea has the highest density of robots in the world, with 1,000 pieces of equipment for every 10,000 employees, leading the list of countries with the most automation in manufacturing. The number is almost double that of second place, Singapore, which has 670 robots per 10,000 employees. Among the highlights are Japan, Germany and China. The latter made a big leap, moving from 20th to 5th position between 2018 and 2021.
In this scenario of redesigning global logic based on industrialisation, where is Latin America? How will she position herself? Would the region, which has been experiencing a process of deindustrialisation for some time, be left with basic industry? Will we play the role of producer of commodities, perpetuating the challenges of maintaining a positive trade balance? There are plenty of questions, but no answers. And Latin American governments still seem to be trapped in debates that refer to the industry of the past and not the industry of the future, in which the ability to innovate will be a decisive factor in success. In this context in which technology promotes profound changes, a major challenge is the qualification of the workforce that will carry out this change. In this new scenario, if on the one hand there will be a potentially reduced demand for workers for the factory floor, on the other we will have to rely on specialised professionals to operate these innovations and monitor their evolution.
The Future of Jobs report, published in May by the World Economic Forum, also highlights the increasing urgency for the reskilling revolution, with companies reporting that skills gaps and the inability to attract talent are key barriers to transformation . Six in ten workers are expected to need training before 2027. At the same time, the study estimates that, on average, 44% of an individual worker's skills will need to be updated.
Transforming this scenario requires coordinated action from governments, companies and workers. The discussion must involve everyone's participation in the search for models that, far from perpetuating traditional social and economic inequalities, can be aimed at sustainability and a fairer income distribution. On the right path, technology is capable of taking the entire society to a new level of efficiency and prosperity.
Related Insights
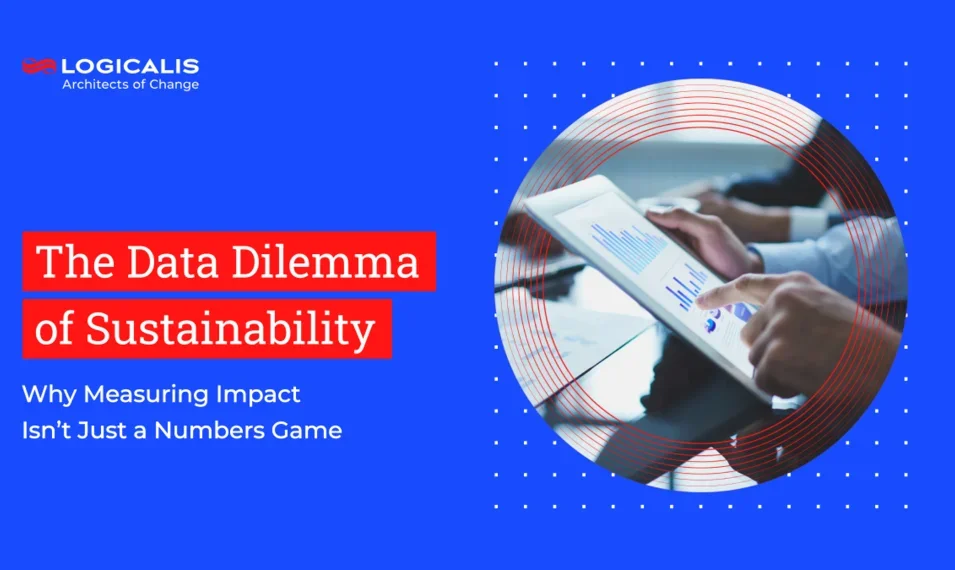
Global , Jul 29, 2025
The Data Dilemma of Sustainability: Why Measuring Impact Isn’t Just a Numbers Game
Explore how Logicalis tackles sustainability data challenges using IBM Envizi, blending ESG metrics with qualitative insights for meaningful impact.
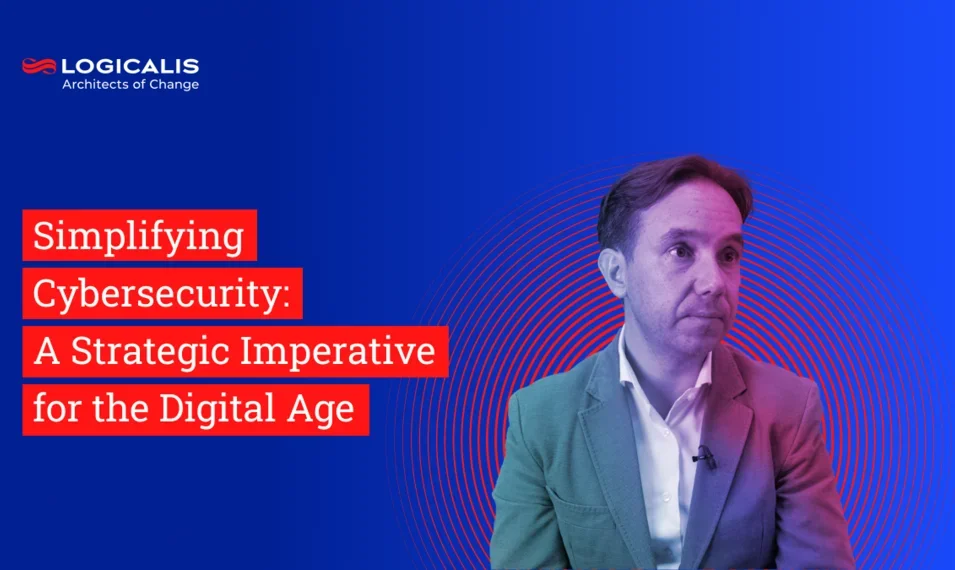
Global , Jul 22, 2025
In the news, Blog
Simplifying Cybersecurity: A Strategic Imperative for the Digital Age
As cyber threats grow, organisations add more tools—yet this complexity itself has become a major security risk. Artur Martins, CISO Logicalis, highlights how CIOs can develop simpler, modern security strategies
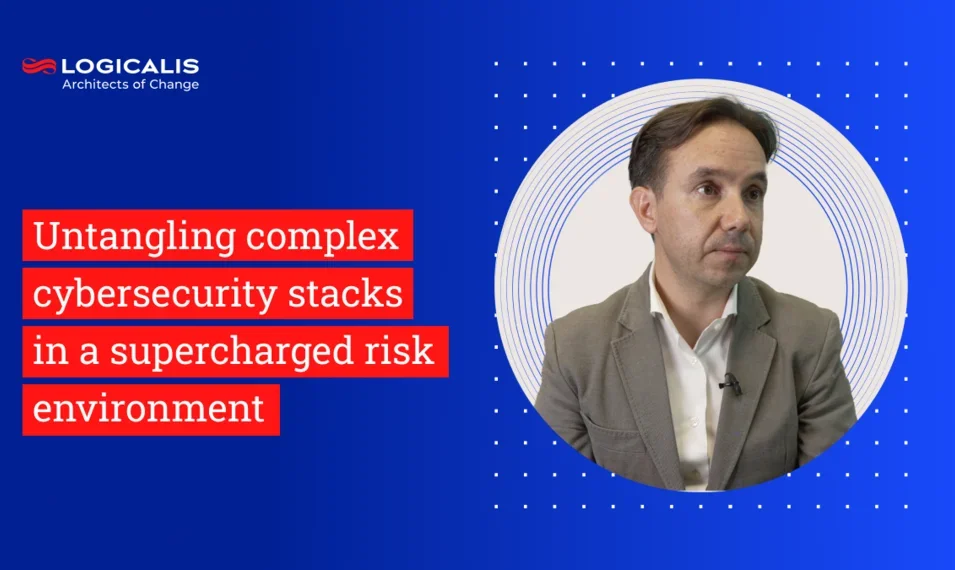
Global , Jul 22, 2025
In the news, Blog
Untangling complex cybersecurity stacks in a supercharged risk environment
Artur Martins, Logicalis CISO discusses the growing complexity of cybersecurity stacks in the face of escalating cyber threats.
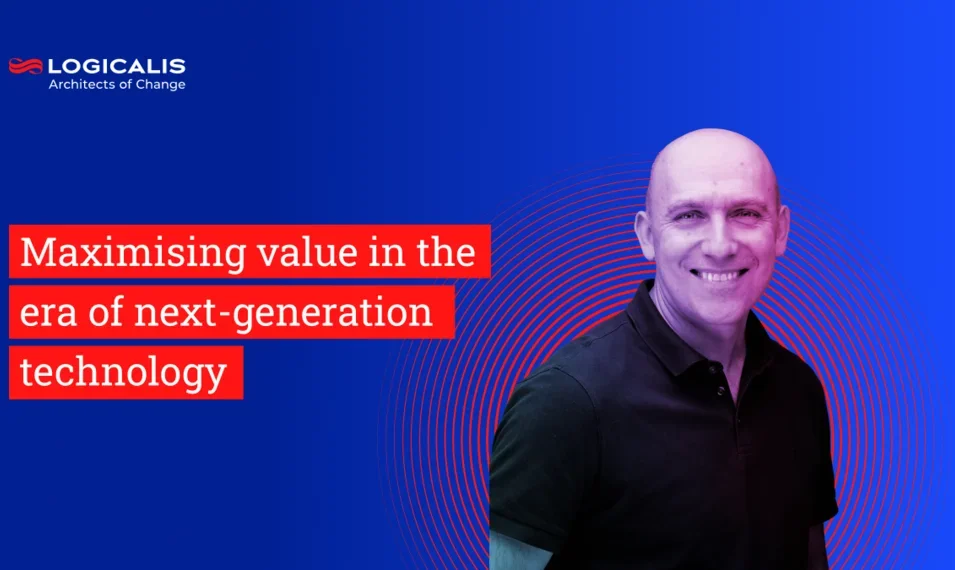
Global , Jul 22, 2025
In the news, Blog
The Engine for Business Growth: Embracing Innovation and Technology
Logicalis CEO, Bob Bailkoski unpacks the key insights from this year’s CIO Report, offering actionable strategies for success.
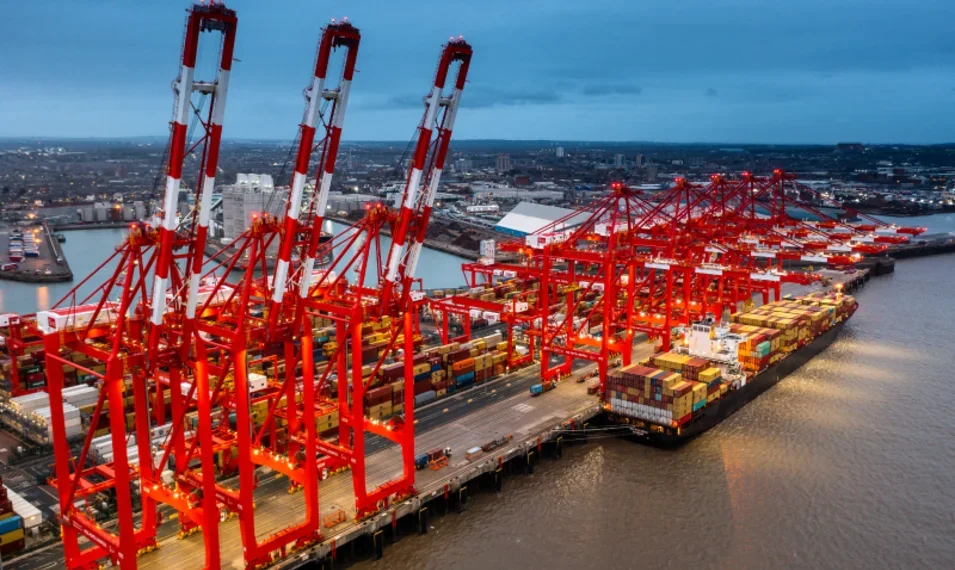
Global , Jul 9, 2025
Revolutionising port operations: How Private 5G is powering automation at Peel Ports
Peel Ports is leading the way in port automation with a cutting-edge private 5G network at the Port of Liverpool. Discover how this ON-SIDE initiative is reshaping the future of logistics and infrastructure.
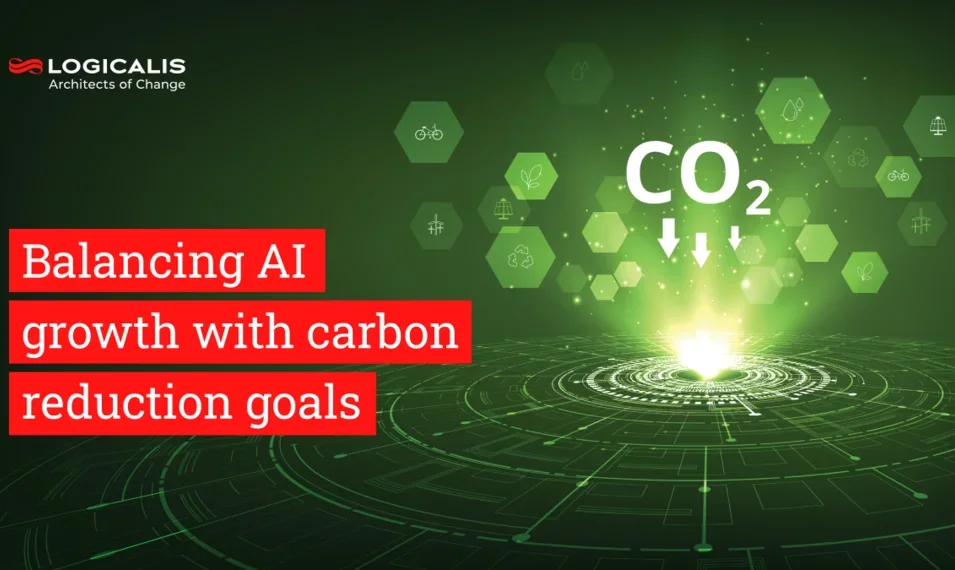
Global , Jul 7, 2025
Balancing AI growth with carbon reduction goals
Artificial intelligence has moved from the fringes of operational considerations to the forefront of operations. As organisations race to implement AI innovations, we all face a critical question, how do we reconcile the energy-intensive nature of AI with existing sustainability commitments?
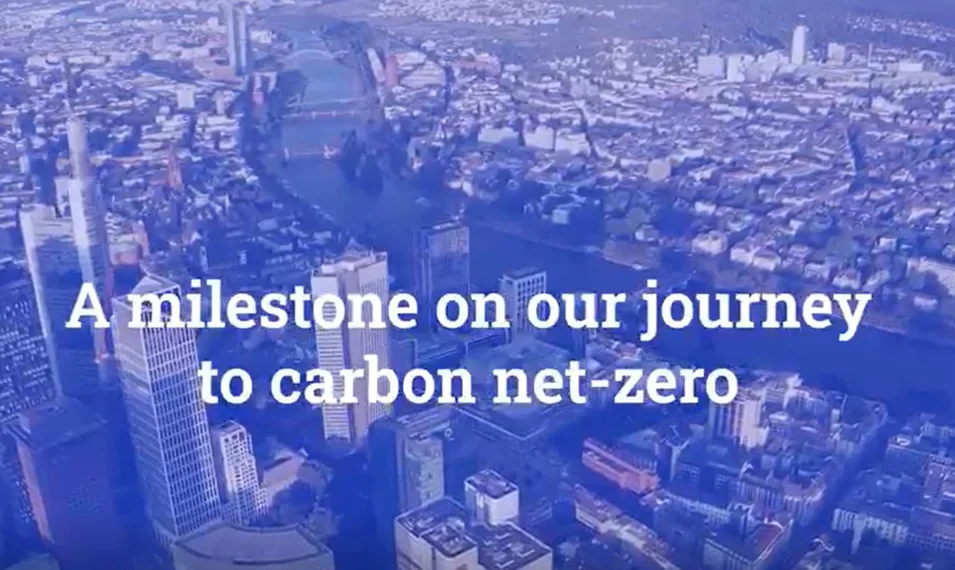
Global , Jun 25, 2025
Blog, Videos
Logicalis reaches carbon neutrality: Scope 1 & 2 emissions milestone achieved
Watch as Bob Bailkoski discusses how Logicalis has achieved carbon neutrality for its Scope One and Scope Two emissions, reaching its 2025 target.
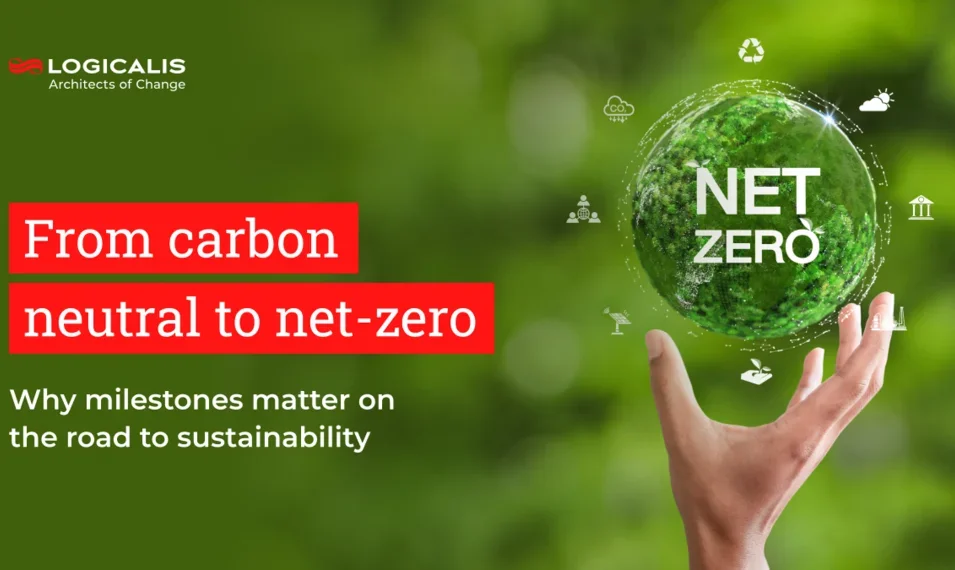
Global , Jun 19, 2025
From carbon neutral to net-zero: Why milestones matter on the road to sustainability
At Logicalis sustainability isn’t a secondary activity. It’s embedded in our DNA. As we mark our achievement of carbon neutrality for Scope 1 and 2 emissions, it’s a moment to reflect on not only how far we’ve come, but also on the road ahead.
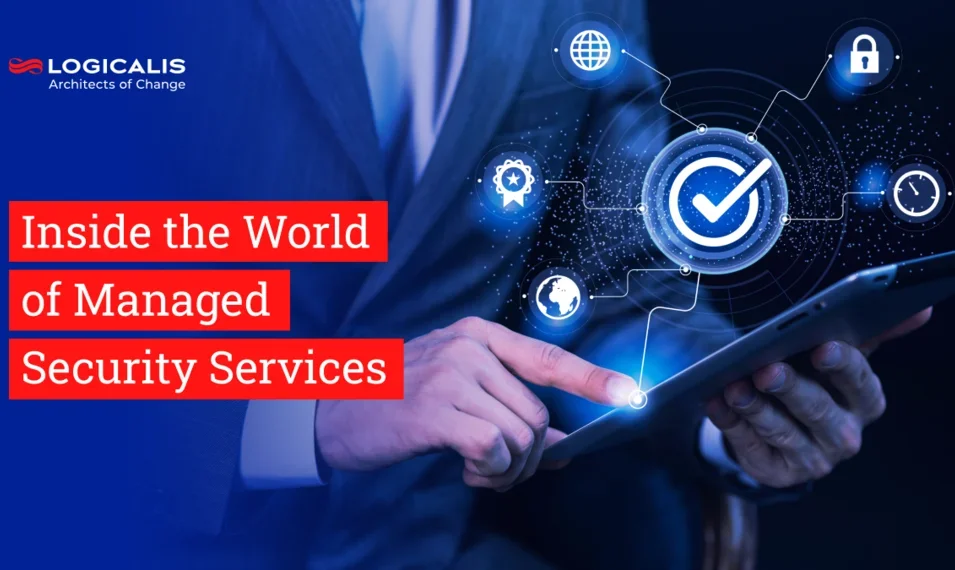
Global , Jun 12, 2025
Inside the World of Managed Security Services: An Interview with James Hampson
To uncover the inner workings of cybersecurity and the services offered by Logicalis, we spoke with James Hampson, Managed Security Services Director. His insights into the Security Operations Center (SOC) reveal the complexities, challenges, and triumphs of safeguarding customer environments.
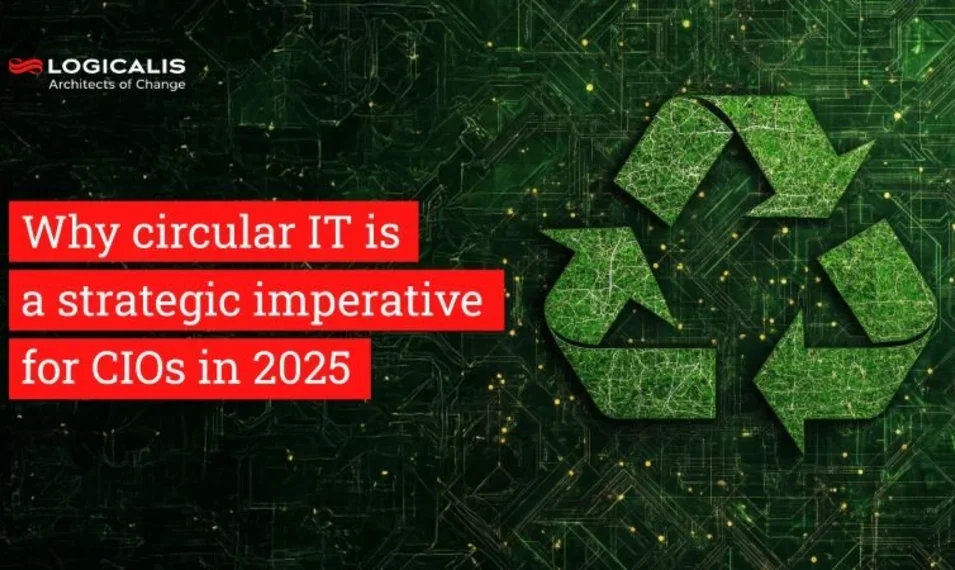
Global , May 29, 2025
Why circular IT is a strategic imperative for CIOs in 2025
The convergence of sustainability and profitability is reshaping how CIOs approach technology strategy. Circular IT is no longer just a green initiative – it’s a strategic imperative. By extending the lifecycle of IT assets, reducing e-waste, and leveraging vendor takeback programs, CIOs can transform their departments into sustainability powerhouses while unlocking new economic value.
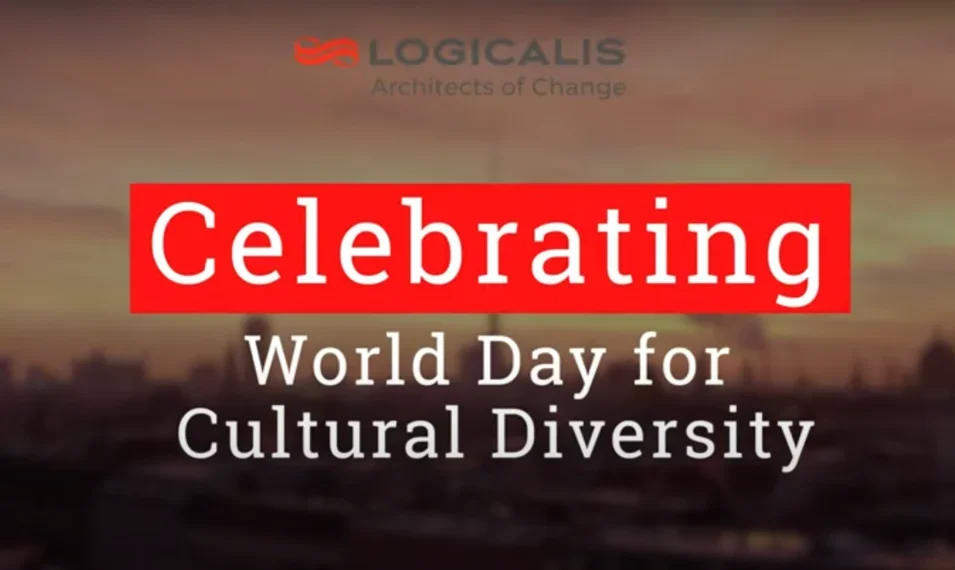
Global , May 27, 2025
Blog, Videos
Logicalis celebrates World Cultural Diversity Day
In celebration of World Cultural Diversity Day, we’re honouring the unique stories and perspectives that strengthen our team. When diverse voices unite, creativity thrives and innovation follows. Watch now ...
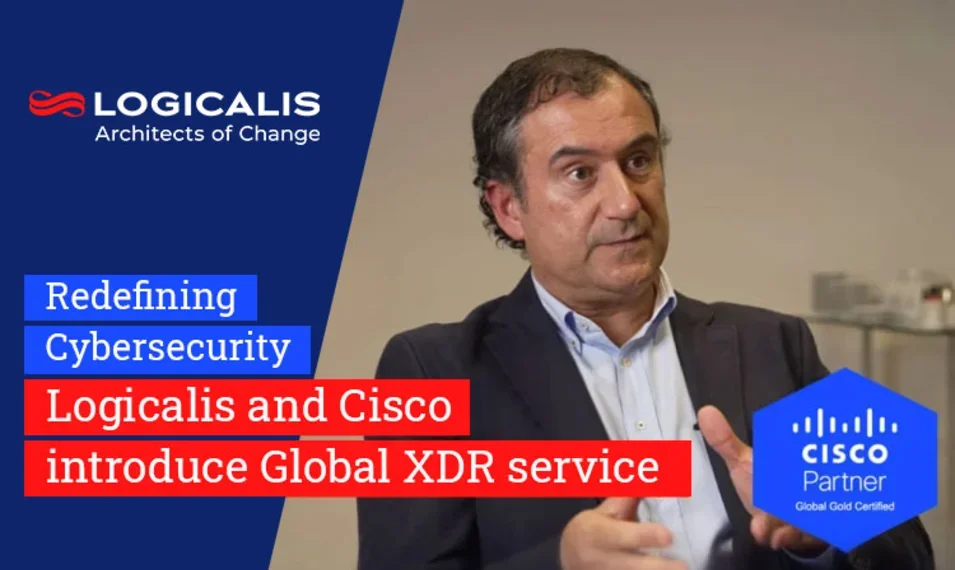
Global , May 27, 2025
Logicalis becomes the first global Cisco partner to launch XDR as a Service
Read this great article by Pedro Morgado as he discusses how the strategic partnership with Cisco helps Logicalis strengthen its cybersecurity leadership with the global launch of Cisco XDR.
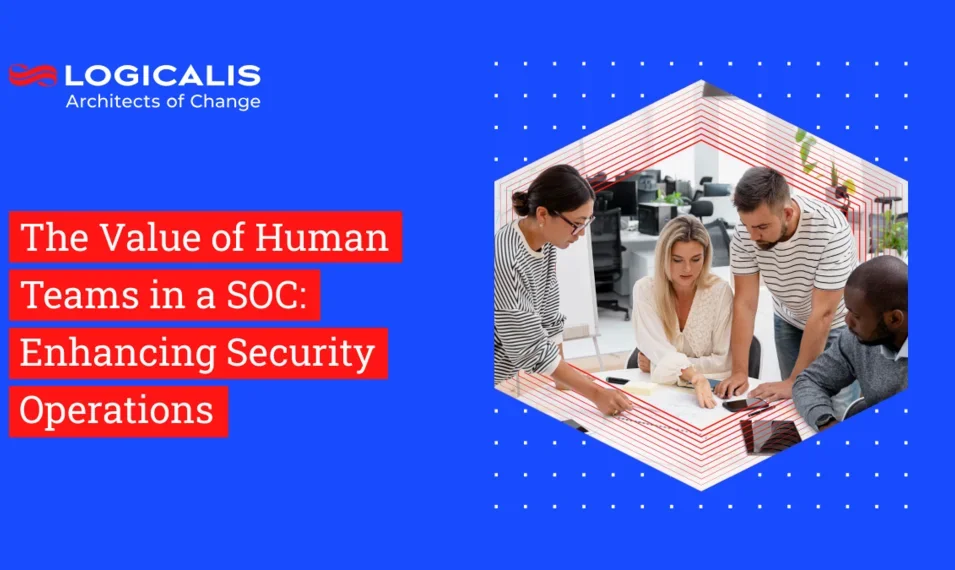
Global , May 27, 2025
The Value of Human Teams in a SOC: Enhancing Security Operations
Why technology alone isn't enough to safeguard your organisation - the importance of the human element in a security operations centre (SOC) and why it can't be underestimated. Article by Artur Martins, CSIO Logicalis Portugal.
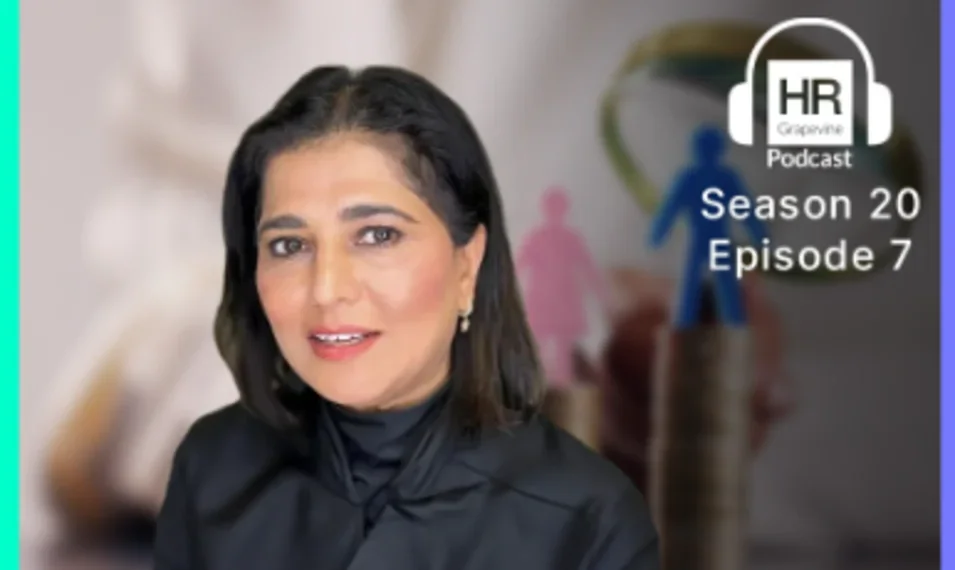
Global , May 20, 2025
Tackling the tech gender gap
The gender gap in tech remains a persistent issue and without action, disparities in representation and pay will continue. Dina Knight joins HR Grapevine's podcast to discuss how Logicalis is committed to change—challenging bias and building an inclusive, empowering environment for women in tech.

Global , May 16, 2025
How Managed XDR provides CIOs with confidence in their Cybersecurity coverage
Roger Loh, Head of Global Solutions, Logicalis, explores how Managed Extended Detection and Response (MXDR) equips CIOs with the visibility, control, and expert support needed to strengthen cybersecurity posture and reduce risk across the enterprise.
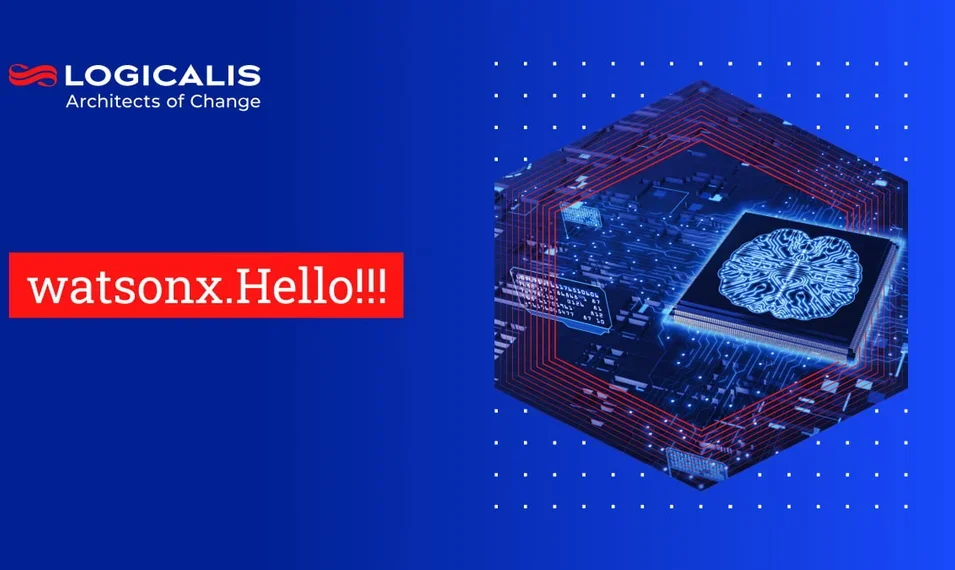
Global , May 13, 2025
AI that works for you in the age of watsonx
IBM’s watsonx platform helps organisations strike the right balance between building custom solutions and adopting ready-made AI to drive real value. Scott Hodges explores the platform’s capabilities and uncovers how it can accelerate innovation across your business.
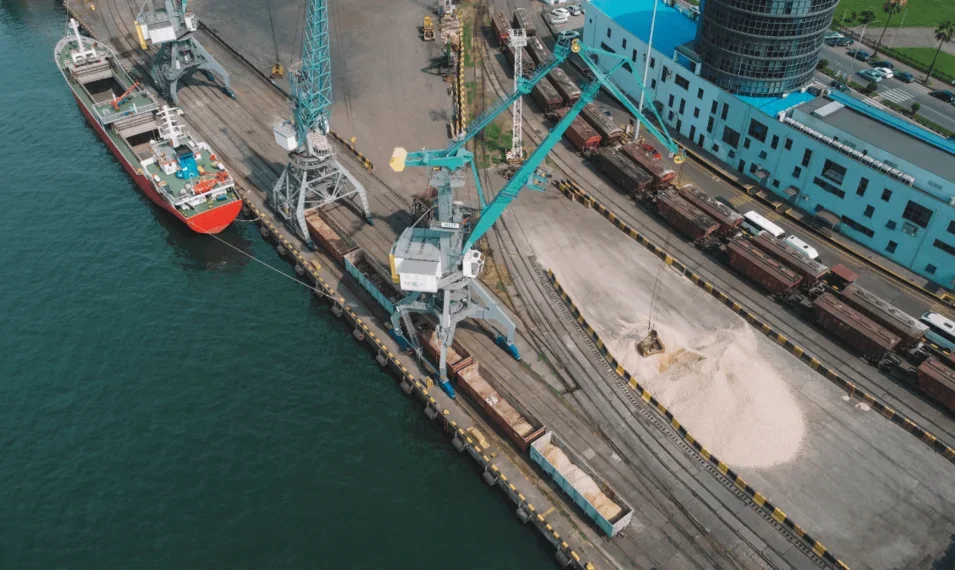
Global , May 13, 2025
From Smart Factories to Smart Ports: The Rise of Private 5G
Private 5G is redefining enterprise connectivity. While initial costs may be higher than Wi-Fi, the long-term gains in automation, efficiency, and ROI make it a smart investment for future-ready businesses.
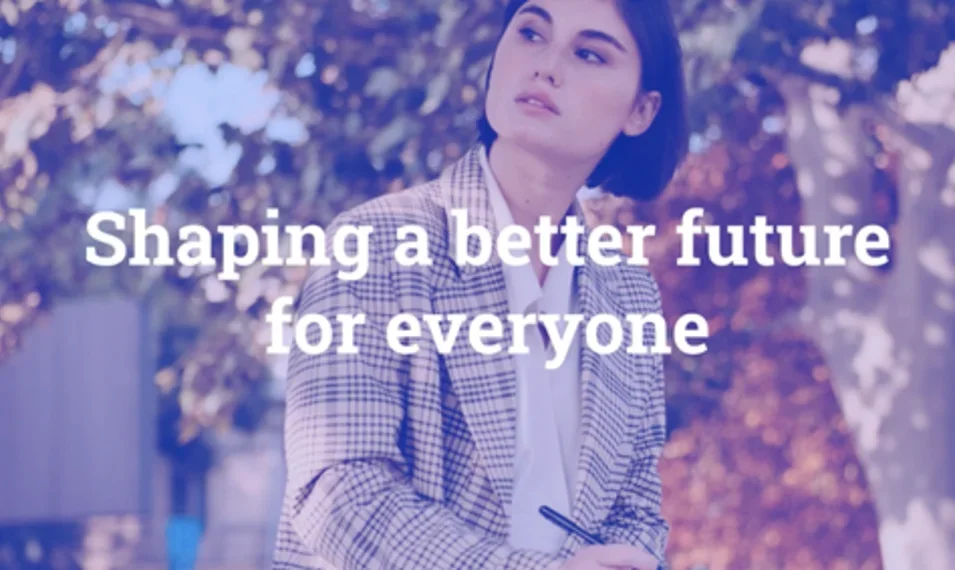
Global , Apr 29, 2025
Blog, Videos
Shaping the future women in tech
Logicalis' VP of Global Alliances, Anita Swann, shares her perspectives on the future of tech and the importance of encouraging more people to enter the industry.
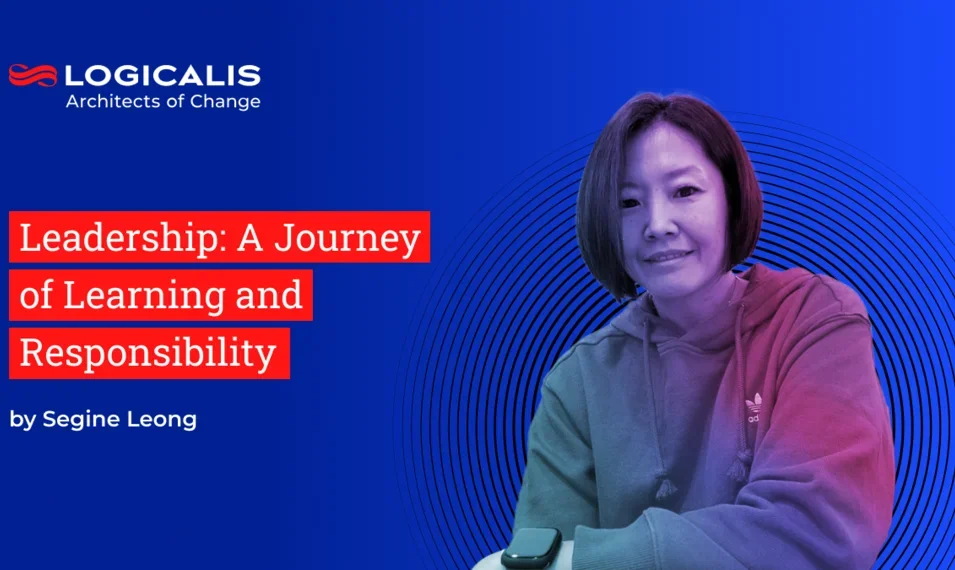
Global , Apr 29, 2025
Leadership: A journey of learning and responsibility
Leadership is often perceived as guiding a team toward success, making critical decisions, and ensuring smooth operations. However, in my experience, leadership is much more than that. It’s about learning, adapting, and taking responsibility—not just for yourself but for the team as a whole.
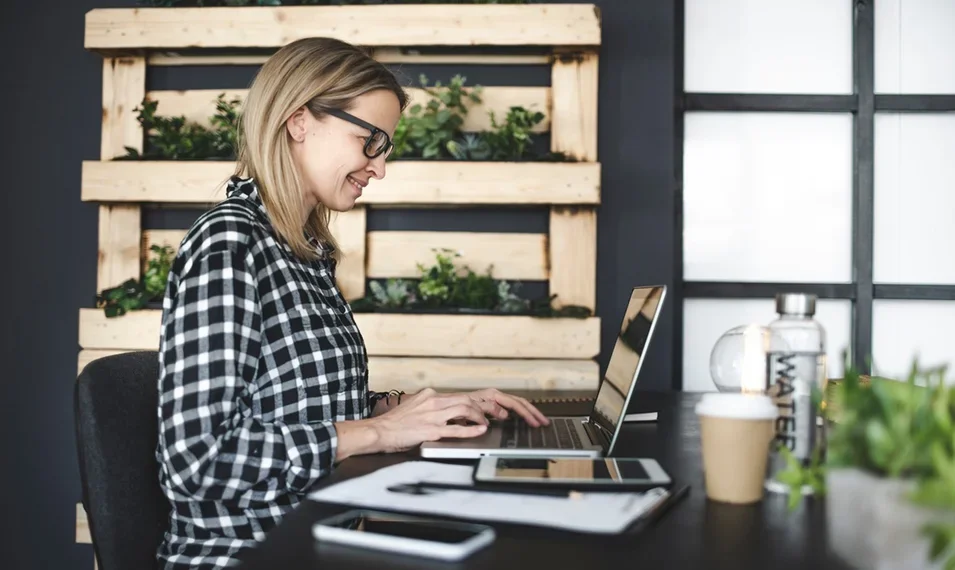
Global , Apr 24, 2025
Driving Sustainability Forward: The Power of Innovative Partnerships
Sustainability is a journey requiring continuous innovation and collaboration. In this article, Cisco discusses how its partners, including Logicalis, drive meaningful change with unique solutions to support business needs and sustainability goals.
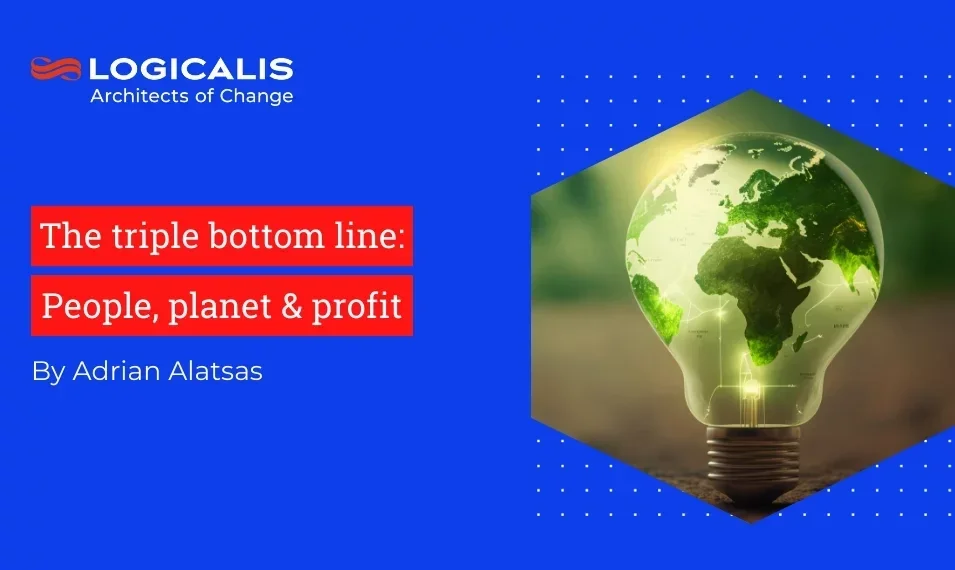
Global , Apr 23, 2025
The triple bottom line: People, planet and profit
Leading the charge in sustainability not only benefits the planet but also affects people and profits, aligning with the concept of the triple bottom line. This mindset is not exclusive to IT; anyone, from plumbers to software developers, can adopt a more sustainable mindset to minimise environmental impact.
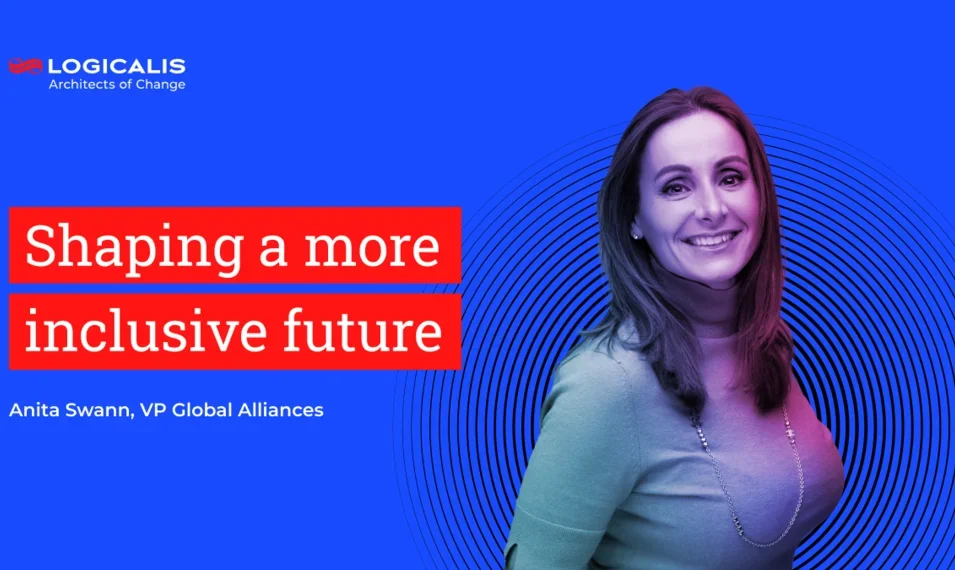
Global , Apr 23, 2025
Shaping a more inclusive future
Technology is a cornerstone of the modern world, yet the industry remains dominated by men, with women only making up a fraction of overall leadership positions. The question is, how can technology truly serve everyone if half the population it serves are underrepresented in shaping its future?
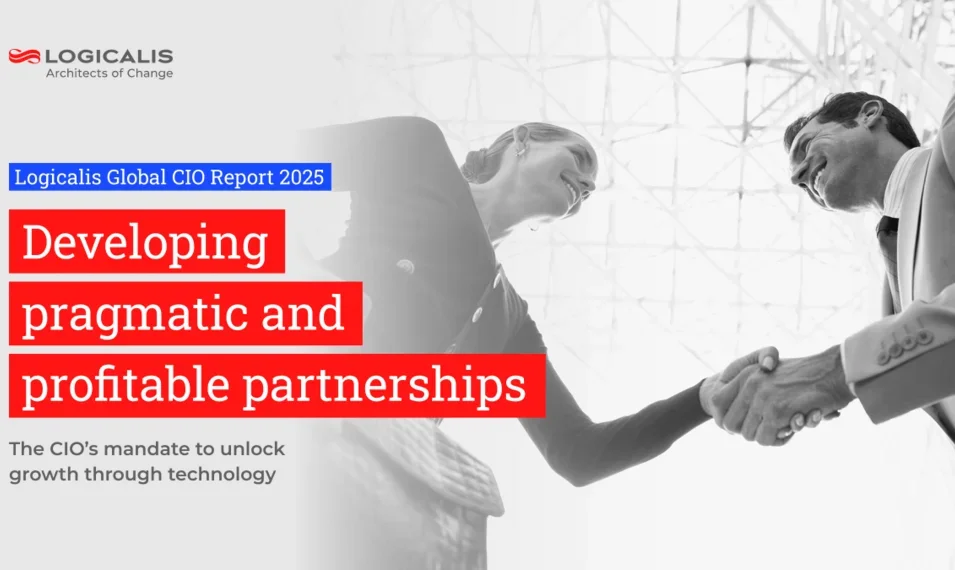
Global , Apr 10, 2025
Developing pragmatic and profitable partnerships
Technology partnerships are essential in this evolving landscape. While many CIOs believe vendors understand their business needs, 59% find vendor solutions are too complex to manage effectively.
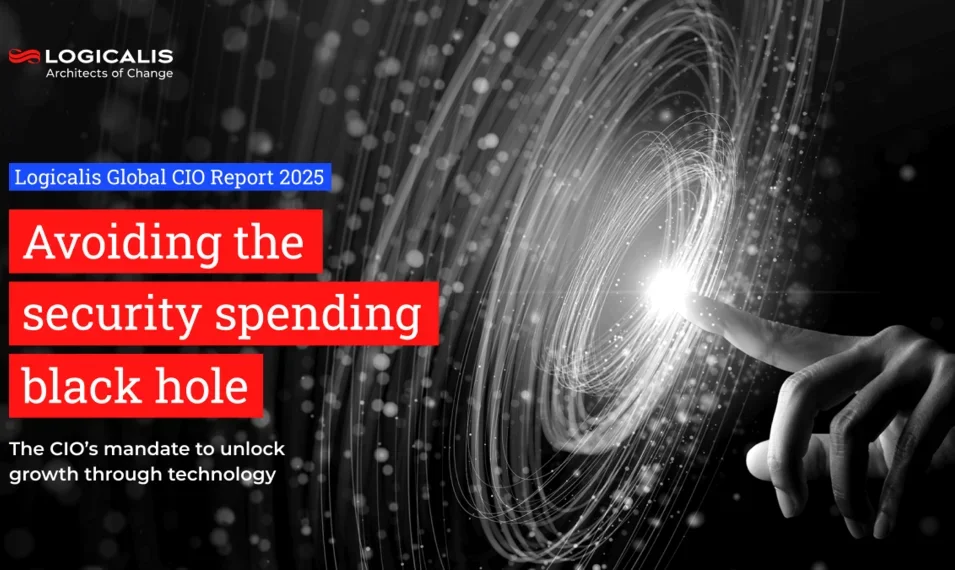
Global , Apr 10, 2025
Avoiding the security spending black hole
The Logicalis Global CIO Report 2025 uncovers a paradox that increased spending has not reduced the frequency of security breaches.
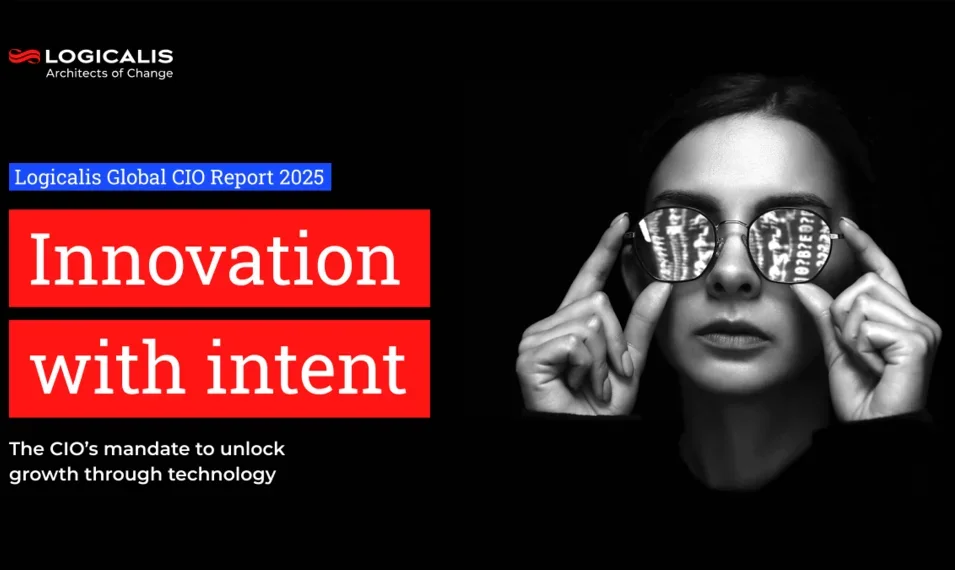
Global , Apr 10, 2025
Innovation with intent: The CIO's mandate to unlock growth through technology
Emerging technologies such as AI, machine learning and IoT are becoming central to business transformation. The Logicalis CIO Report 2025 reveals a growing emphasis on demonstrating tangible business impact.
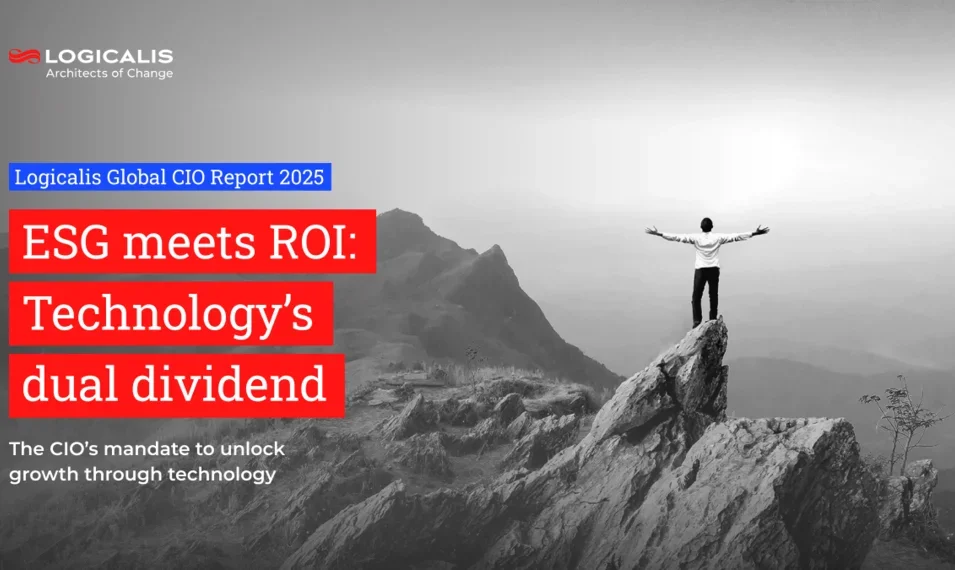
Global , Apr 9, 2025
ESG meets ROI: Technology's dual dividend
The increasing intersection of environmental sustainability and business performance has led to 91% of organisations surveyd in the Logicalis CIO Report 2025 reporting that they have experienced financial benefits form adopting environmental technologies.
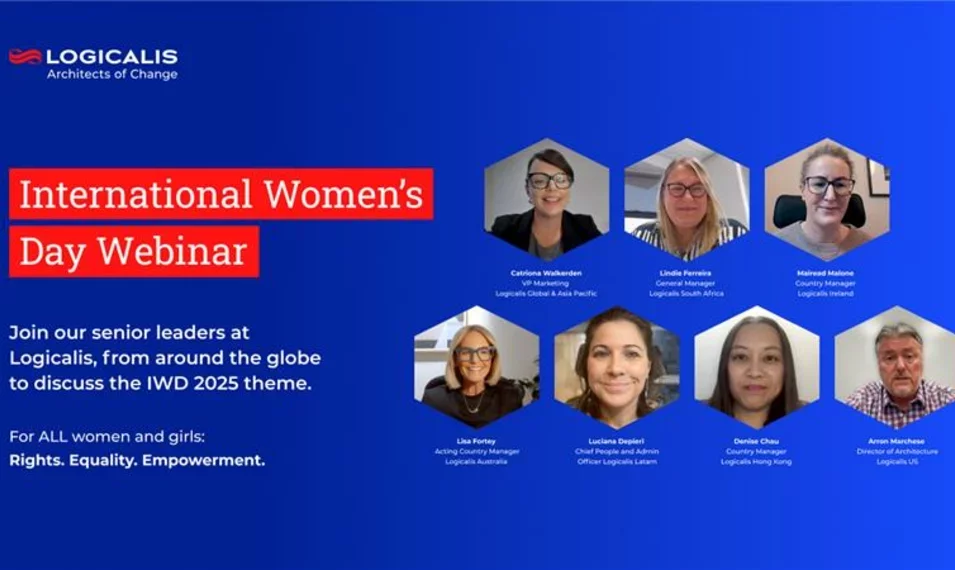
Global , Mar 17, 2025
Blog, Videos
Celebrating International Women's Day 2025
To celebrate IWD 2025, we hosted a webinar with senior leaders across Logicalis to discuss rights, equality and empowerment for women.

Global , Feb 7, 2025
Introducing Logicalis’ Interim Responsible Business Leader
Logicalis has a new Interim Responsible Business leader, Nick Zinzan. Read this Q&A session to understand more about his background and his key focus for Logicalis' key sustainability goals for 2025.
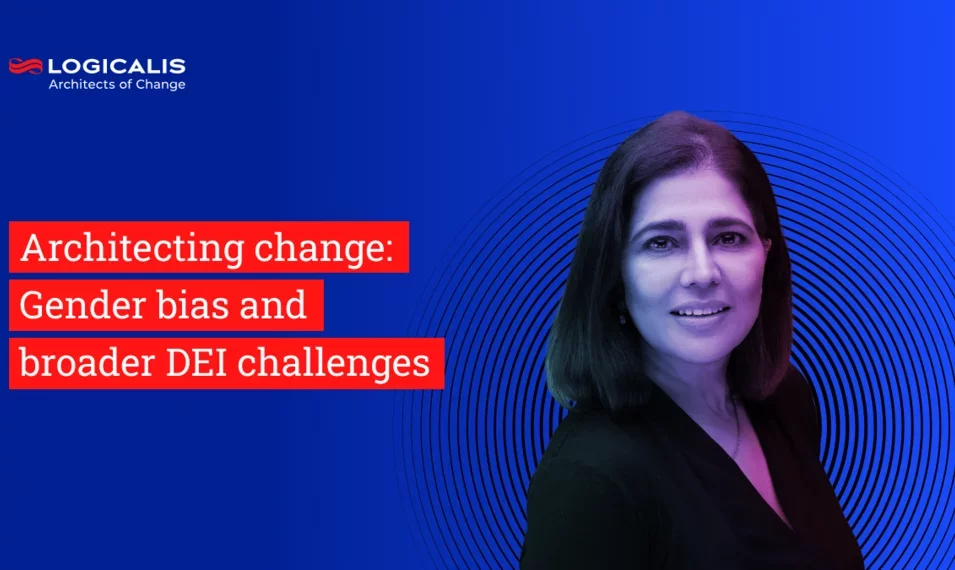
Global , Jan 14, 2025
Architecting change: Gender bias and broader DEI challenges
In this article, Dina Knight, CPO Logicalis shares her personal and professional experience with gender bias, wider DEI industry challenges, and practical examples of how to architect change towards true inclusivity.
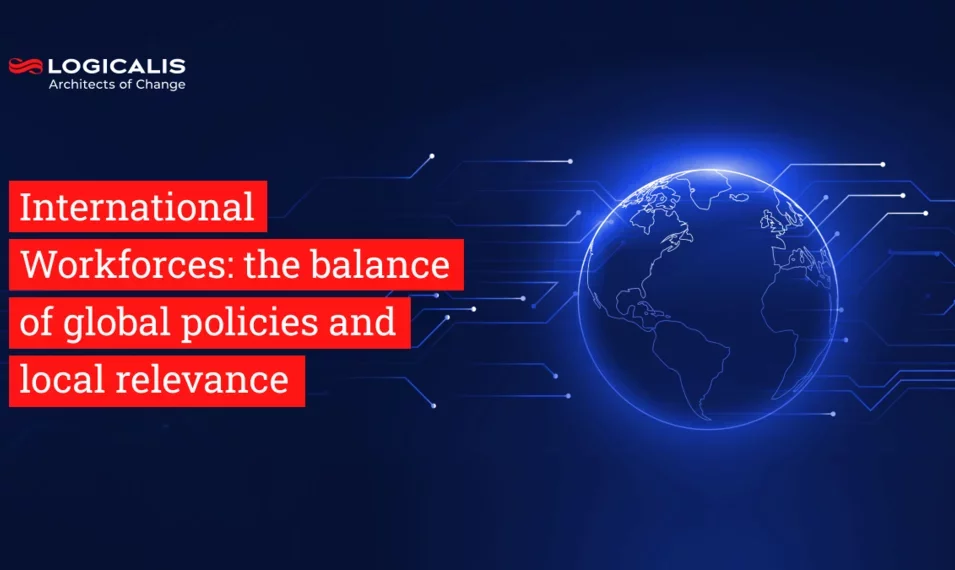
Global , Dec 6, 2024
International Workforces: the balance of global policies and local relevance
Speaking to HR World, our CPO Dina Knight shares valuable insights about successfully managing and nurturing diverse multicultural workforces.
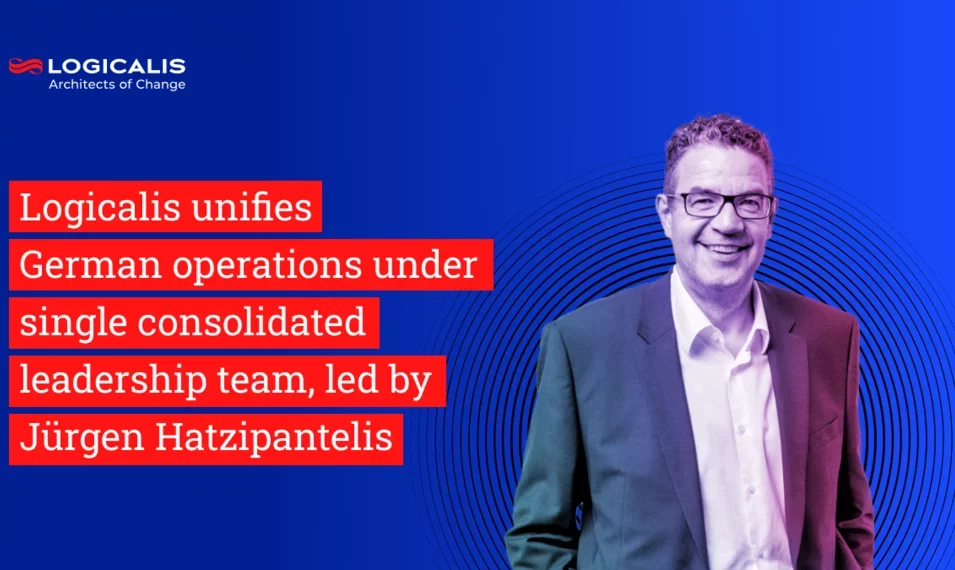
Global , Dec 4, 2024
Press Release, In the news
Logicalis unifies German operations under single consolidated leadership team
Logicalis announce a new structure for operations in Germany with the goal of leveraging their collective capabilities across the region.
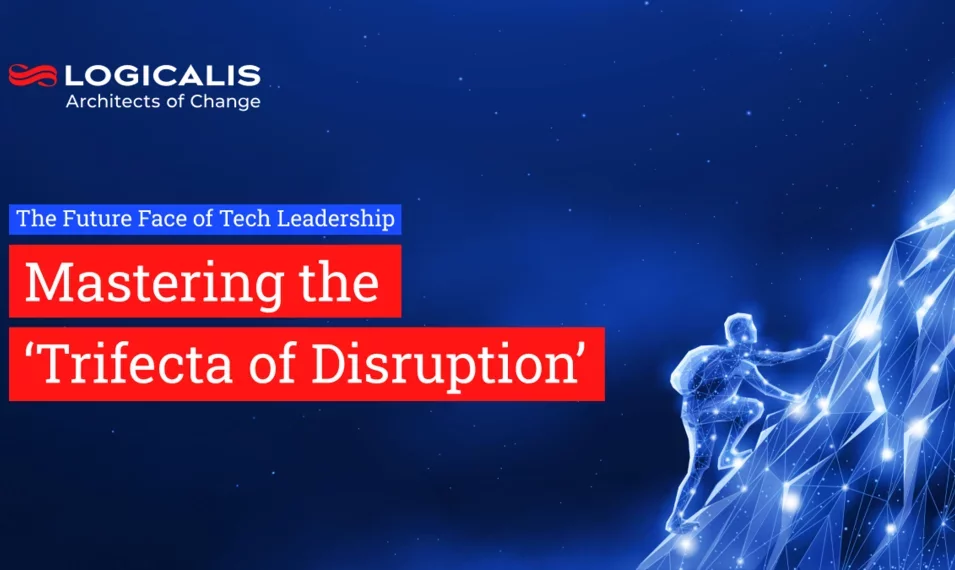
Global , Nov 28, 2024
Future Face of Tech Leadership: Mastering the ‘Trifecta of Disruption’
"Disruption is redefining tech leadership, with regulation emerging as a critical new force," according to Logicalis CEO Robert Bailkoski.
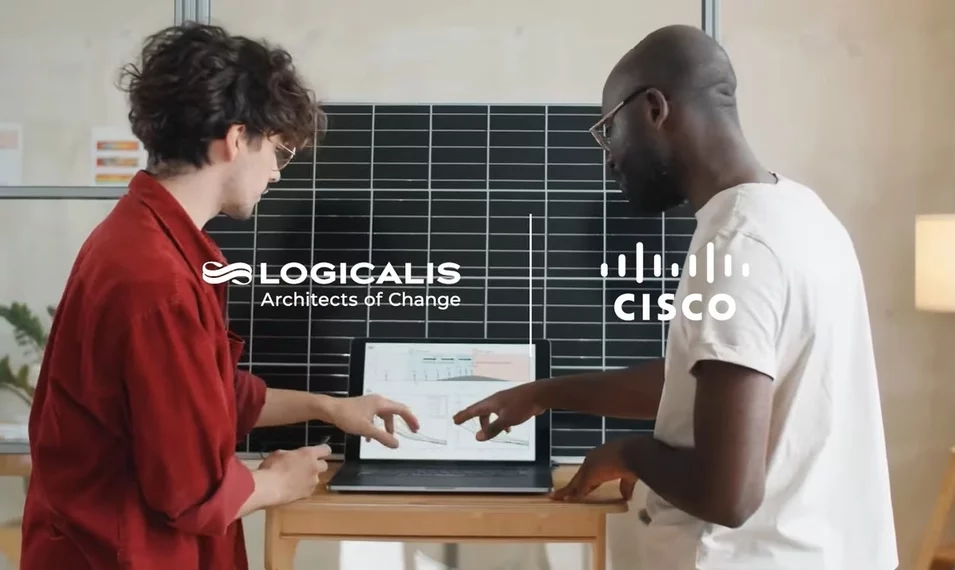
Global , Nov 11, 2024
In the news
Logicalis becomes the first global partner to launch Cisco XDR
Watch as Cisco's VP of Product Management for Threat Detection and Response, AJ Shipley, and Logicalis' CTO, Toby Alcock, discuss the significance of Logicalis being the inaugural partner to introduce Cisco (XDR) as a Managed Service (MXDR)
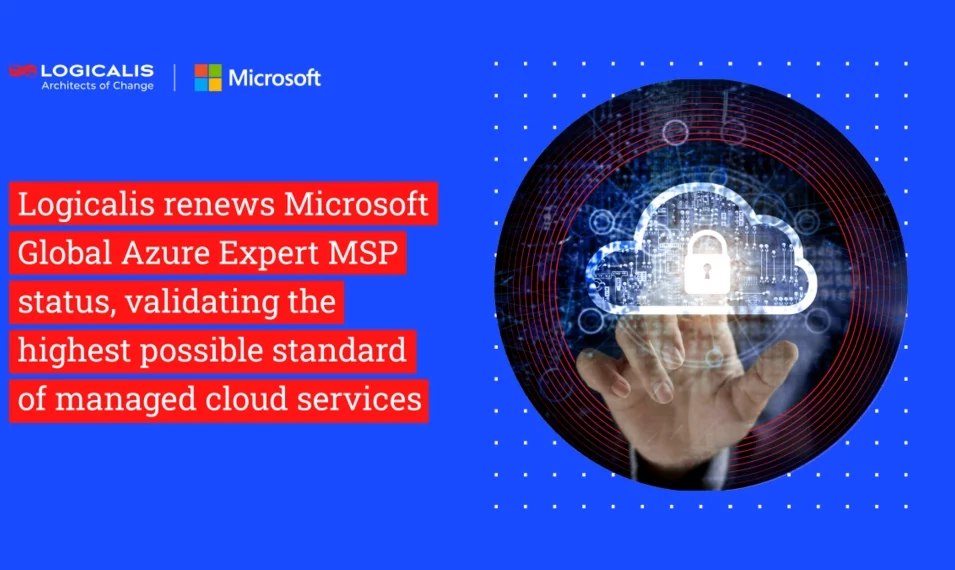
Global , Nov 5, 2024
In the news, Blog
Logicalis renews Microsoft Global Azure Expert MSP status
Logicalis are proud to announce they have renewed the prestigious Global Azure Expert Managed Service Provider (AEMSP) certification, validating the highest possible standard of managed cloud services.
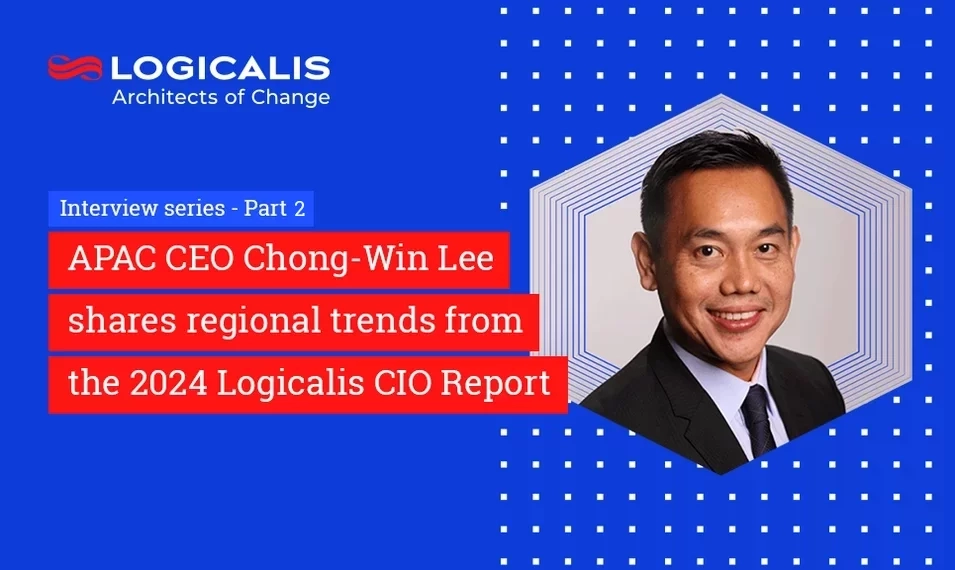
Global , Sep 30, 2024
Interview series - Part 2: APAC CEO Chong-Win Lee shares regional trends from the 2024 Logicalis CIO Report
Antoinette Georgopoulos, Content and Communications Manager at Logicalis Australia, continues her interview with Chong-Win Lee (Win), CEO of Logicalis Asia Pacific.
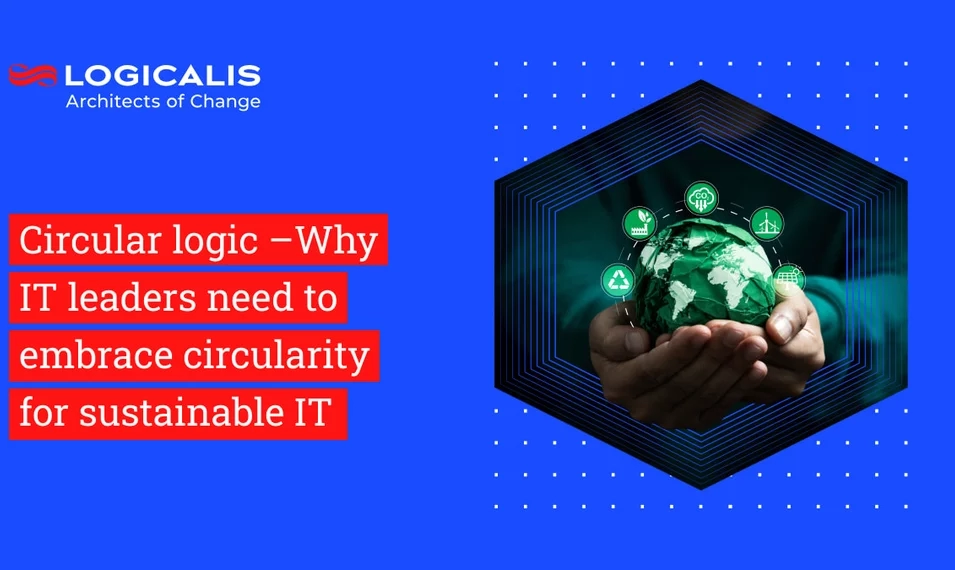
Global , Aug 28, 2024
Blog
Circular logic: Why IT leaders need to embrace circularity for sustainable IT
Discover how embracing Circular IT can transform your IT department into a sustainability powerhouse. This article explores the top 5 ways IT leaders can deliver on sustainability goals.
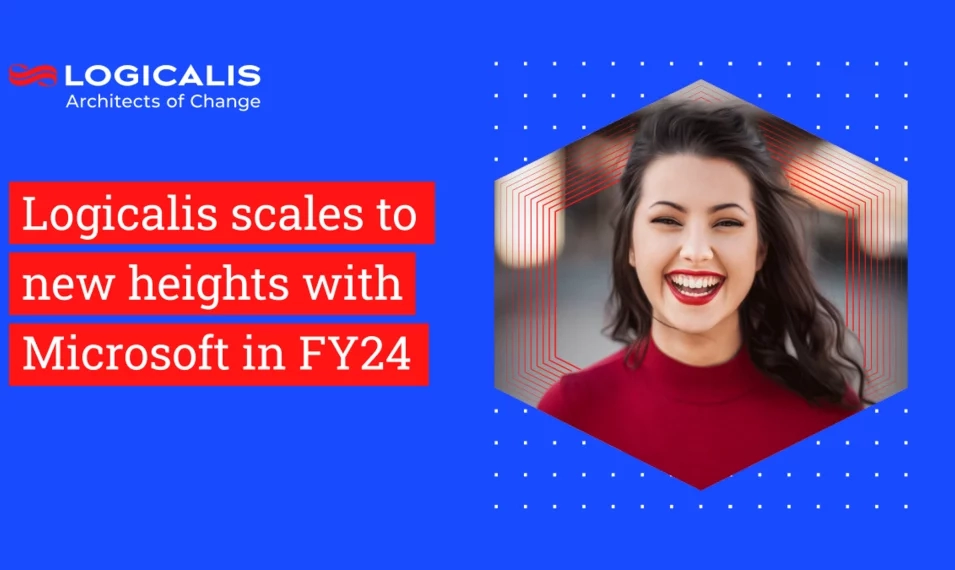
Global , Aug 8, 2024
Blog
Logicalis scales to new heights with Microsoft in FY24
With awards season behind us and an outstanding year of growth, customer outcomes and new capabilities, Logicalis, has received significant recognition for our outstanding partnership with Microsoft in FY24.
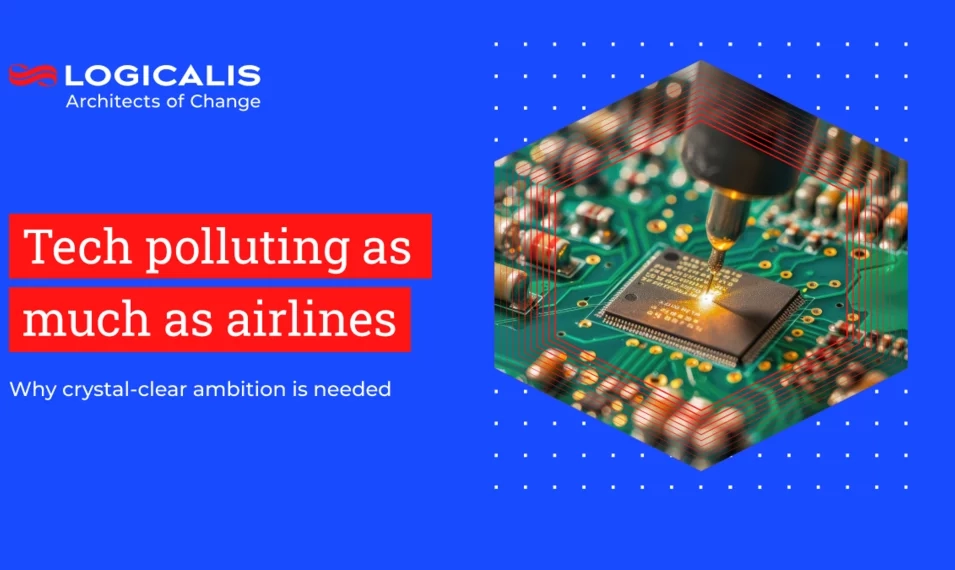
Global , Aug 6, 2024
In the news, Blog
Tech polluting as much as airlines. Why crystal-clear ambition is needed
CIOs are no longer peering into the sustainability debate from the outskirts. They are at the centre of it, driving conversations and influencing future decision-making.
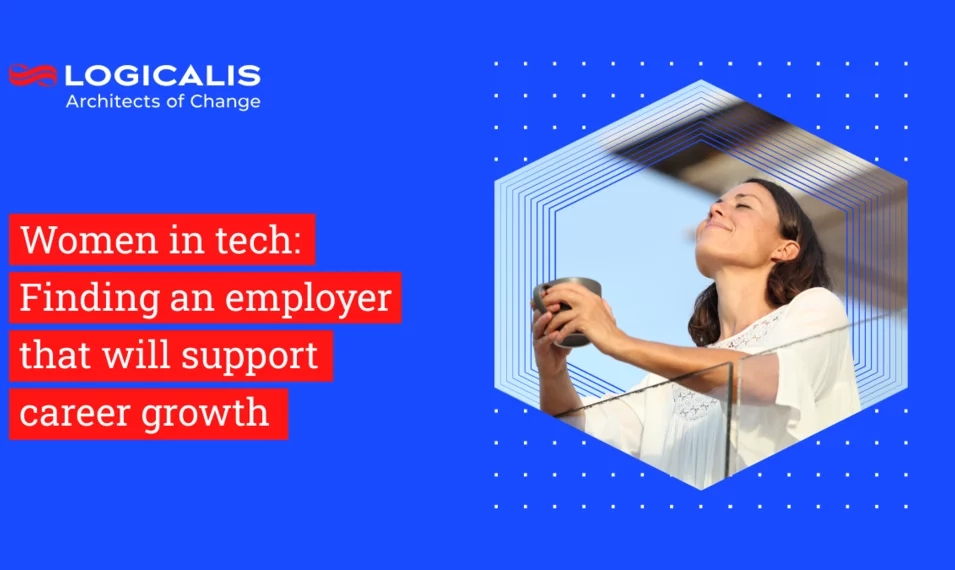
Global , Jul 31, 2024
In the news, Blog
Women in tech: Finding an employer that will support career growth
Dina Knight, CPO at Logicalis shares her insights on what women should look out for when considering organisations that will support their career growth.
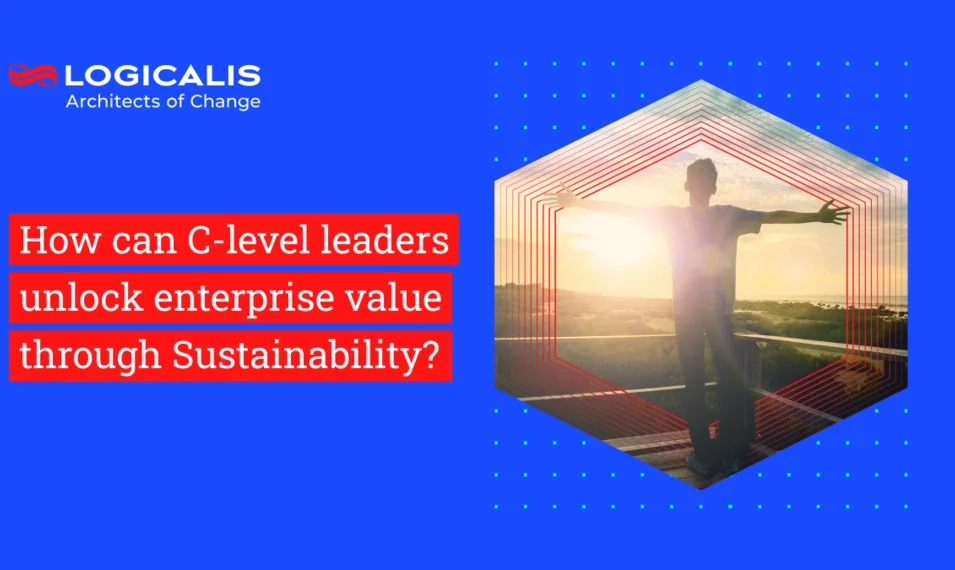
Global , Jul 31, 2024
Blog
How can C-level leaders unlock enterprise value through Sustainability?
Read how CEOs and other top executives can champion sustainable practices, to inspire the entire company to prioritise responsibility and innovation. Join our LinkedIn live - Increasing Enterprise Value through Sustainability - on Wednesday 11th September 2024.
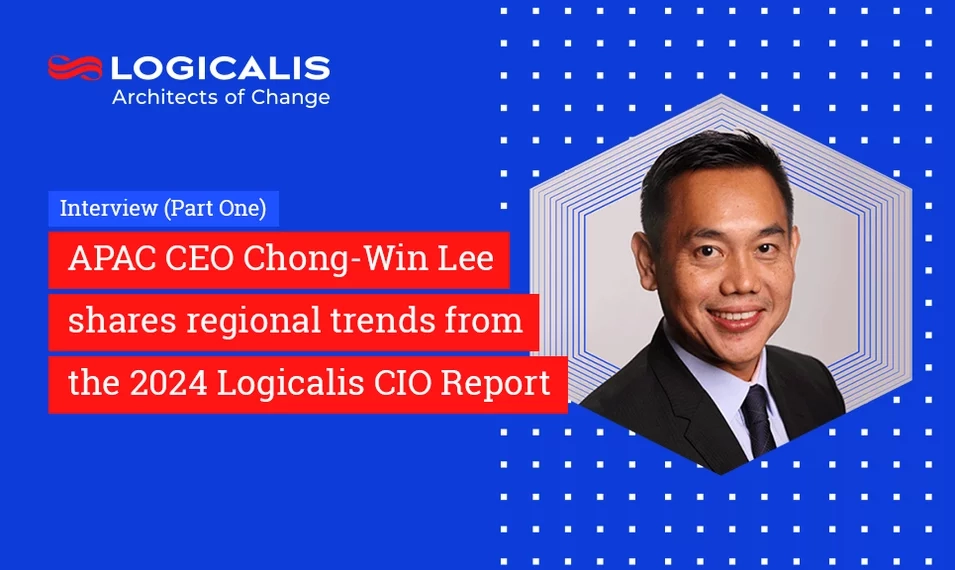
Global , Jul 31, 2024
APAC CEO Chong-Win Lee shares regional trends from the 2024 Logicalis CIO Report
Antoinette Georgopoulos, Content and Communications Manager at Logicalis Australia, caught up with Win to discuss his thoughts on the Asia Pacific trends and results from the Logicalis Global CIO Report for 2024.
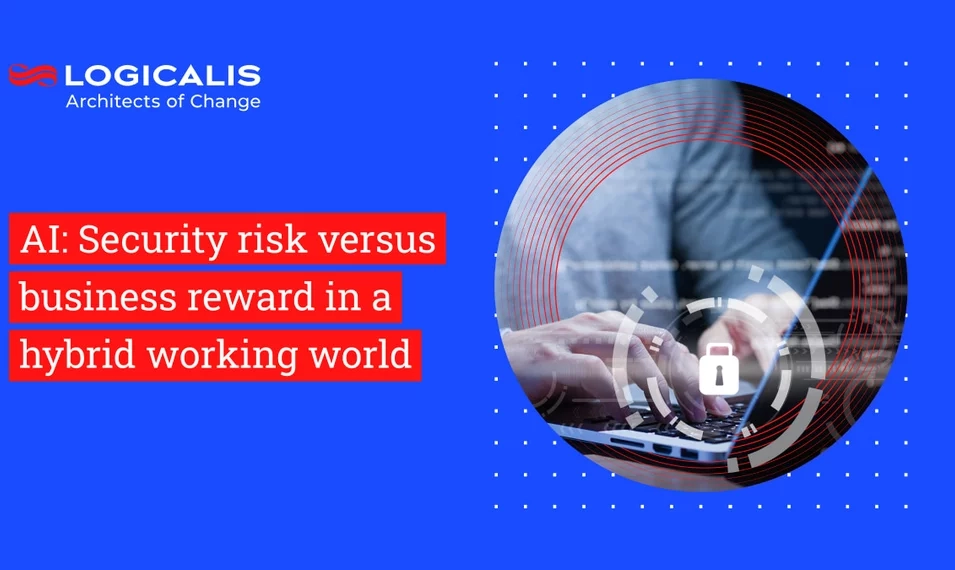
Global , Jul 22, 2024
In the news
AI: Security risk versus business reward in a hybrid working world
Protect your organisation from cyber threats with AI powered security solutions. Enable flexible working while ensuring data privacy and protection. Read Bob Bailkoski's article originally published in Forbes.
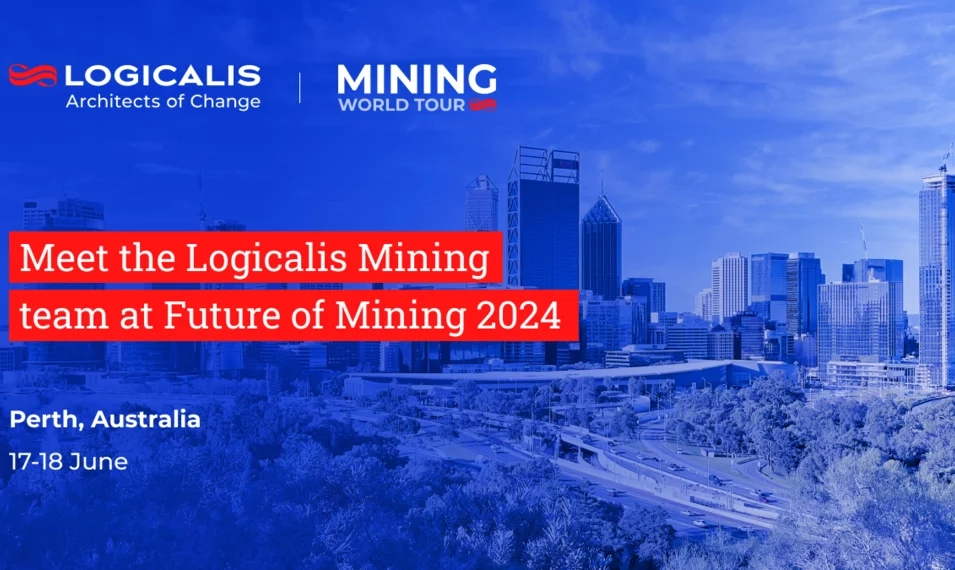
Global , Jun 14, 2024
Unlocking the future of mining: Logicalis at the Future of Mining Perth 2024
We’re thrilled to announce that Logicalis Australia will be attending the Future of Mining Conference 2024 in Perth for the very first time!
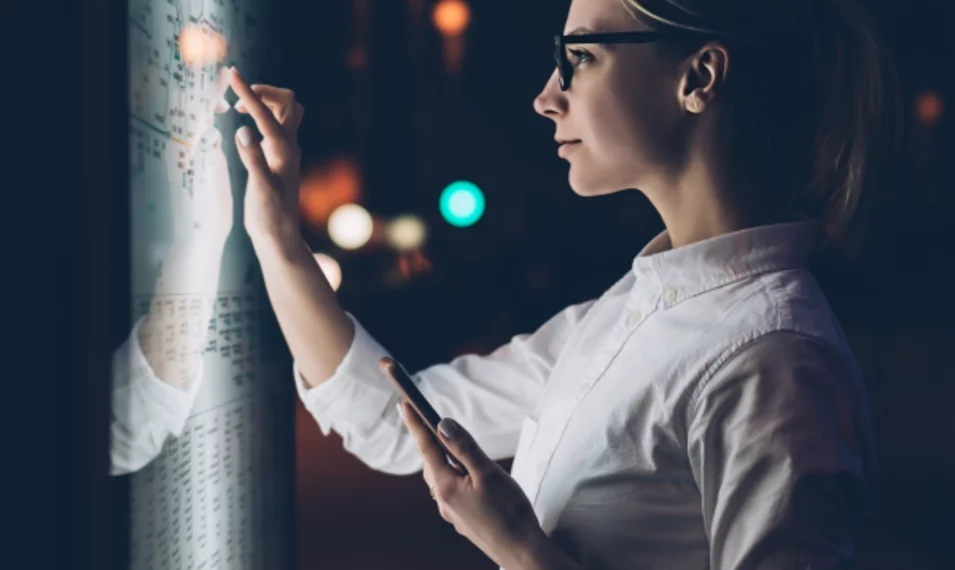
Global , May 30, 2024
How Logicalis is strengthening cybersecurity for a secure future
Discover how Logicalis' Intelligent Security solution leverages advanced technologies and proactive strategies to provide comprehensive threat protection, detection, and response capabilities for your business. Stay ahead of the ever-growing cybersecurity threat landscape.
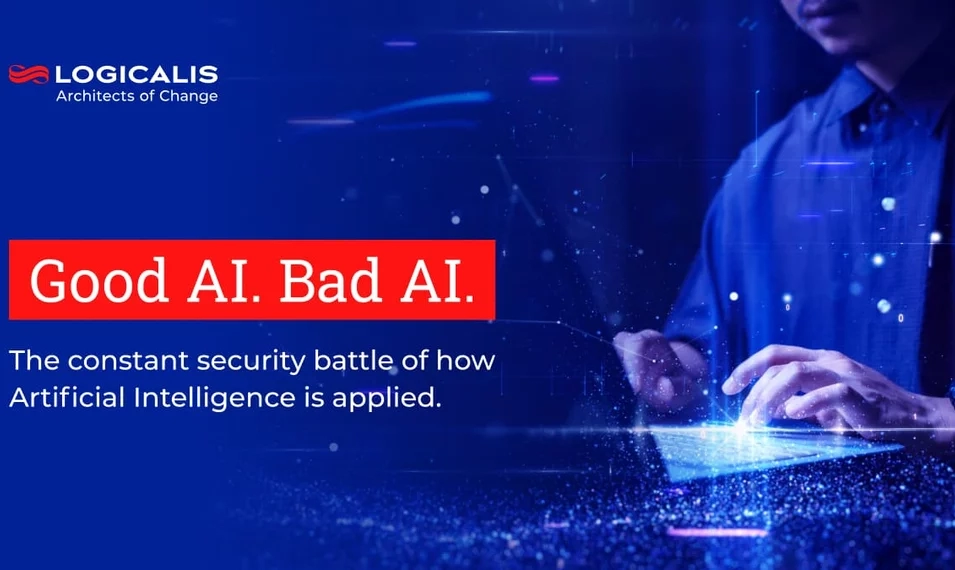
Global , May 30, 2024
Good AI. Bad AI.
Discover how AI-driven security solutions analyse network activity, detect anomalies, and predict potential exploits. Protect your business from emerging threats with our advanced AI technology.
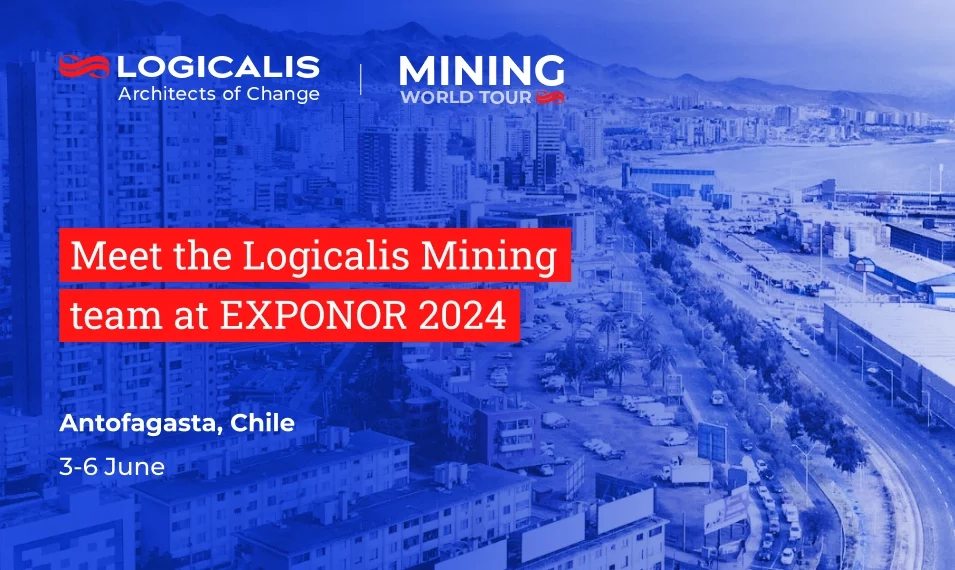
Global , May 30, 2024
Join Us at EXPONOR: Unlocking the Future of Mining
As part of our Logicalis Mining World Tour, we are thrilled to announce our participation at EXPONOR, an exhibition held in Antofagasta, Chile, to assist our mining customers in solving their most complex challenges.
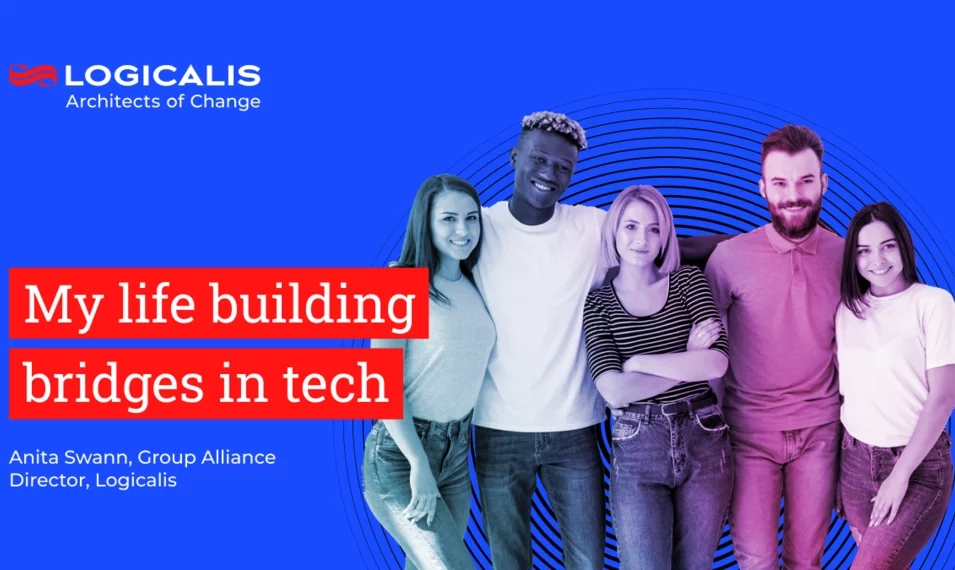
Global , May 7, 2024
My life building bridges (and opportunities) in tech
Anita Swann, Group Alliance Director, Logicalis offers her advice as to what do we need to grow the tech industry of the past into the tech industry of the future.
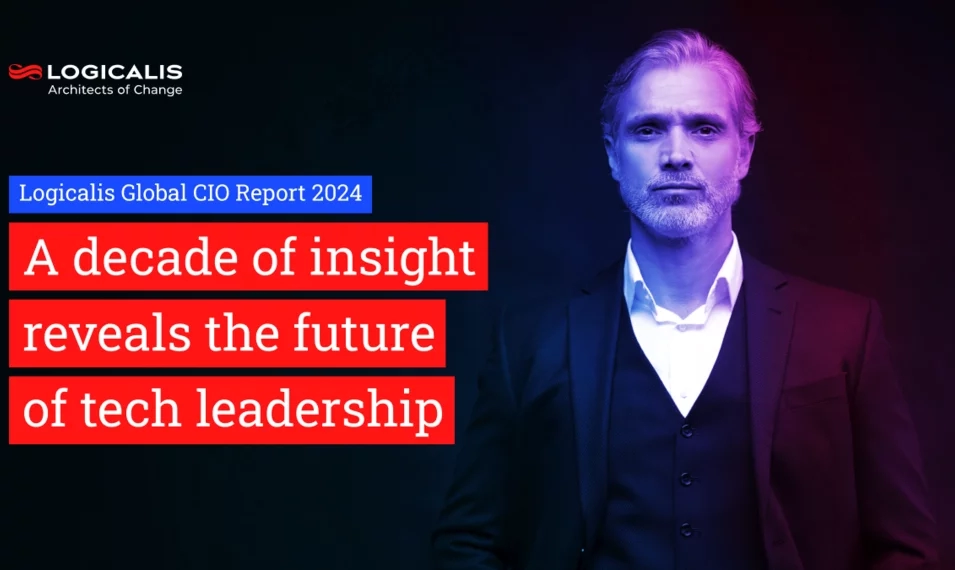
Global , Apr 12, 2024
A decade of insight reveals the future of tech leadership in the Logicalis Global CIO Report 2024
It’s been ten years since the Logicalis CIO report was launched. It was designed as a pulse check on the mood in the industry, to identify common CIO challenges and ambitions and to serve as a reminder that we are part of an ever-changing ecosystem that evolves each year.
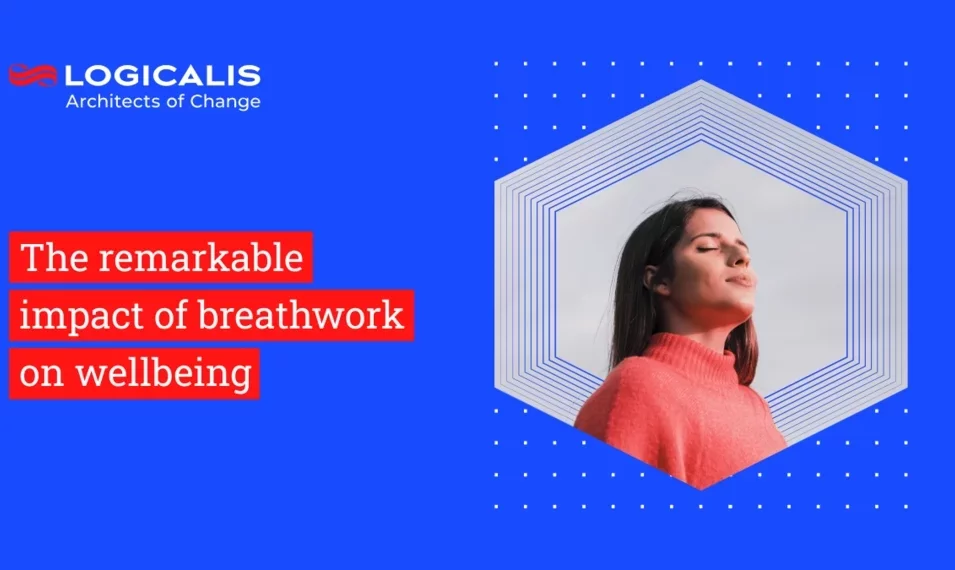
Global , Jan 31, 2024
The remarkable impact of breathwork on wellbeing
The next session in our Revive and Thrive series focuses on the damage done by stress and how we can alleviate not just stress, but also build abilities and skills that support our overall wellbeing.
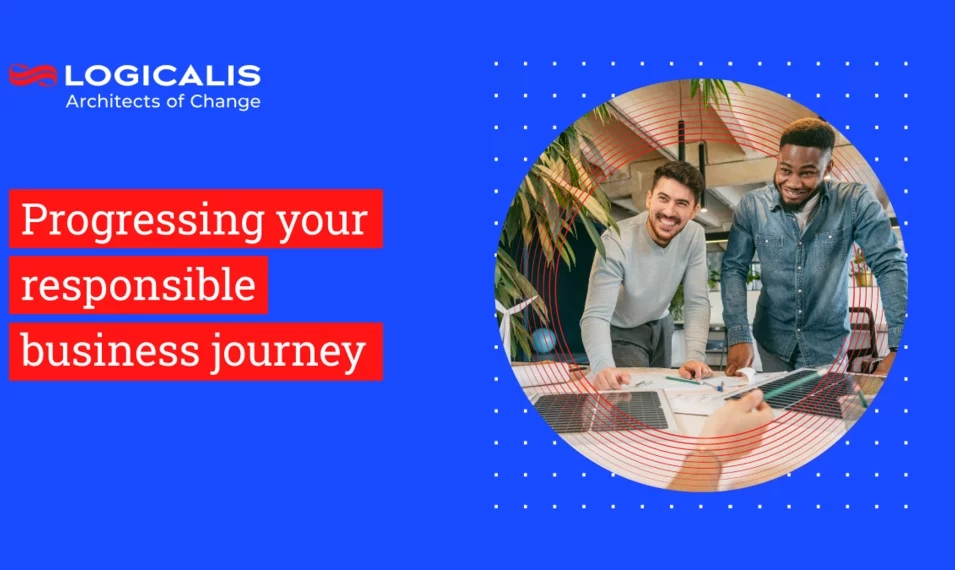
Global , Dec 11, 2023
Progressing your responsible business journey
Our responsible business agenda has been shaped by understanding who we are as a business, which social and environmental challenges are important to our customers, partners, people and in the regions that we operate in.
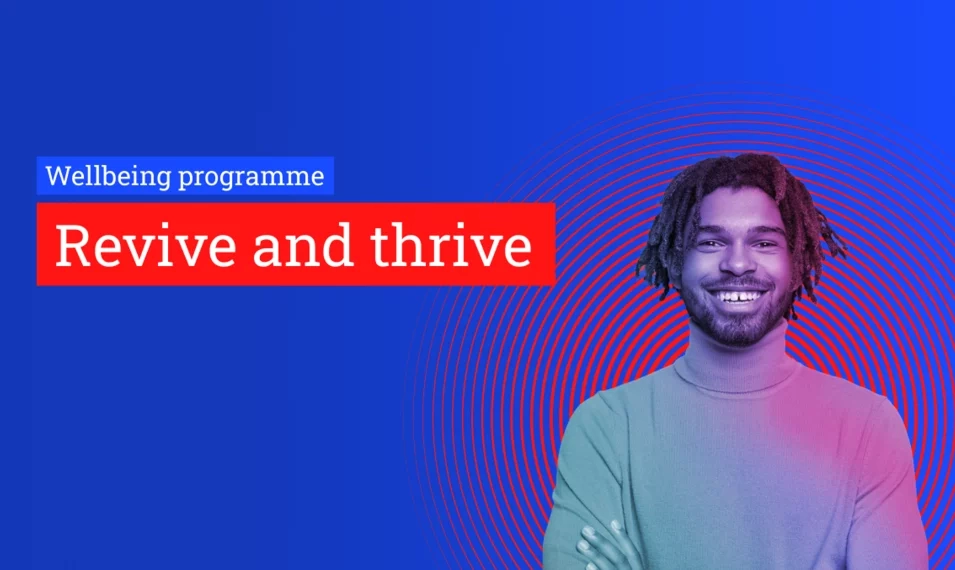
Global , Dec 11, 2023
Inclusion starts with me
Investigating making the invisible visible, the first session in our Revive and Thrive series provided an understanding of how we can look after each other's mental health by changing behaviours, from unconscious bias to consciously include people.
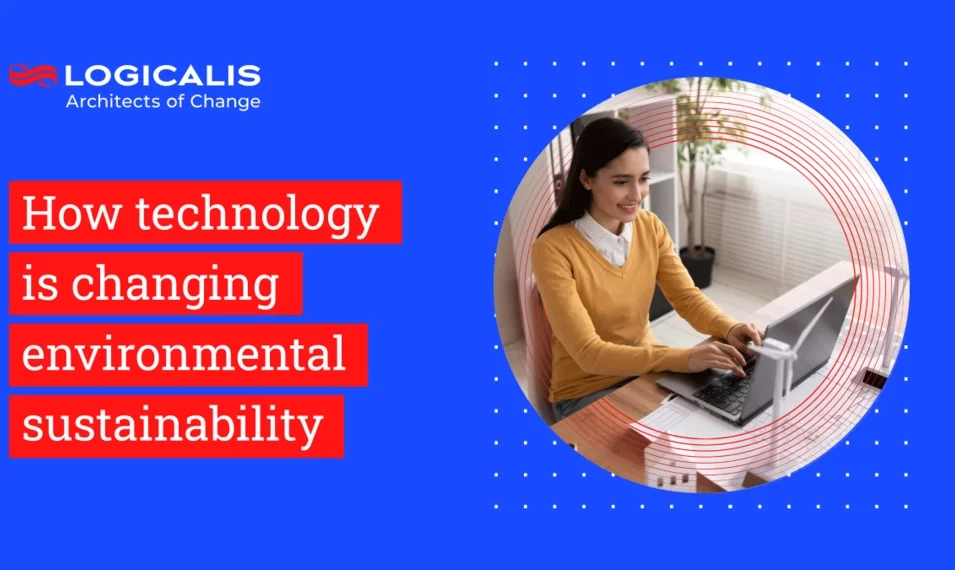
Global , Nov 23, 2023
How technology is changing environmental sustainability
The enablement of sustainability strategies through technology and IT, in this instance is what can truly enable business growth and ESG performance, and there are several ways that they tie together.
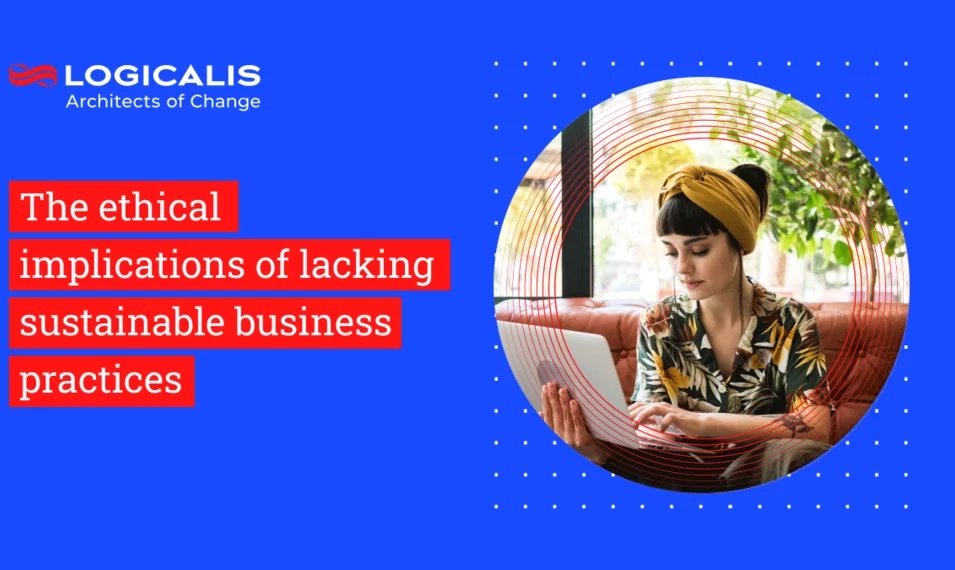
Global , Nov 15, 2023
The ethical implications of lacking sustainable business practices
A sustainable society is one that lives within the carrying capacity of its natural and social systems, but as the impact of businesses on the environment has increased dramatically, that balance for a sustainable society has tipped.
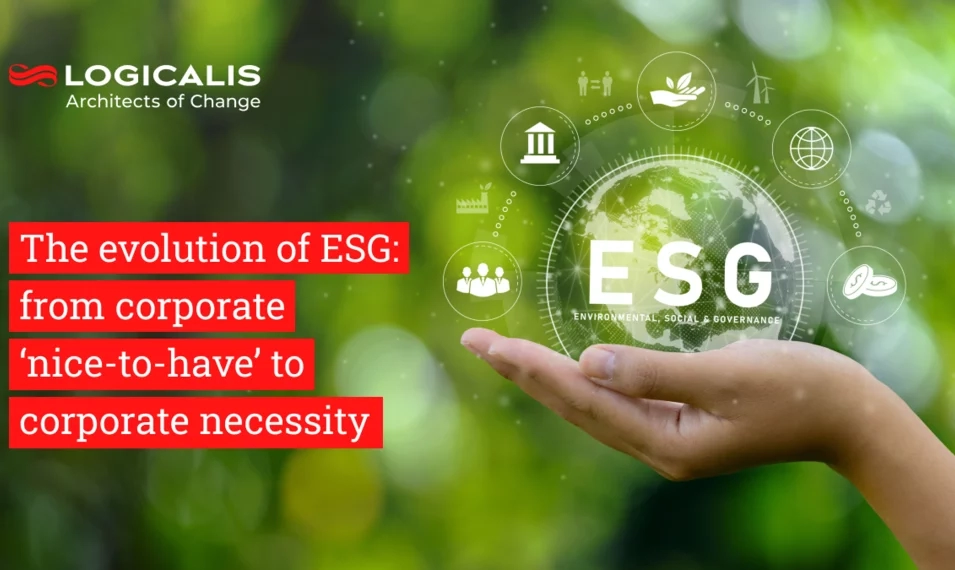
Global , Oct 26, 2023
The evolution of ESG: from corporate 'nice-to-have' to corporate necessity
Corporate sustainability has become more than a “nice to have”. We are seeing more and more organisations realise the urgency to act not just because of regulatory pressure, but also because they see sustainability as a way to drive business benefits. Environmental and social governance or ESG which considers sustainability policies and ethical practice, is moving out of the shadows and becoming the next big bet in business transformation providing clear shared value.
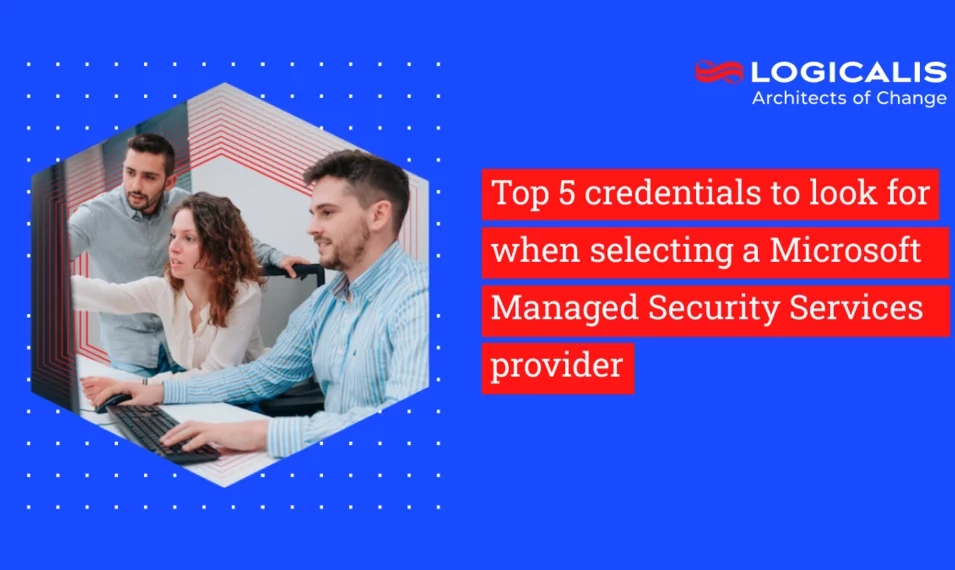
Global , Oct 18, 2023
Choosing the right MSSP -Top 5 credentials to look for when selecting a Microsoft Managed Security Services provider (MSSP)
Our recent CIO survey shows over half of respondents plan to increase their risk management investment. They also consider malware and ransomware significant risks that their organisations will face in the coming year. But what should an organisation look for in choosing the right MSSP?
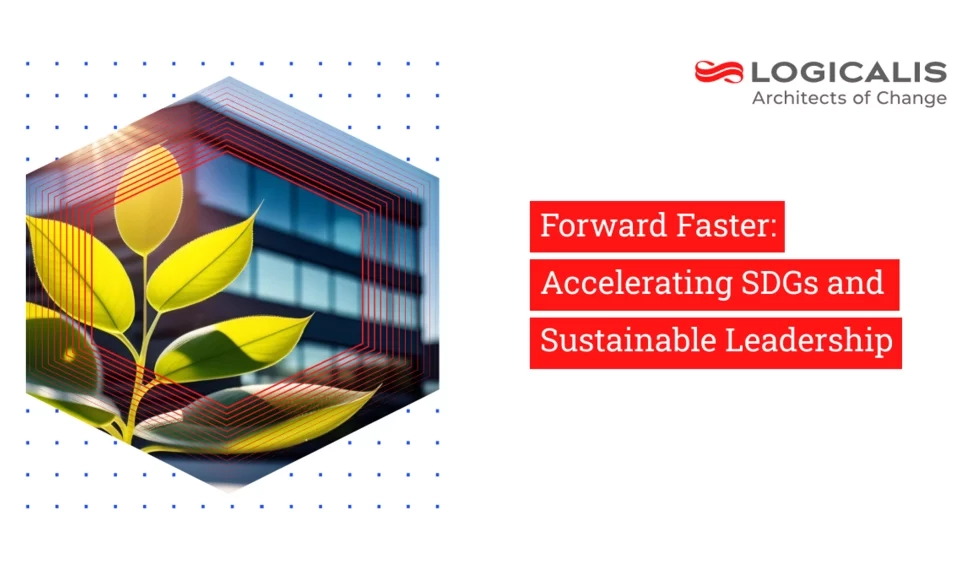
Global , Oct 16, 2023
Forward Faster: Accelerating SDGs and Sustainable Leadership
While we are working hard on our robust responsible business plan, especially with regards to our sustainability goals, there is still a long way for us all to go. Responsible Business Manager Sharon Kekana, recently participated in the UN Global Compact Leaders Summit, held at the Javits Centre in New York.
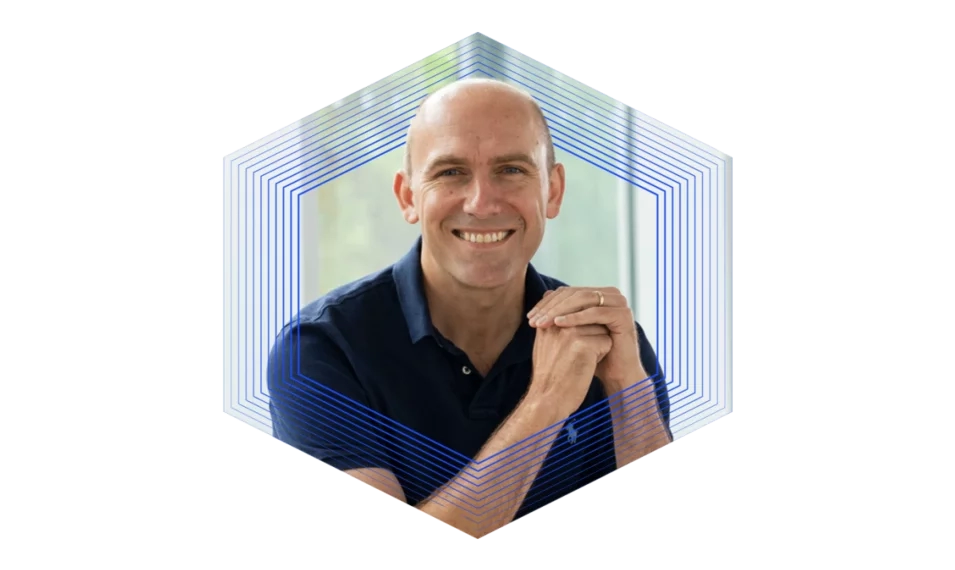
Global , Oct 5, 2023
In the news
Why the CIO is key to driving business sustainability
Sustainability initiatives in the business world, are becoming more of a requirement and technology plays a central role. Read Bob's three steps for CIOs to become leaders in driving their sustainability agendas.
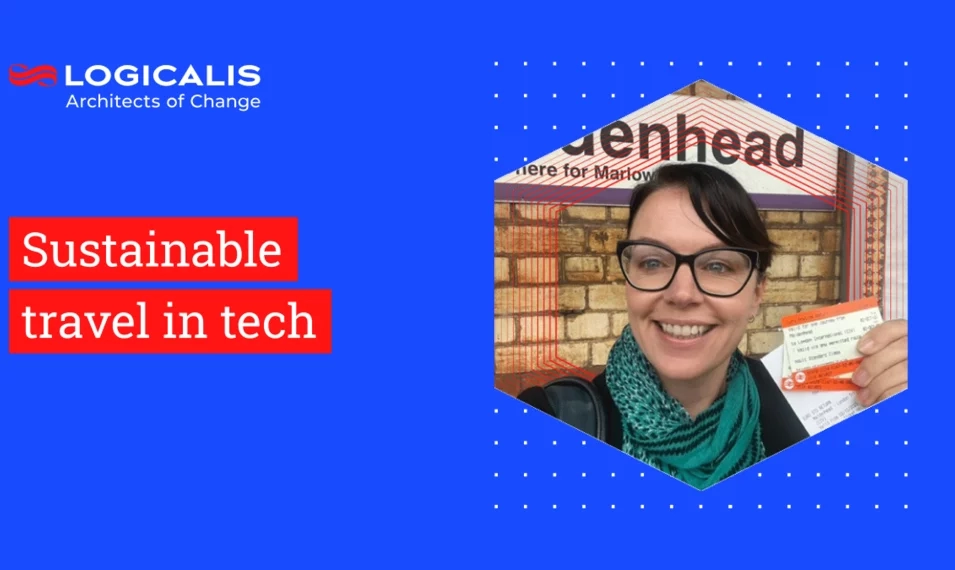
Global , Oct 4, 2023
Sustainable travel – a realistic goal in the IT industry?
Catriona Walkerden, Global VP, Marketing takes us through how the new sustainable travel policy at Logicalis influenced her recent business travel decisions. See how she got on ...
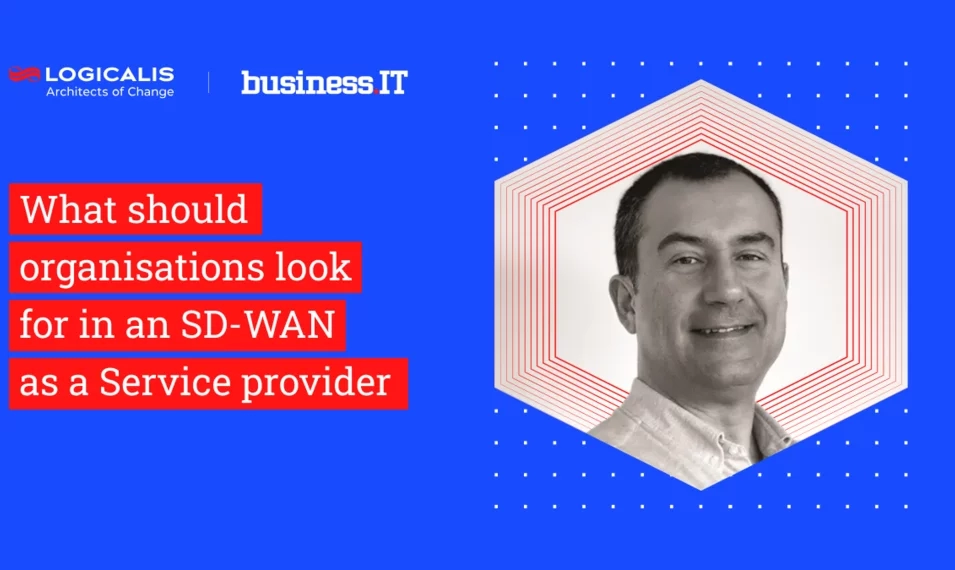
Global , Sep 21, 2023
In the news
What should organisations look for in an SD-WAN as-a-Service provider?
Pedro Morgado outlines the key factors organisations need to consider when selecting an SD-WAN solution provider.
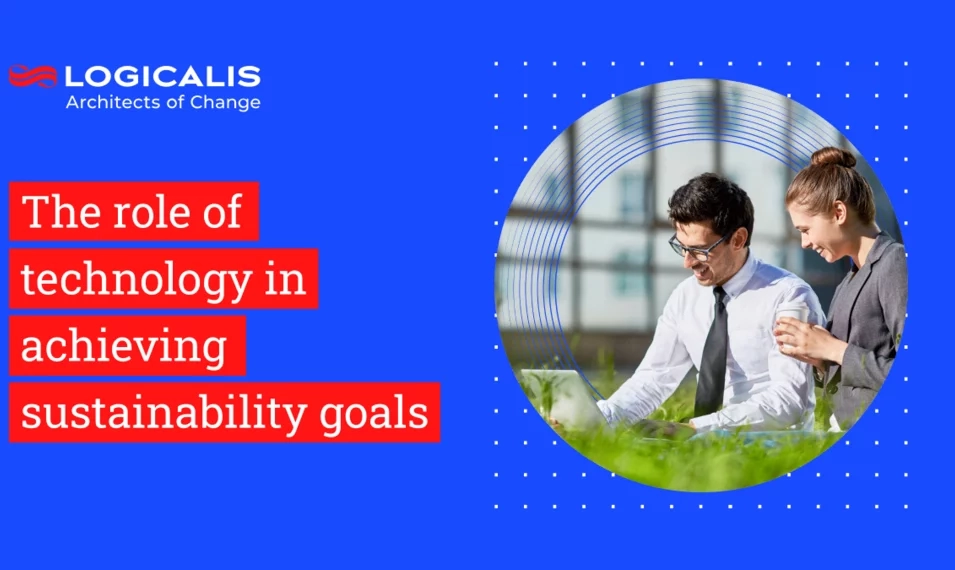
Global , Sep 18, 2023
The role of technology in achieving sustainability goals
Technology has undoubtedly revolutionised the world, however, technology and sustainable approaches are not mutually exclusive. There is a duality to technology and sustainability; while technology itself must be made more sustainable, the way we use technology may be the key to acting more sustainably and tackling the climate crisis.
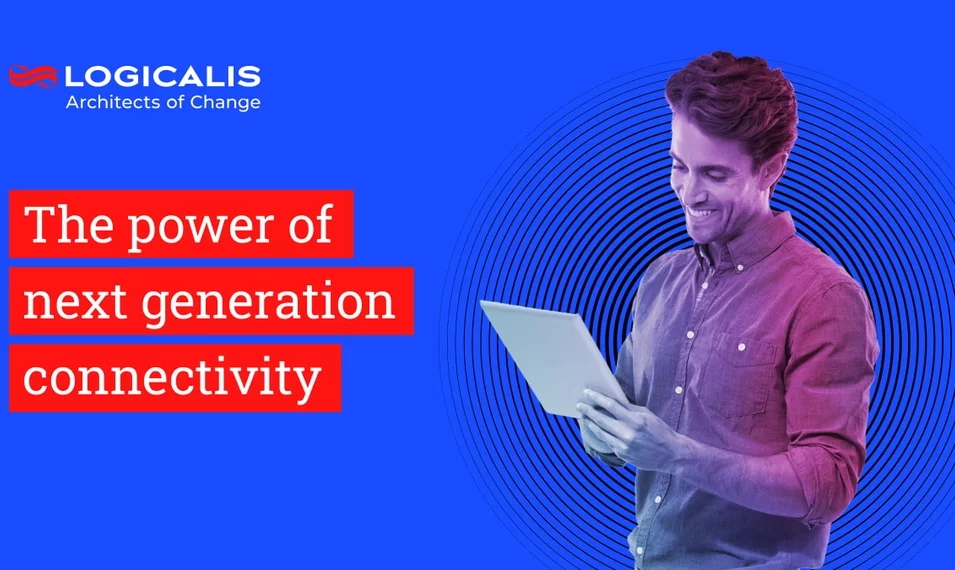
Global , Sep 4, 2023
The power of next generation connectivity
Business leaders need to create environments that can adapt to maximise opportunities, mitigate risks and most importantly be able to scale both securely and sustainably. The key to this is connectivity.
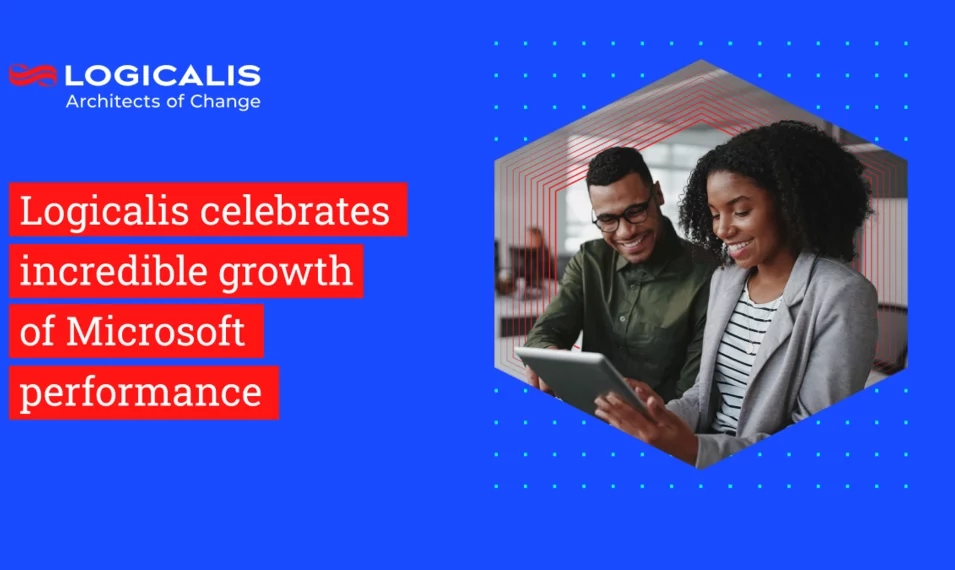
Global , Aug 4, 2023
Logicalis celebrates incredible growth of Microsoft performance
FY23 has been an extraordinary year for Logicalis’s Microsoft partnership. We’ve seen 60% year-on-year growth reflecting our unwavering commitment to helping customers deliver business value through digital transformation.
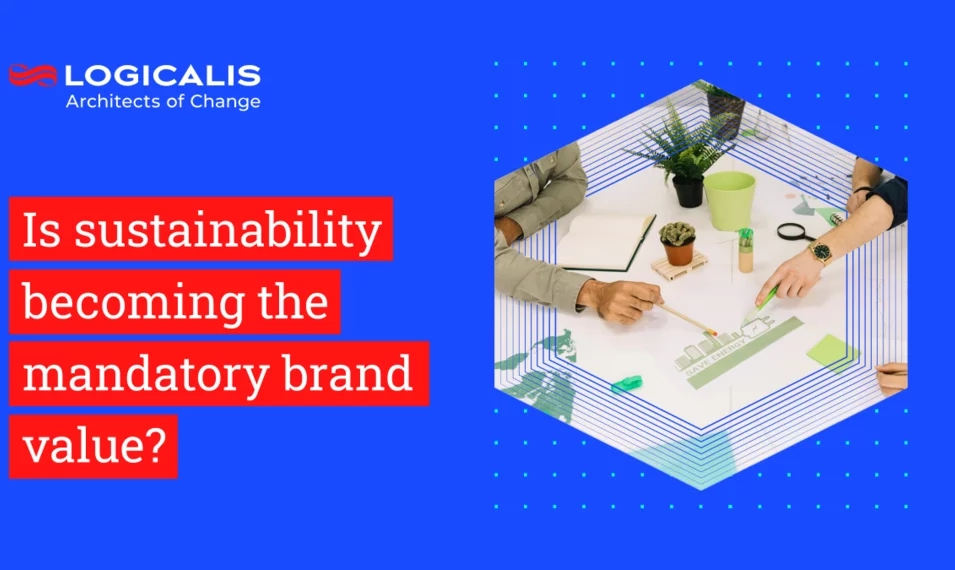
Global , Jul 14, 2023
Is sustainability becoming the mandatory brand value?
Employees and customers are looking to organisations for proactive sustainability action to help tackle the worsening climate situation. How can marketing help drive the right behaviour in organisations?
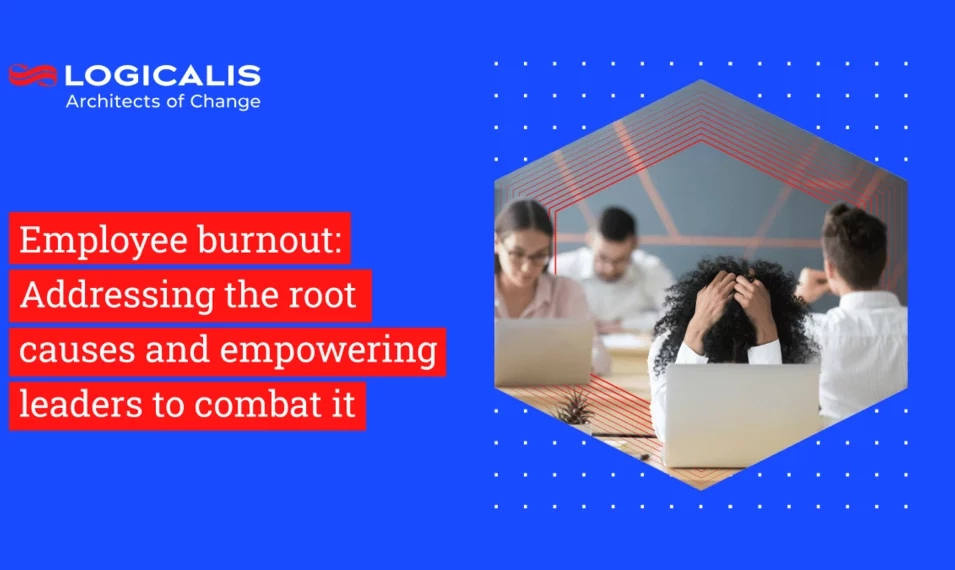
Global , Jul 10, 2023
Employee burnout: Addressing the root causes and empowering leaders to combat it
Employee burnout has become an increasingly alarming concern in recent years and it's now a necessity for modern businesses to empower leaders to proactively address burnout, creating a workplace that promotes employee well-being and productivity.
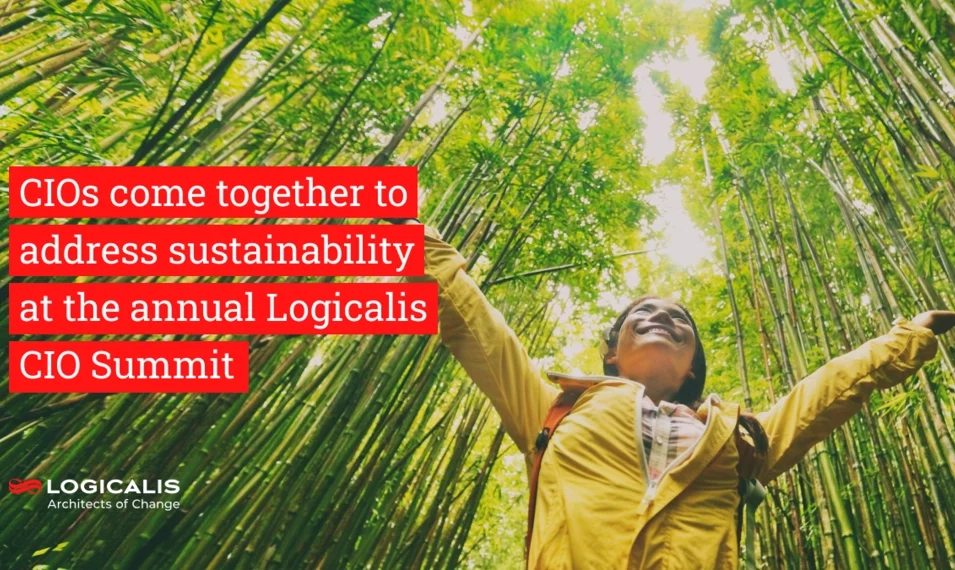
Global , Jun 30, 2023
In the news
CIOs come together to address sustainability at the annual Logicalis CIO Summit
Keynote address from Leading Analyst Firm reveals ESG is growing in importance to IT buyers but cautions against investing in tech that doesn’t deliver against goals.
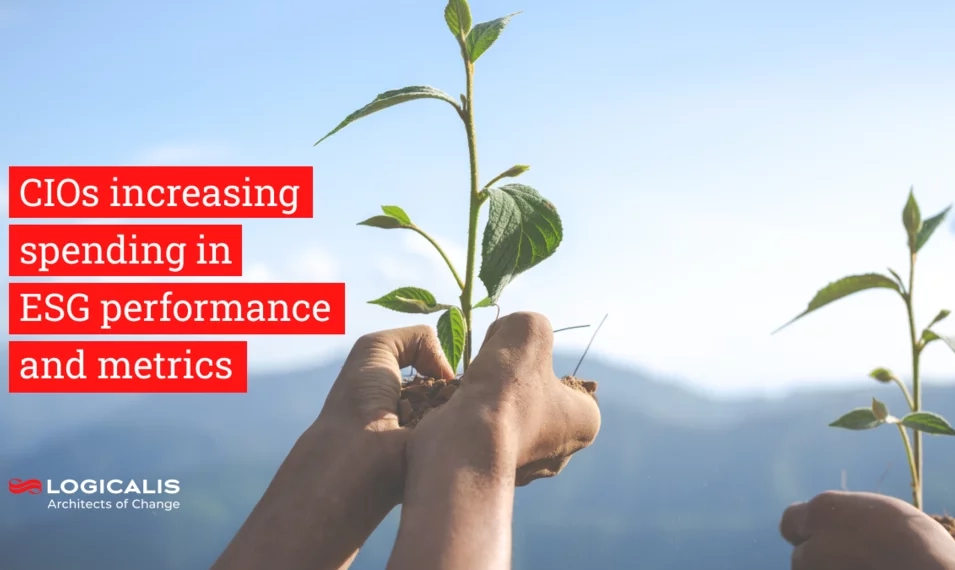
Global , Jun 30, 2023
In the news
CIOs increasing spending in ESG performance and metrics
CIOs are increasing investment in technologies that help drive business value and ESG performance and highlighted growing trends such as linking executive pay to ESG metrics, a Logicalis summit was told.
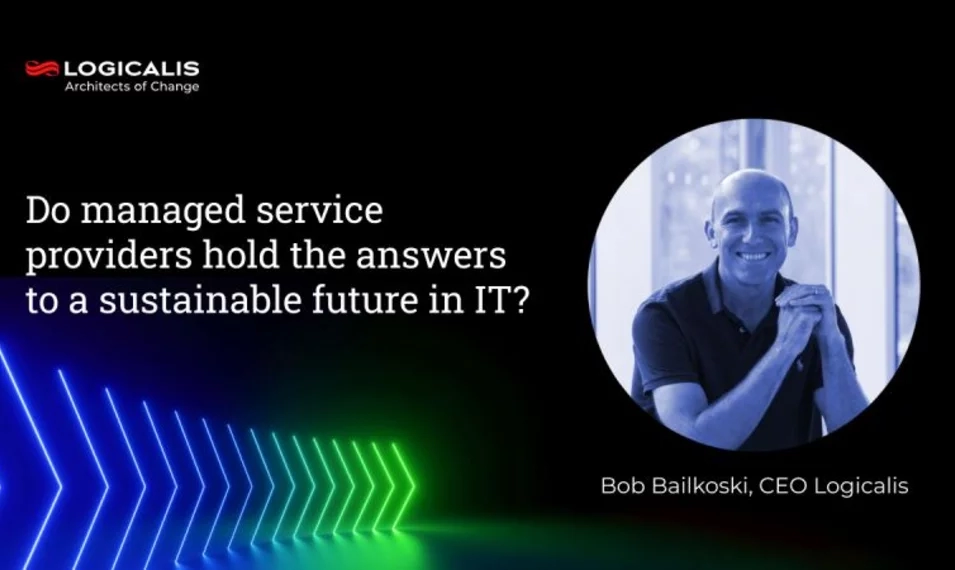
Global , Jun 2, 2023
Do managed service providers hold the answers to a sustainable future in IT?
With sustainability top of mind for everyone, organisations are demanding transparency and clarity from suppliers and partners around ESG goals today.
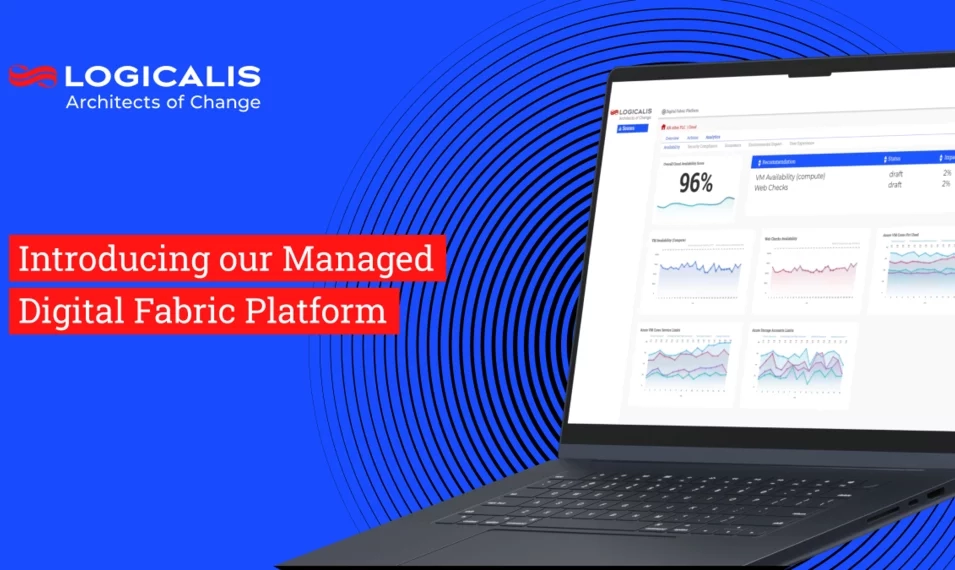
Global , May 12, 2023
Introducing our Managed Digital Fabric Platform
In response to the need to support our customers and focus on critical activities that matter, such as optimising resources and reducing costs, in 2022, we developed the Managed Digital Fabric platform. Based on machine learning and AI, The Managed Digital Fabric Platform provides our managed services customers with a real-time view of their digital infrastructure across cloud, security, workplace, and connectivity.
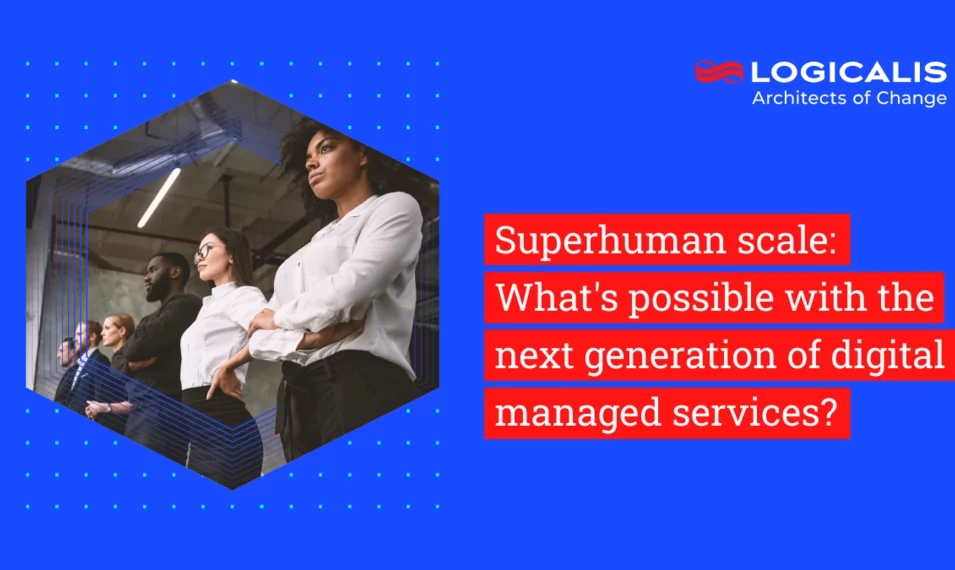
Global , May 9, 2023
Superhuman scale: What's possible with the next generation of digital managed services?
The era of digital managed services is upon us, offering superhuman scale for an organisation’s technology ecosystem. What can you expect from this new generation of digital MSPs? Markus Erb, VP of Services for Logicalis, shares his insights on the possible.
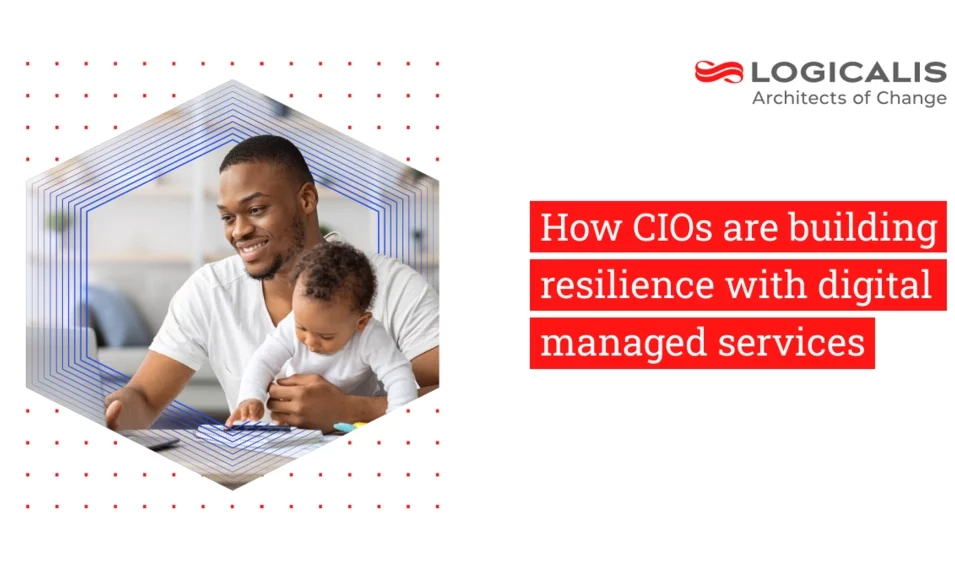
Global , Apr 3, 2023
How CIOs are building resilience with digital managed services
This blog explores how CIOs are building resilience with digital managed services.
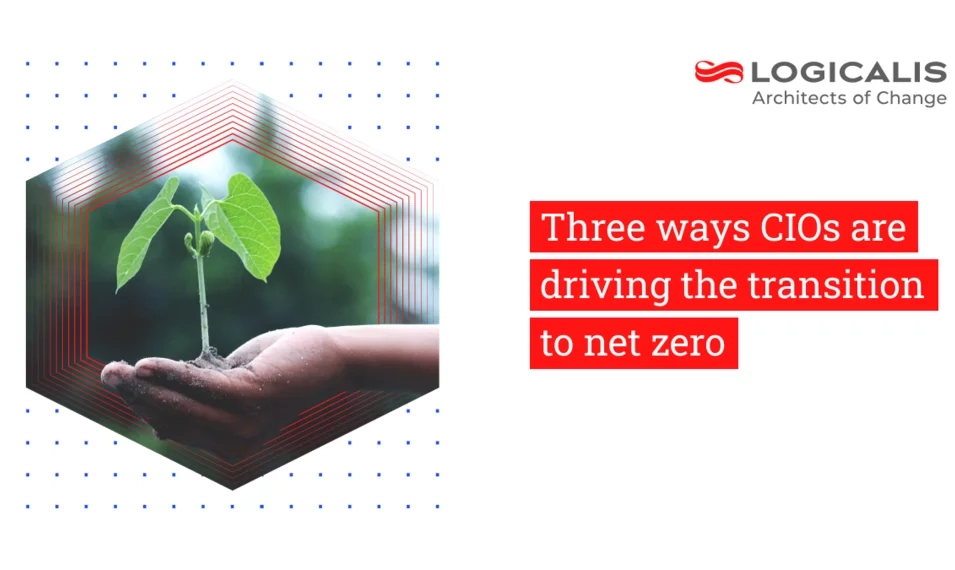
Global , Apr 3, 2023
Three ways CIOs are driving the transition to net zero
The transition to net zero offers a great opportunity for CIOs to increase their strategic influence across the business. The Logicalis Global CIO Report 2023 identified three ways CIOs are driving the transition to net zero.
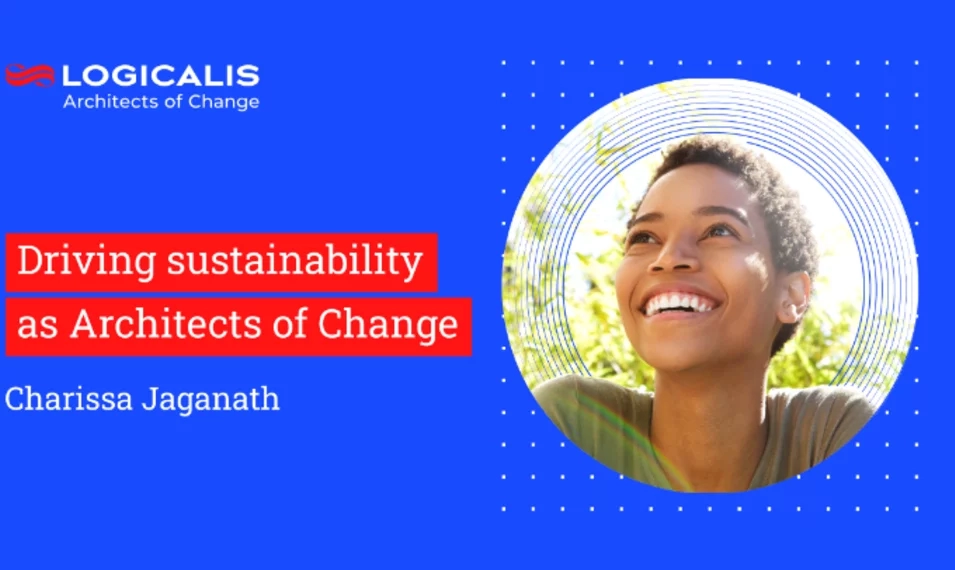
Global , Feb 1, 2023
Driving sustainability as Architects of Change
Being a responsible business is about the ability to make a commitment and make a difference. Charissa Jaganath discusses what Logicalis is doing to make a difference and why driving sustainability is so important to us.
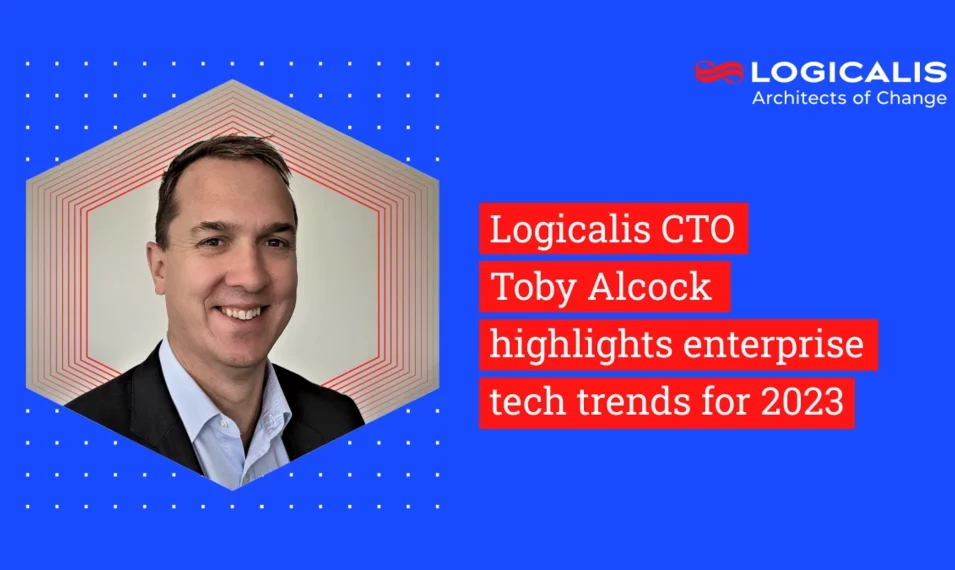
Global , Jan 23, 2023
Logicalis CTO Toby Alcock highlights enterprise tech trends for 2023
Digital innovation, cybersecurity, workplace talent, sustainability, and recession-proofing top the list At Logicalis, as we look forward to yet another busy and challenging year for the IT industry, we've put together the strategic technology trends for 2023 that can help IT leaders see through the current economic and market challenges and deliver sustainable business outcomes that matter.
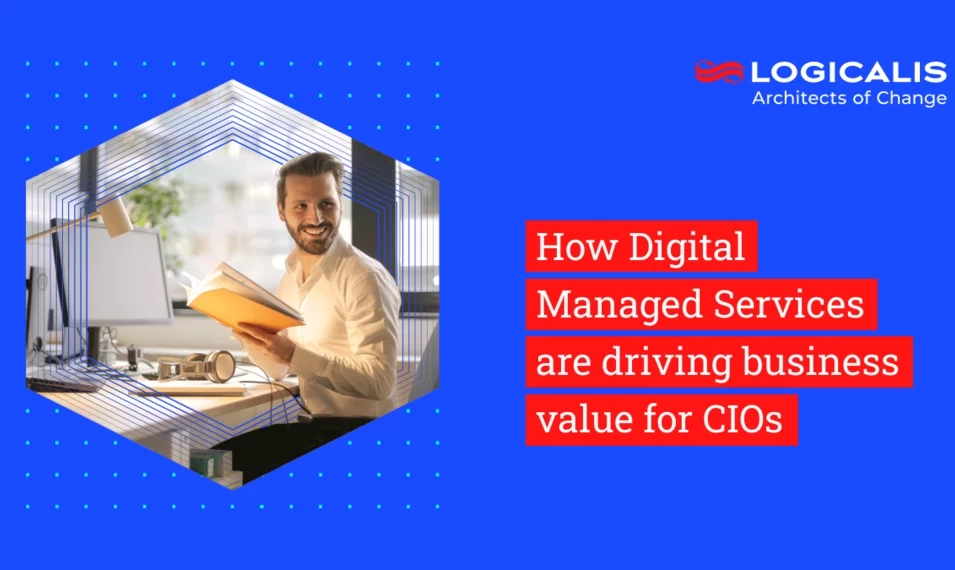
Global , Nov 22, 2022
How Digital Managed Services are driving business value for CIOs
Today’s CIOs face key challenges around futureproofing, innovating, and the perennial skills shortage. As businesses increasingly adopt a digital-first approach, CIOs need to deliver solutions and services that are future-ready, to mitigate the risks of these challenges.
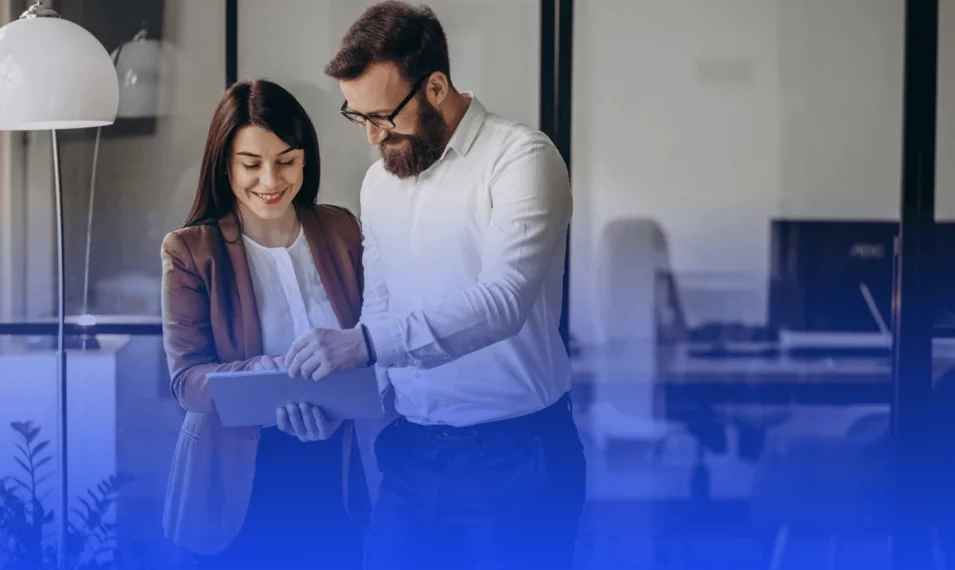
Global , Nov 16, 2022
Logicalis's Intelligent Connectivity solution now Powered by Cisco
Logicalis's Cisco Powered Intelligent Connectivity delivers SD-WAN and SASE offerings in a managed capacity, providing real-time insights into network performance. Find out more.
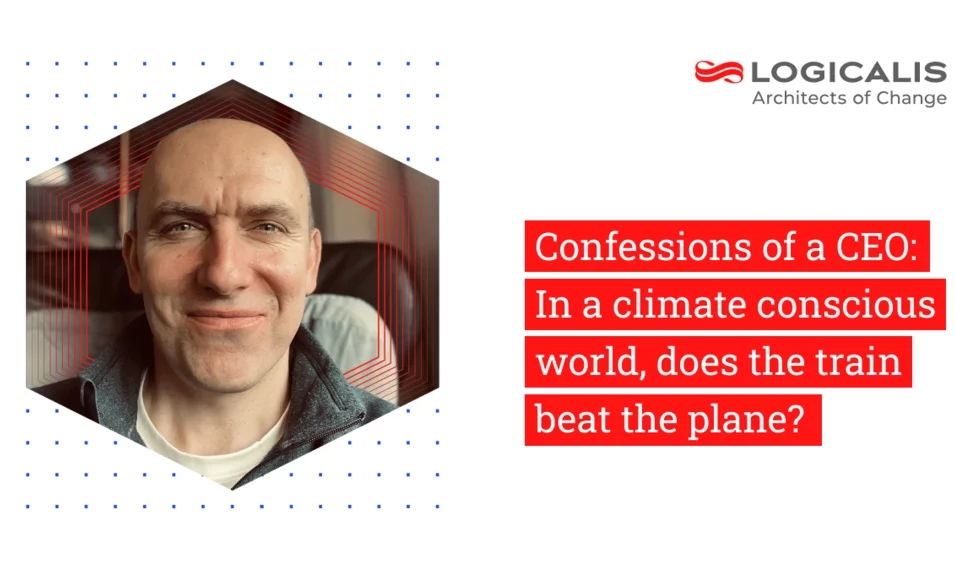
Global , Oct 11, 2022
Confessions of a CEO: In a climate conscious world, does the train beat the plane?
More and more climate-conscious travellers are opting to take the train instead of flying. With this in mind, and a business meeting coming up in Cologne, Bob decided to take the 580km trip by train. Here's how he got on
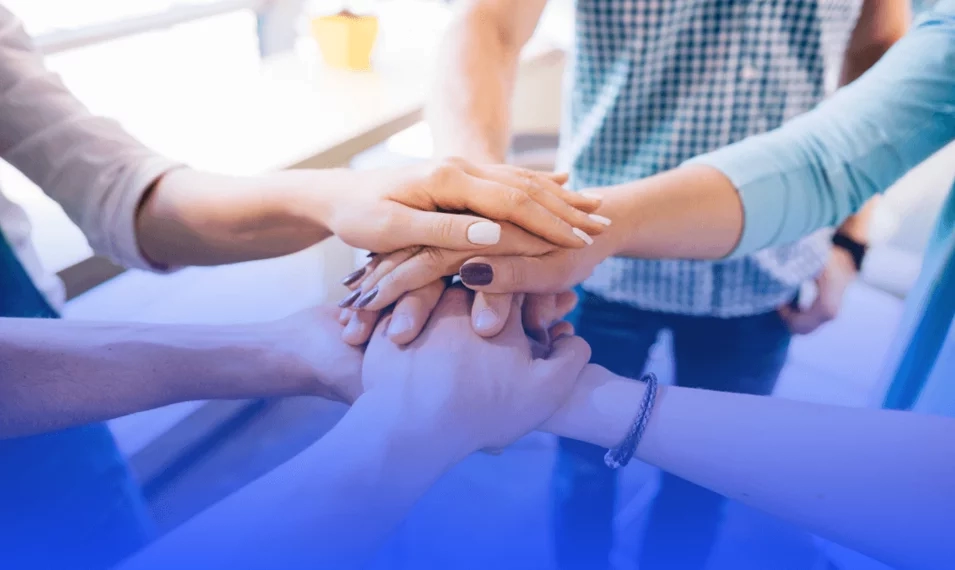
Global , Sep 28, 2022
Logicalis welcomes the overhaul of the Microsoft partner eco-system
Read how Logicalis has worked really hard, not only to be aligned with Microsoft Cloud, but also with Microsoft’s focus sectors. We have deep expertise in retail, health and financial services, and can leverage the full potential of Microsoft Cloud in every sector.
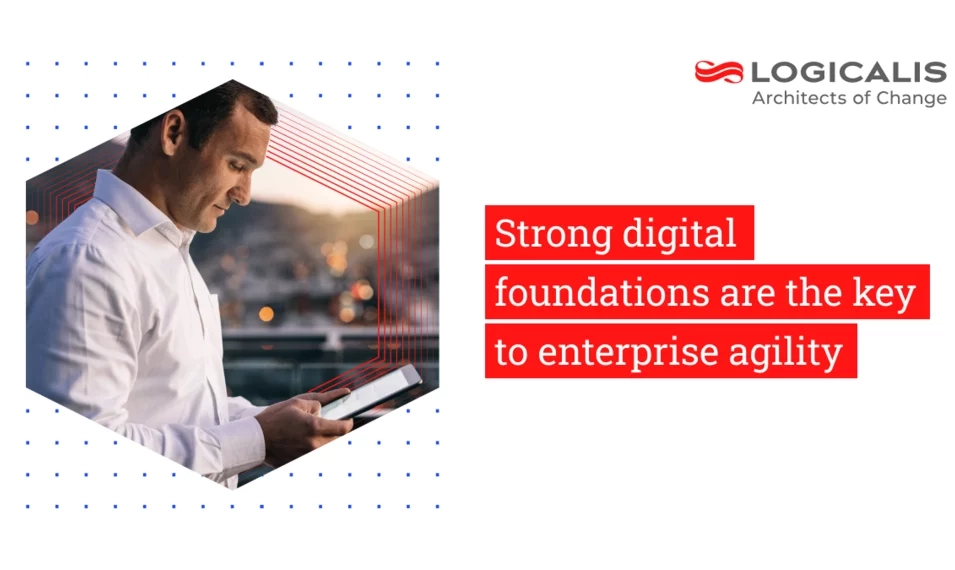
Global , Jul 9, 2022
Strong digital foundations are the key to enterprise agility
Safeguard your employees and data with a secure IT foundation. Learn how managed cloud services can protect staff, productivity, and morale in today's hybrid and remote work environment.
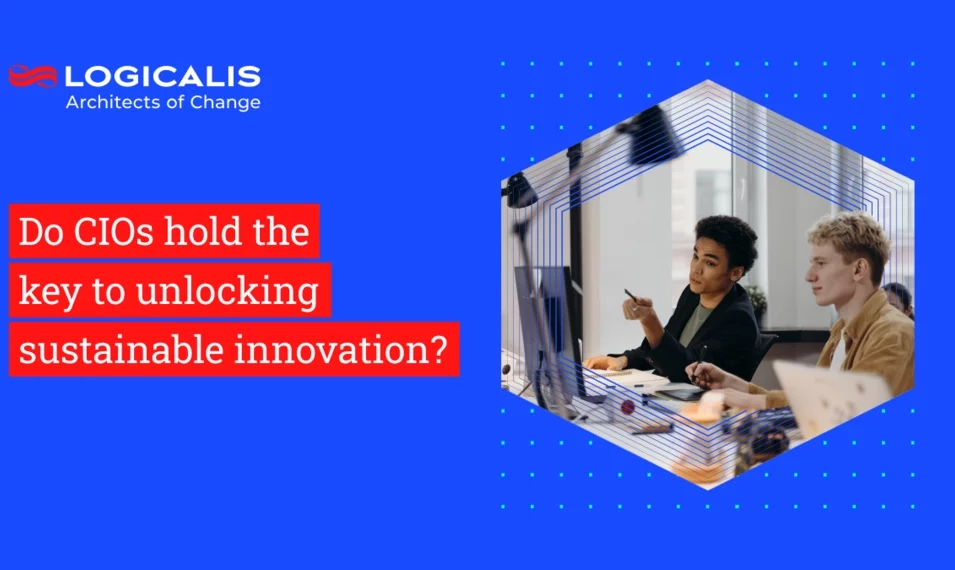
Global , Jun 16, 2022
Do CIOs hold the key to unlocking sustainable innovation?
Businesses need robust plans to lower emissions and reduce their impact on the environment. Businesses not only require sustainable innovation but efficient innovation through taking a data-driven approach and managing IT to outcomes, not uptime.
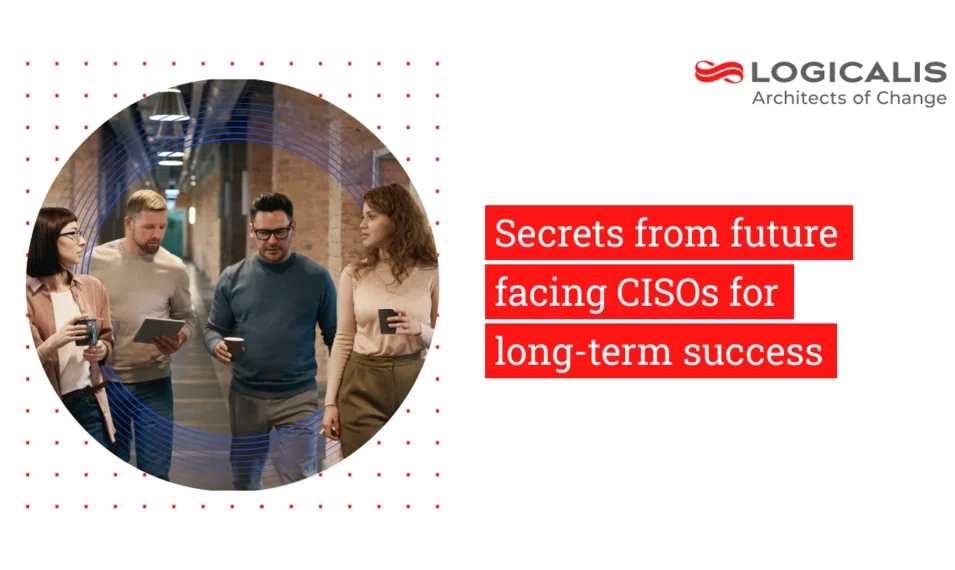
Global , May 11, 2022
Secrets from future facing CISOs for long-term success
Discover strategies for maintaining security and driving innovation in the modern marketplace. Learn how to balance risk and ensure long-term success in data security and risk management.
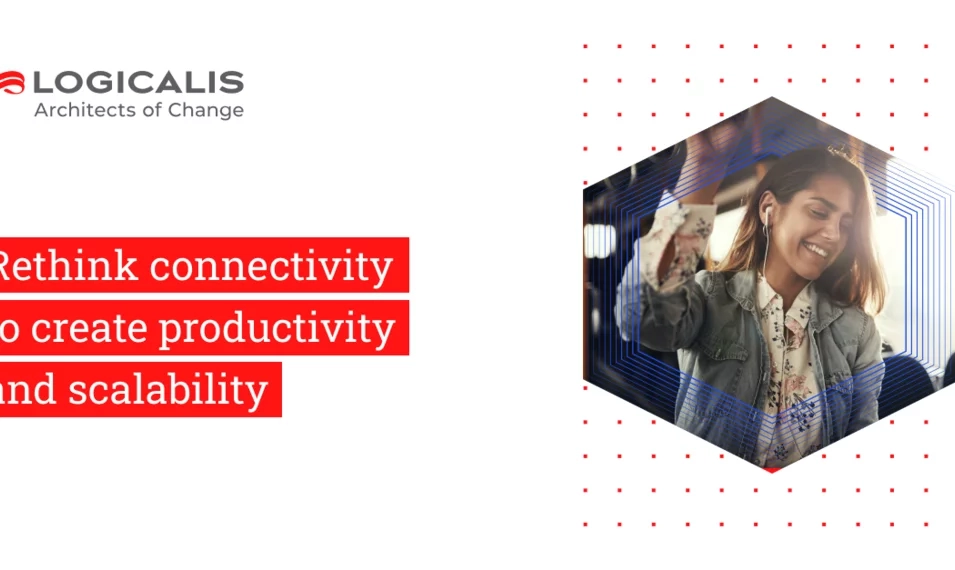
Global , Apr 21, 2022
Rethink connectivity to create productivity and scalability
Discover how businesses can optimise processes, reduce costs, and deliver new products at scale through the power of IoT connectivity.
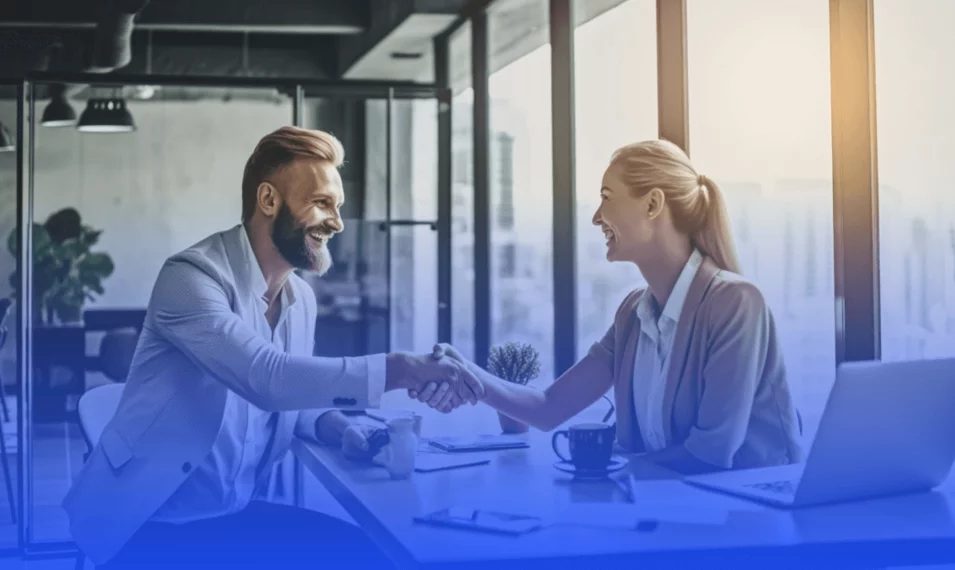
Global , Apr 19, 2022
Logicalis reflect on three-year journey of innovation and growth with Microsoft
Discover how Logicalis partners with Microsoft to provide the best hybrid cloud solutions and managed services. Learn about our advanced specialisations and industry-leading solutions.
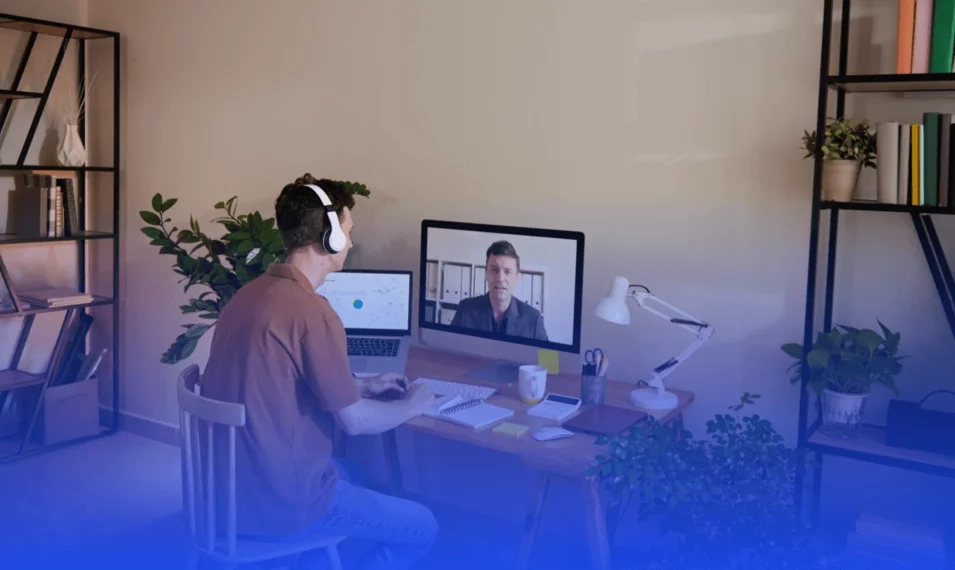
Global , Mar 31, 2022
Allow employees to collaborate freely
Boost productivity and foster effective communication with employee collaboration tools. Find out how to support your dispersed workforce and drive business success.
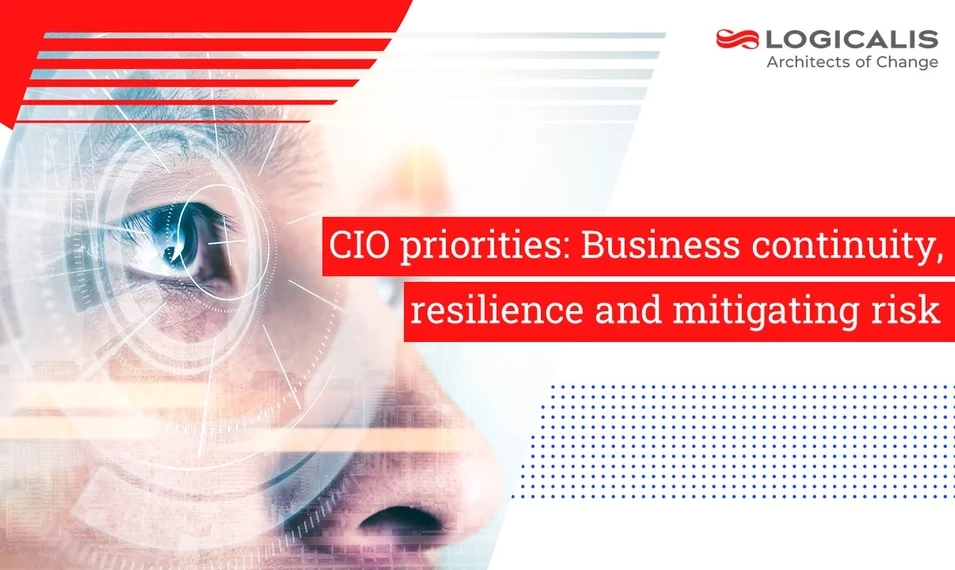
Global , Mar 24, 2022
CIO priorities: Business continuity, resilience and mitigating risk
With the right strategic approach, companies can combine security, resilience, and innovation, to create a clear competitive advantage, but businesses must act now to capitalise on the tools and skills available to them
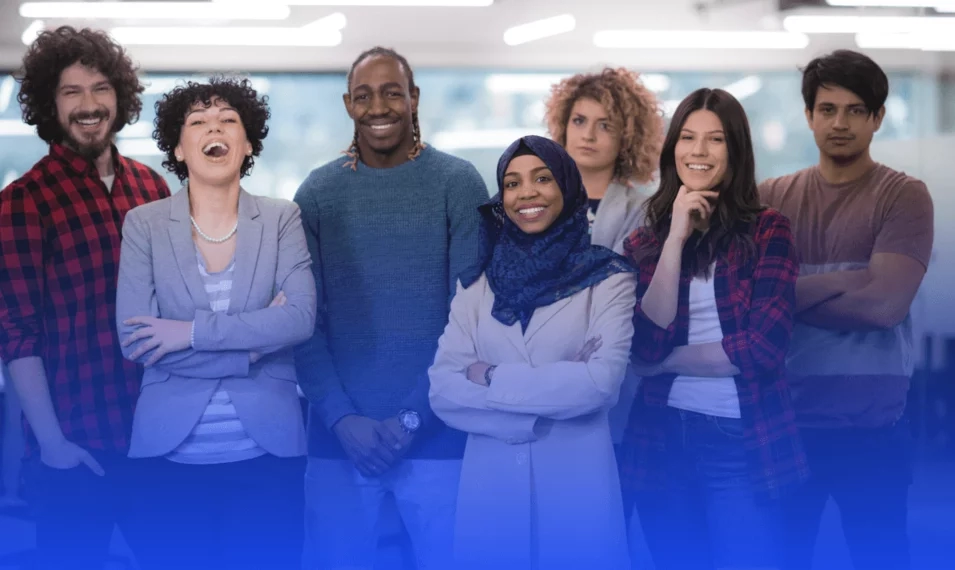
Global , Mar 22, 2022
A new generation of workers demand a new approach to the workplace
The rise of remote working and a younger digitally native workforce, is shaking up traditional business structures. Many organisations are still adapting their workspaces to cope and in some instances need to overhaul their approach to work entirely.

Global , Mar 15, 2022
Diversity as a key differentiator in transformation
Discover how embracing equality, diversity, and inclusion can drive business success. Learn why diverse and inclusive workplaces are essential in today's competitive landscape.
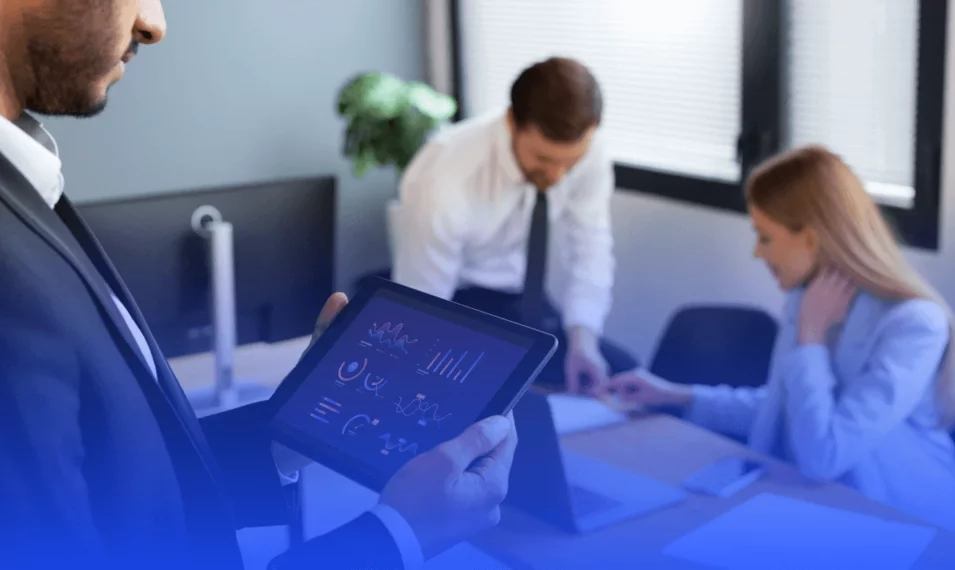
Global , Mar 9, 2022
Actionable insights are the missing link to collaboration in the hybrid workplace
Discover how to overcome barriers in the hybrid workplace and promote collaboration for increased innovation. Learn how data and insights can drive better employee communication and results
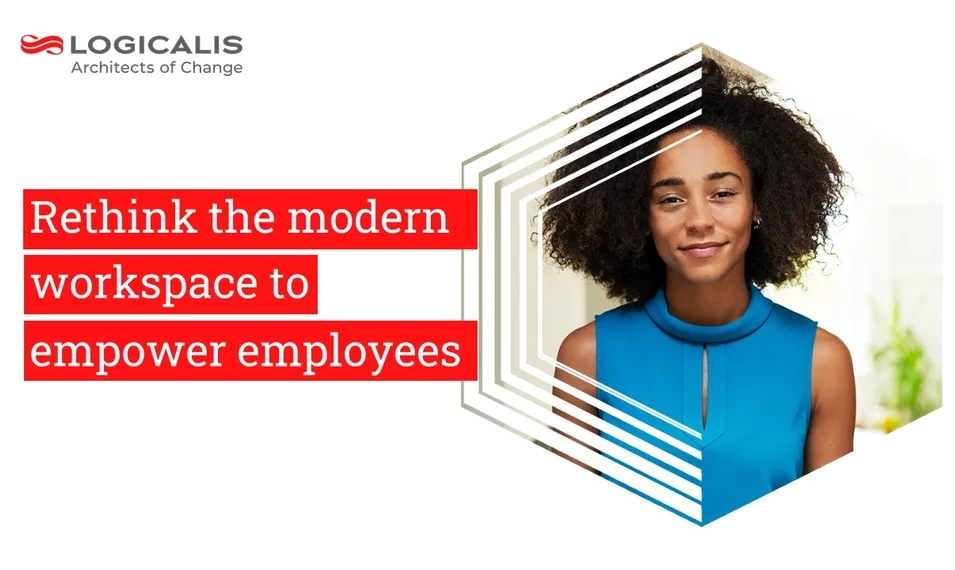
Global , Feb 16, 2022
Rethink the modern workspace to empower employees
Discover how senior leaders can create a balance between business needs and employee preferences to cultivate a productive hybrid office environment.
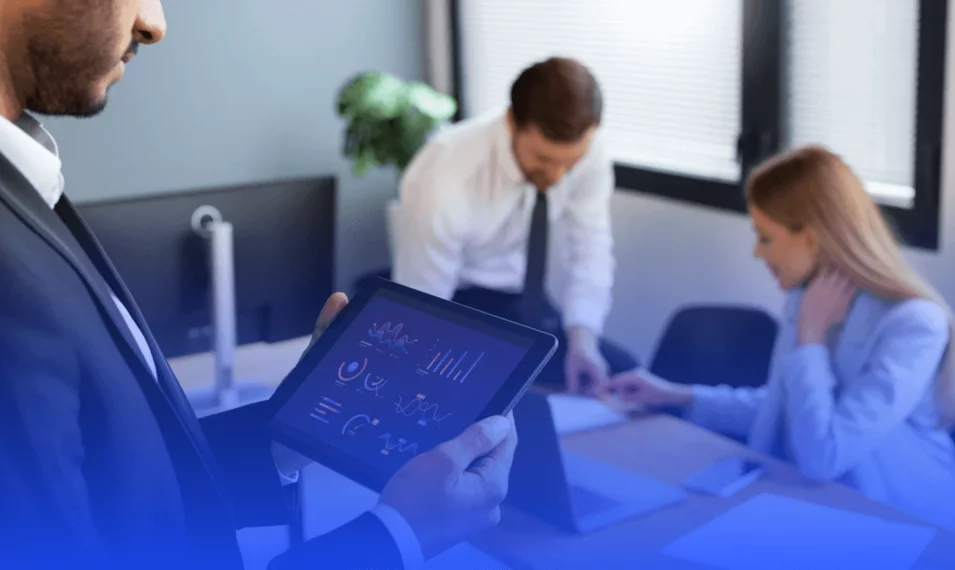
Global , Feb 9, 2022
Is effective collaboration no longer bound by time or place?
Discover how to empower your employees and optimize collaboration in the digital workplace for enhanced productivity and success.
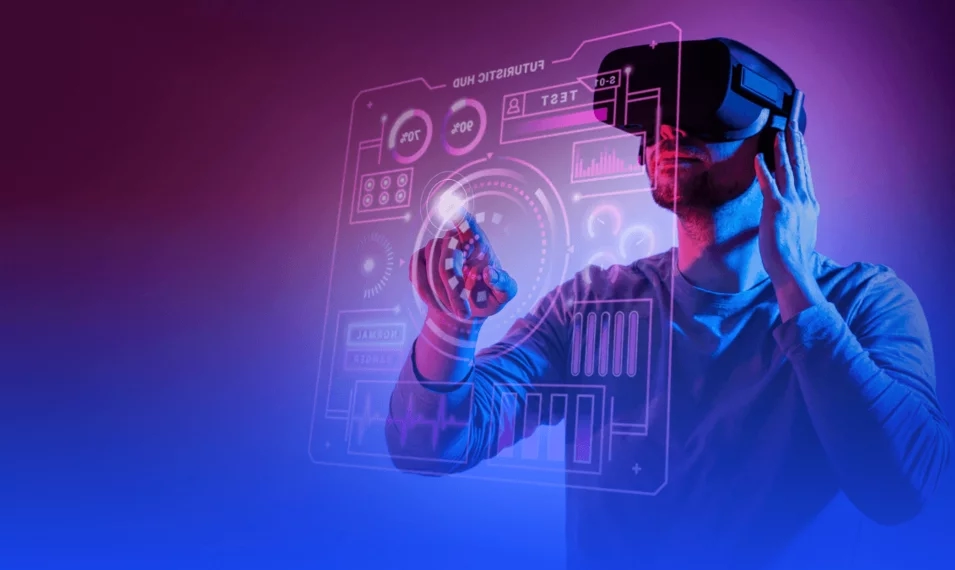
Global , Feb 1, 2022
Business trend predictions for 2022
Logicalis Group CEO Bob Bailkoski, sat down with us and talked us through his top three predictions for the year ahead. Find out what they are ...
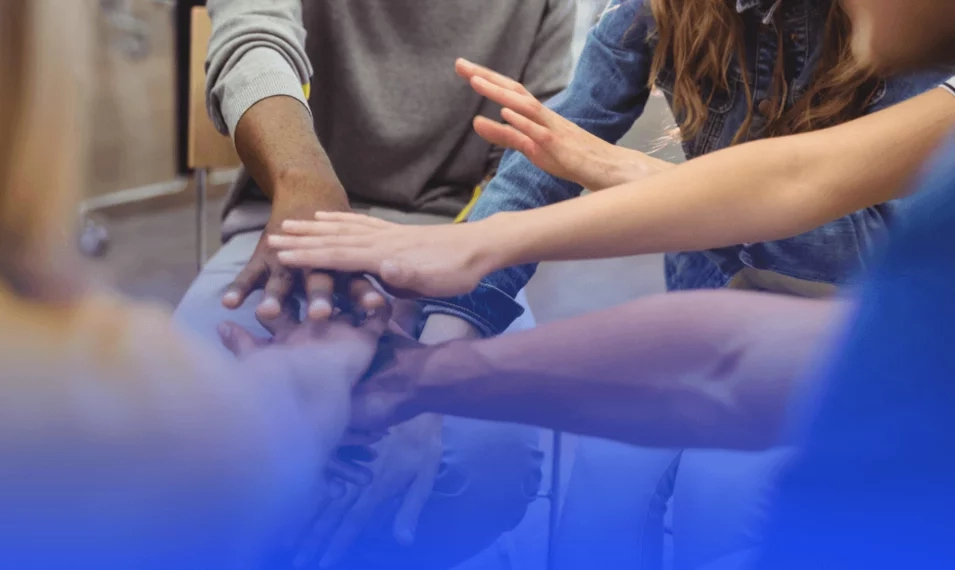
Global , Jan 26, 2022
Creating a culture of innovation and the digital workplace
Alongside the innovation within company culture, CIOs must ensure their employees are satisfied as the hybrid workplace takes shape.
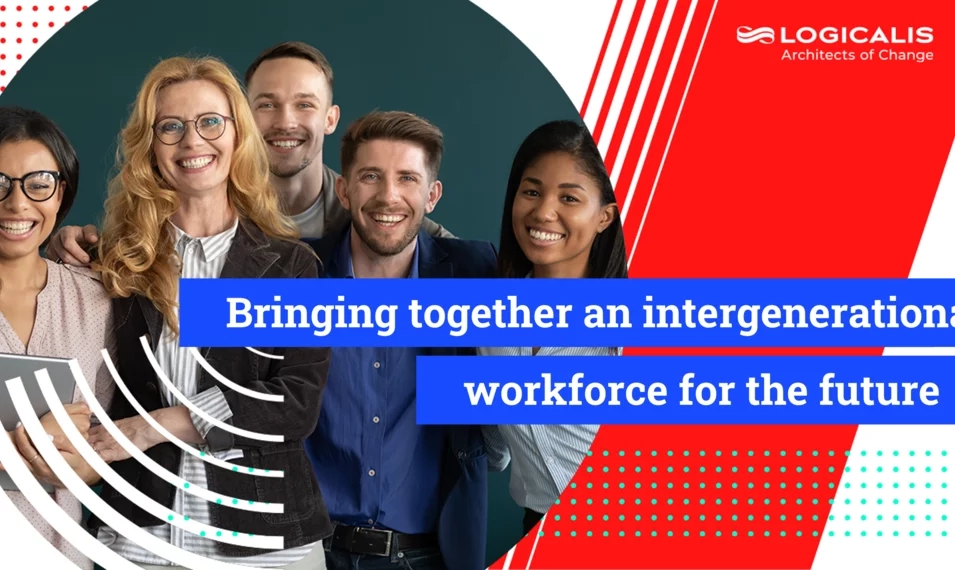
Global , Jan 13, 2022
Bringing together an intergenerational workforce for the future
To attract and retain talent, leaders need to take the time to understand what younger generations really want from their work environment and consider how to empower an increasingly divided intergenerational workforce.
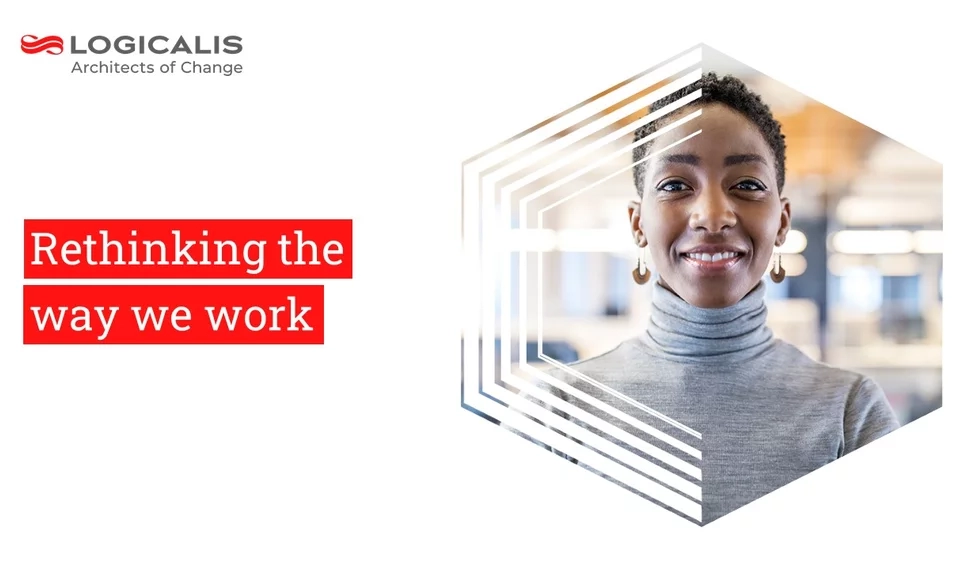
Global , Dec 7, 2021
Rethinking the way we work
Logicalis helps businesses rethink their approach to digital transformation strategy to take a hybrid approach with agility, scalability, and innovation at the core, building resilient businesses for the future.
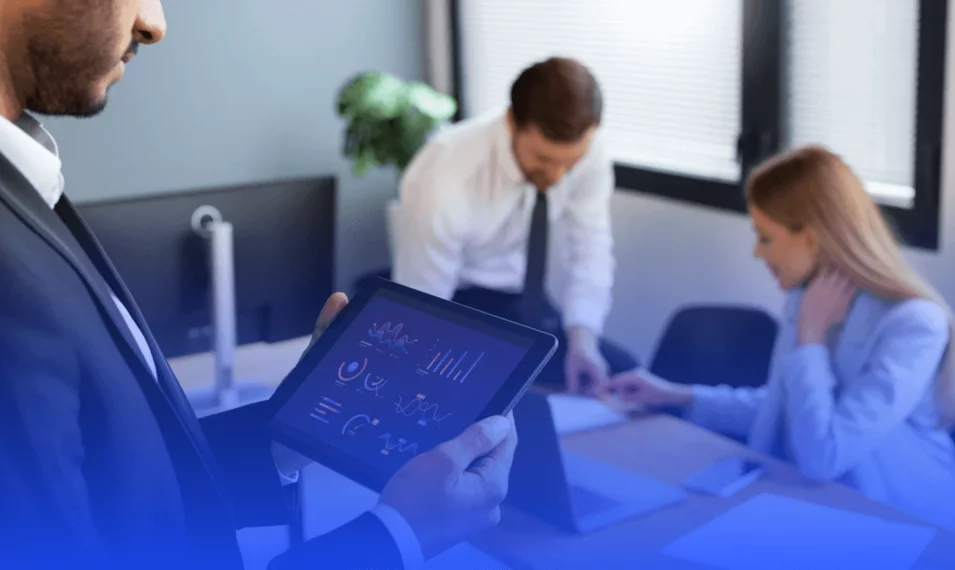
Global , Nov 29, 2021
Unlocking data to drive business strategy and accelerate growth
The need for digital transformation is more prevalent than ever with the pandemic triggering companies to shift and realign their priorities. Results from this year’s survey identified that three quarters of respondents admit their organisations are wrestling with their abilities to unlock data
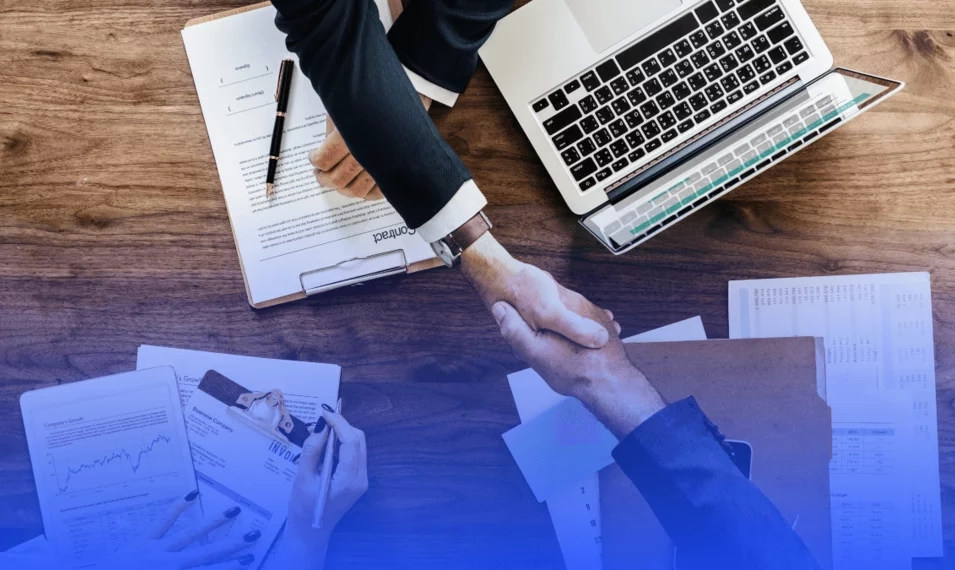
Global , Nov 16, 2021
Logicalis recognised with 18 awards at the Cisco Partner Summit 2021
One of only five Cisco Global Gold Certified Partners, Logicalis has worked in partnership with Cisco for over 25 years to combine global expertise with intelligent cutting-edge solutions that deliver business success through digital transformation
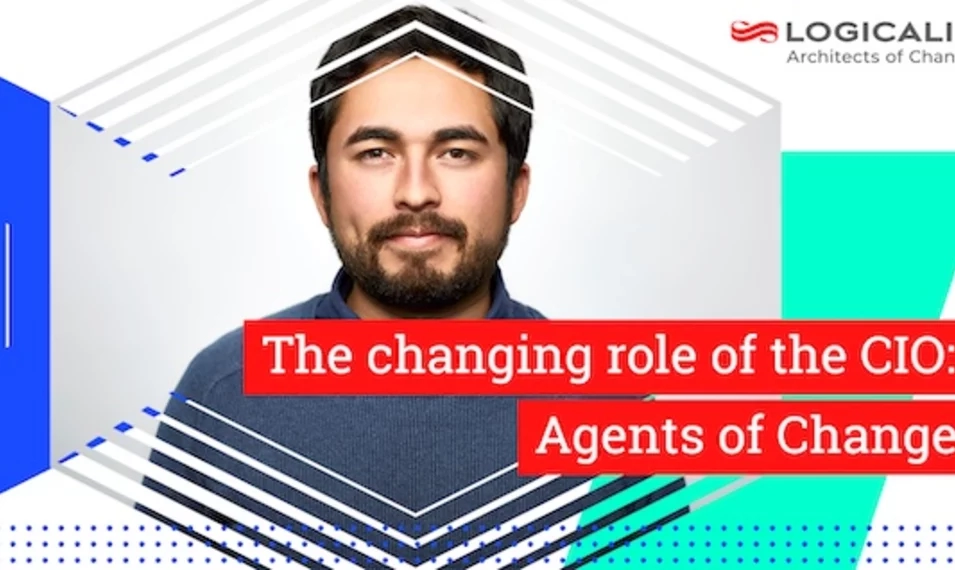
Global , Sep 28, 2021
The Changing Role of the CIO - Emerging Agents of Change
Strong customer relationships have become a critical business priority according to the results of the first report in a four-part series following the eighth annual Logicalis Global CIO Survey.
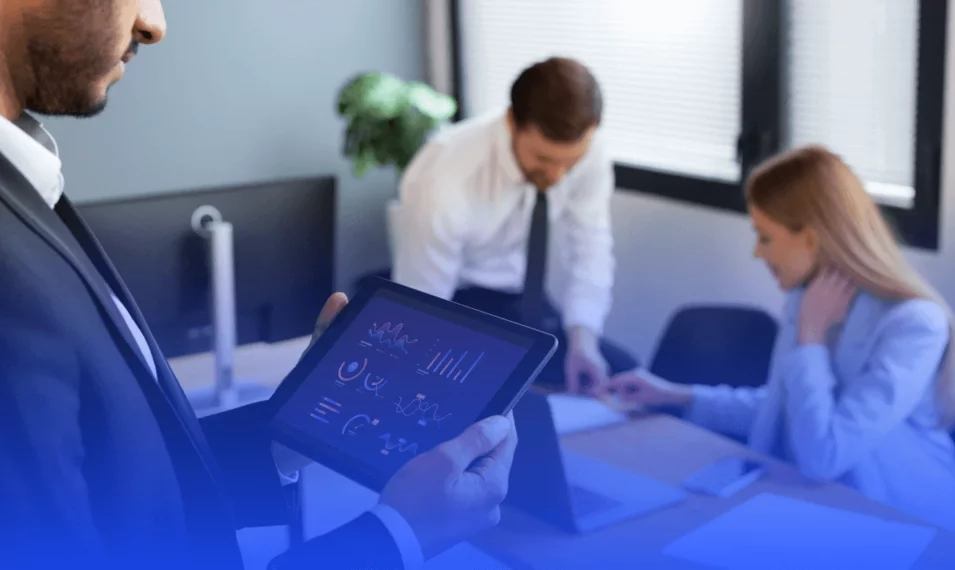
Global , Sep 21, 2021
Want return on digital investments? Look to a managed service provider
Today every business, regardless of industry, is operating in a hyper-competitive environment with everyone battling for their place in the digital economy
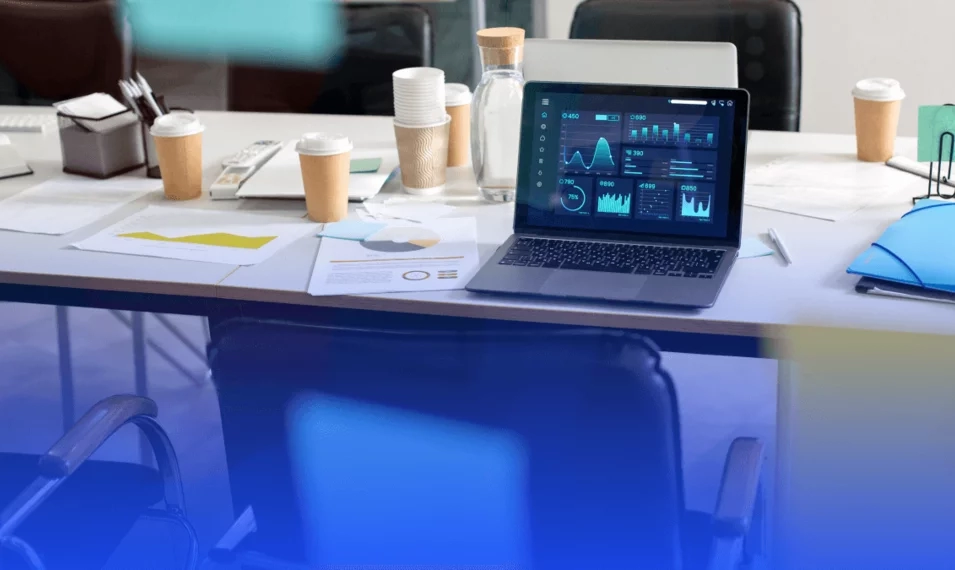
Global , Sep 14, 2021
The holy trinity in effective digital workplaces? Cloud, data, and security
Discover the key elements of a successful digital workplace strategy and how enlisting the help of an expert partner can ensure continued success. Unlock the full potential of your organisation with a holistic approach to digital workplace strategy.
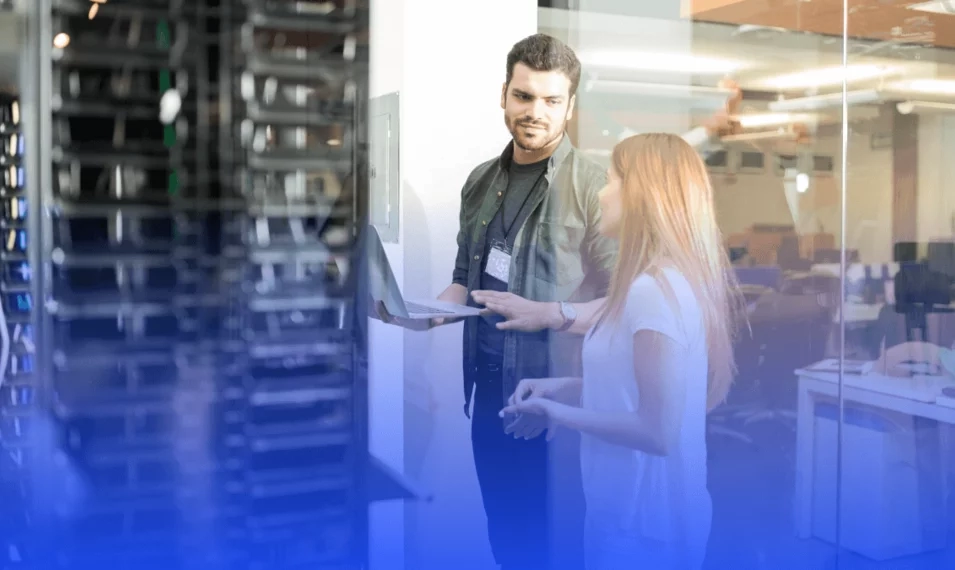
Global , Sep 7, 2021
Can a lifecycle approach to cloud adoption improve success?
Cloud migration offers a range of benefits from security to scalability. Successful and optimised cloud migration, especially in the post-pandemic digital economy, will be critical for achieving real-time performance and efficiency.
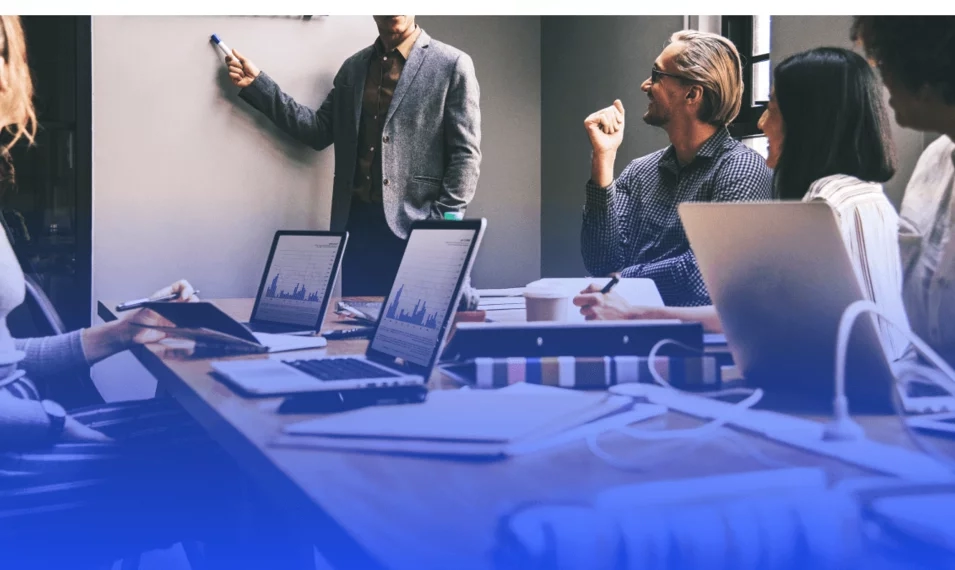
Global , Aug 31, 2021
Truly successful digital transformation includes employee experience from the start
Discover how a human-centric approach to digital transformation can enable business growth and optimize employee performance. Learn how to tackle the challenges and empower your workforce with the right digital tools.

Global , Aug 26, 2021
The connected workplace is not just for offices
Discover how WiFi 6 and 5G are revolutionizing industries. Together Cisco and Logicalis bring unrivaled expertise to personalize IoT and 5G solutions for your business.
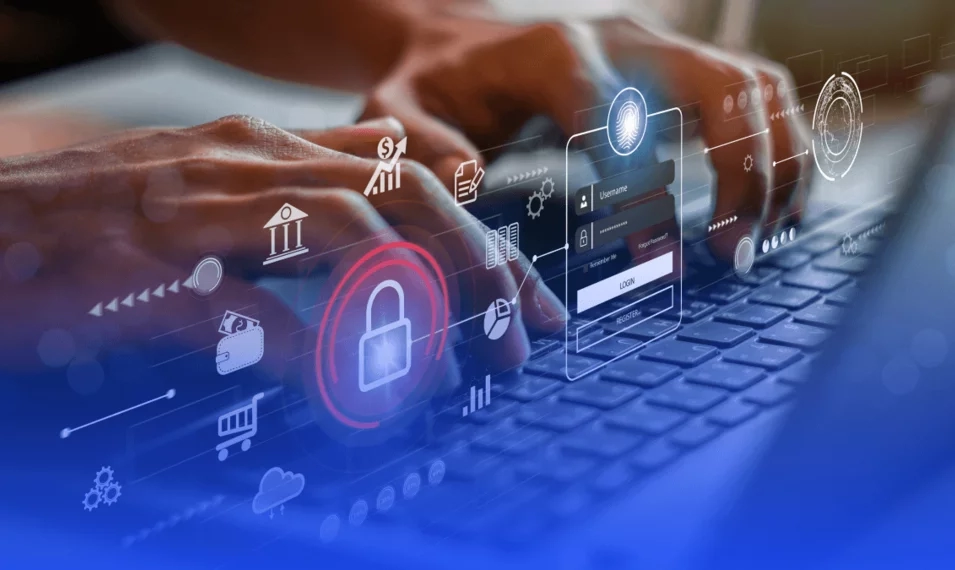
Global , Aug 24, 2021
5G: The next enterprise revolution
5G is less about high-speed connectivity and more about unleashing data and computing capability. With the ability to power future solutions such as autonomous cars, 5G technology can accelerate the growth of low-cost enabled Internet of Things (IoT) devices and more
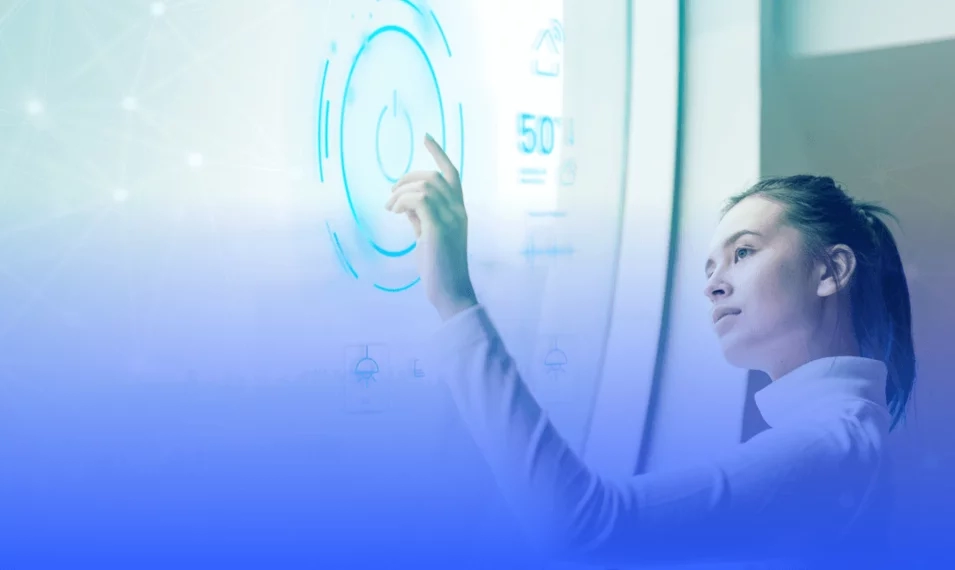
Global , Aug 10, 2021
Will digital transformation help you compete in the digital economy?
Discover the power of digital transformation in driving business growth, efficiency, and customer satisfaction. Unlock new possibilities and create a digital-first organization with data at its core
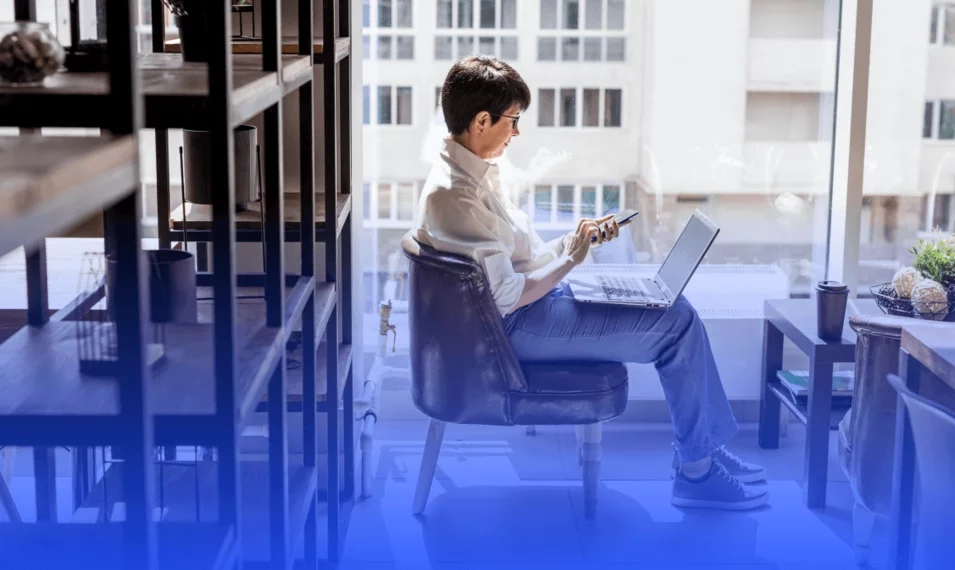
Global , Jul 5, 2021
Enabling collaboration in a digital workplace
It’s pretty clear that digital workplaces are here to stay in one form or another. As a growing number of organisations move to make flexible or remote working part of their permanent policy, there are clear benefits to a digital workplace.
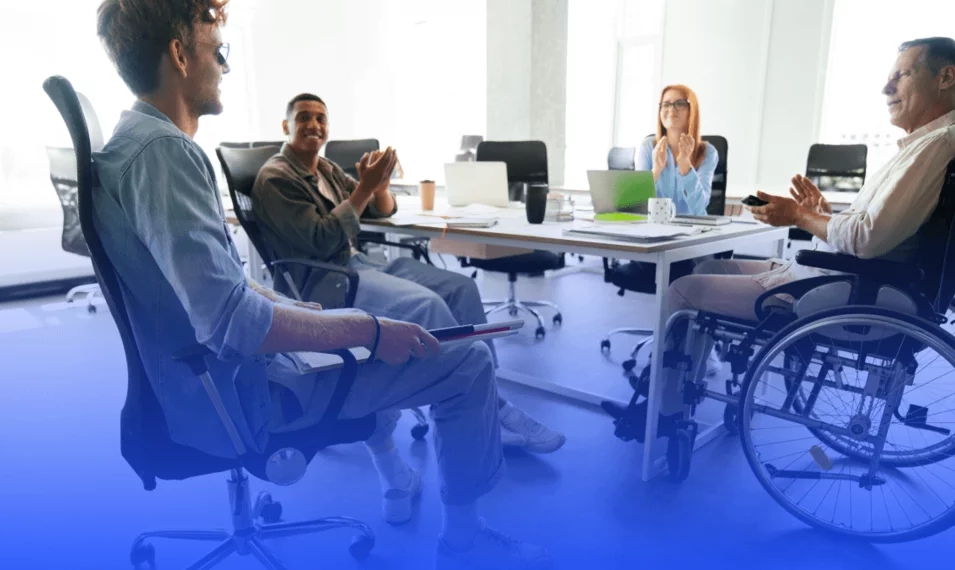
Global , Jun 28, 2021
Preparing for the hybrid workforce of the future
Discover how a collaborative workplace can enhance communication, build company culture, and improve market responsiveness. Partner with experts for the right collaboration tools.
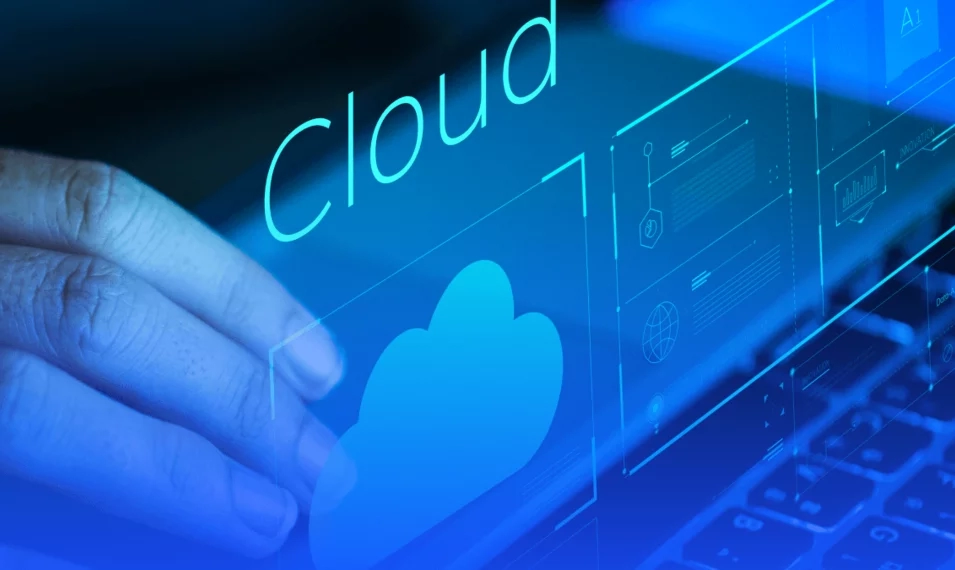
Global , Jun 15, 2021
How the global chip shortage is driving data centre projects to the cloud
Explore how moving to the cloud can offer a cost-effective and flexible solution for managing new projects and workloads during the chip shortage. Learn how cloud managed services can provide ample capacity without the high costs of an on-premises solution.
Global , Apr 28, 2021
Your business may not exist if you are not in the Cloud
Discover how transitioning to the cloud can help your business adapt to changing customer demands and achieve greater agility. Explore the benefits of cloud technology and gain a competitive edge
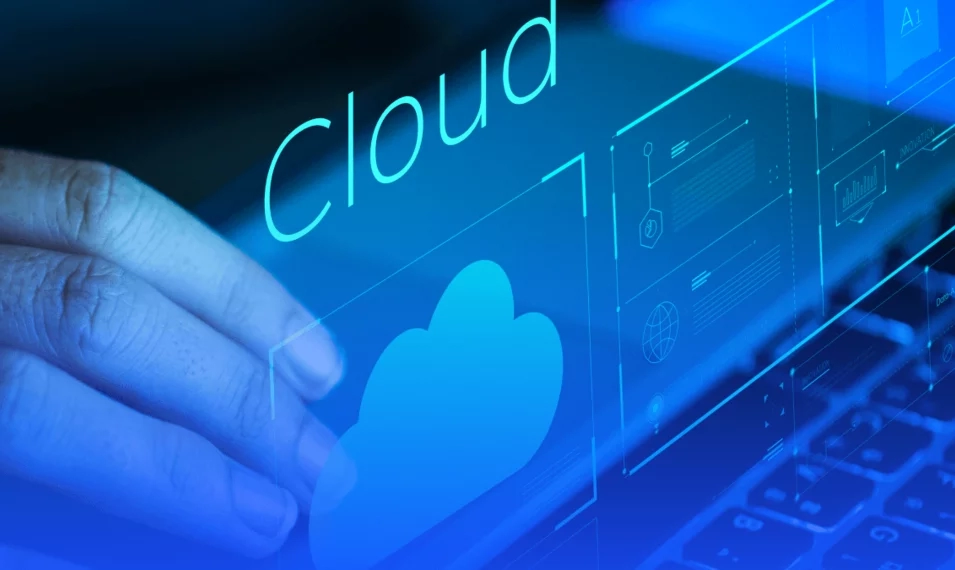
Global , Apr 5, 2021
Big Data and Cloud: The perfect business partners
Discover how cloud technology and infrastructure advancements enable businesses to unlock the true value of Big Data analysis. Learn how flexible infrastructure and scalable services support variable workloads.
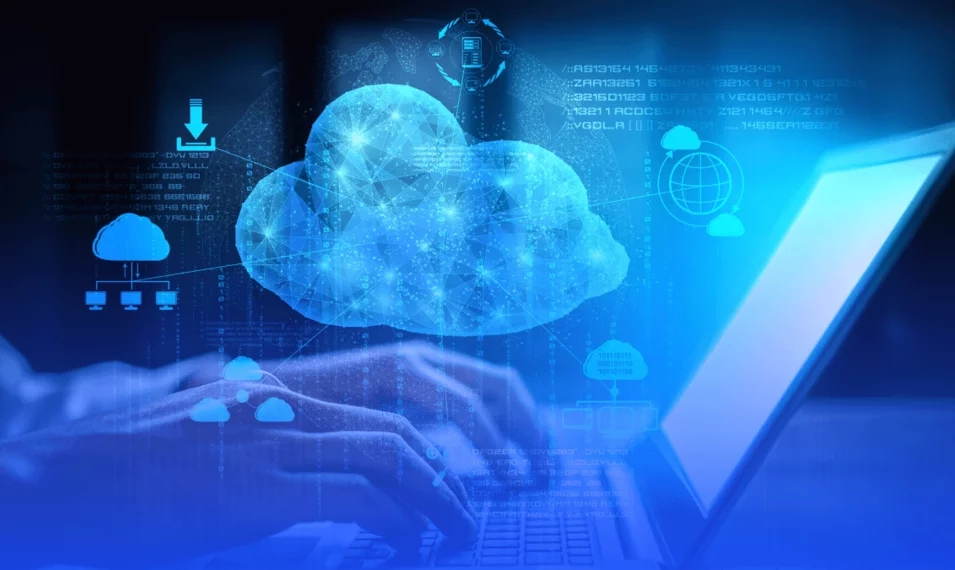
Global , Mar 30, 2021
Run VMware on Azure? Yep, you read it right!
Azure VMware Solution shouldn’t be overlooked as a valid step on a cloud journey. It enables migration to the cloud at an infrastructure level, without disrupting application or operations teams.
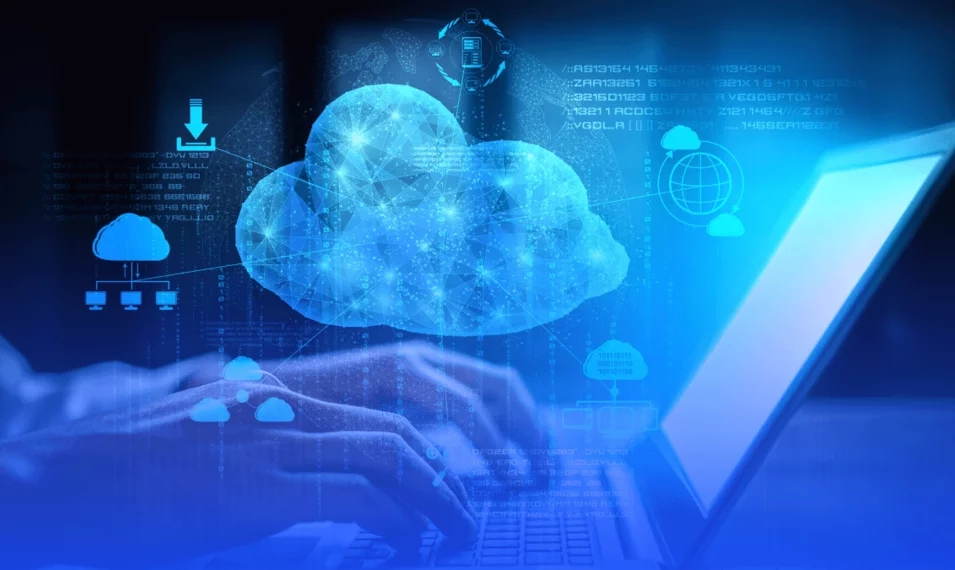
Global , Mar 26, 2021
How the pandemic uncovered the need for global solutions with local execution
Successful digital transformation requires the integration of technology into all areas of a business. The aim is to fundamentally change how an organisation operates and delivers for its customers.
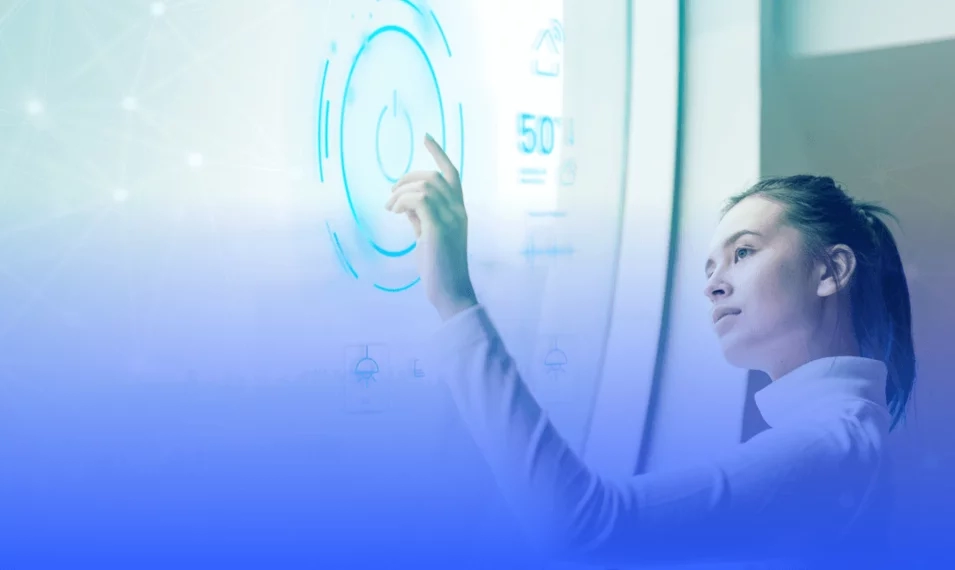
Global , Mar 19, 2021
Transforming business models to focus on agility
Achieve true business technology needs with a strategic multinational technology partner. Scale solutions at pace and gain global foresight and overview for your enterprise digital transformation journey
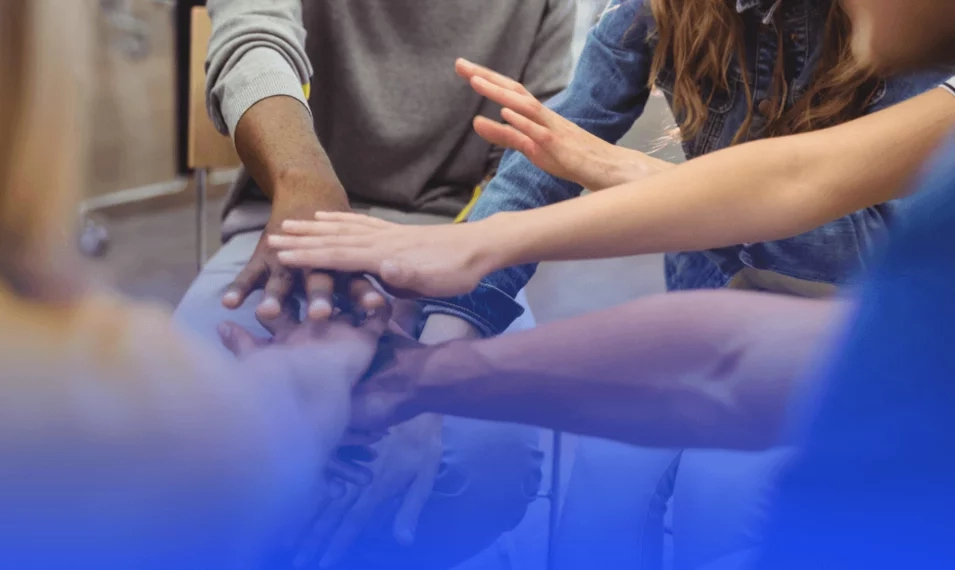
Global , Mar 16, 2021
Logicalis South Africa builds a digital future in local school
Learn how Logicalis South Africa supports education and empowers future Architects of Change through its CSR strategy and initiatives. Find out more about their commitment to the BBBEE Act and investments in education.
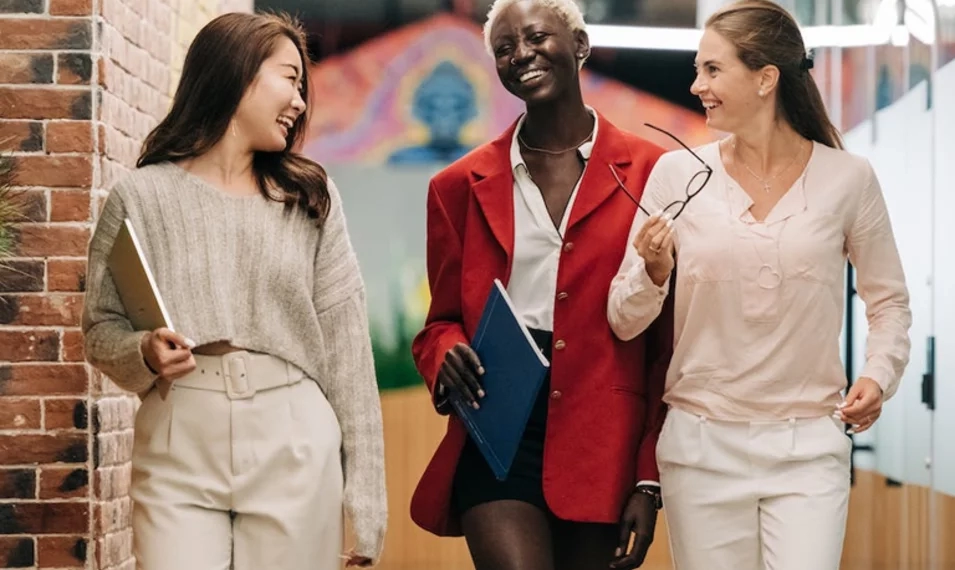
Global , Mar 8, 2021
International Women's Day 2021
Our teams around the world are committed to supporting gender equality and challenging gender bias and inequality. To celebrate International Women’s Day 2021, we spoke to a couple of women in leadership from across Logicalis.
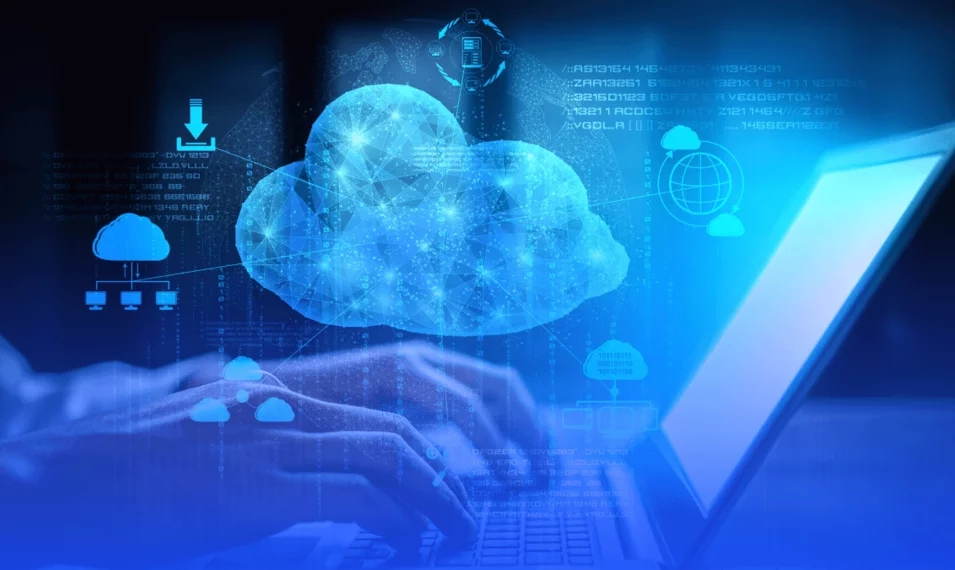
Global , Feb 18, 2021
Cloud: Everything to play for, no time to lose
Discover why 83% of global CIOs anticipate increased demand for cloud technology. Gain valuable insights on the impetus for change and the growing enthusiasm for digital transformation.
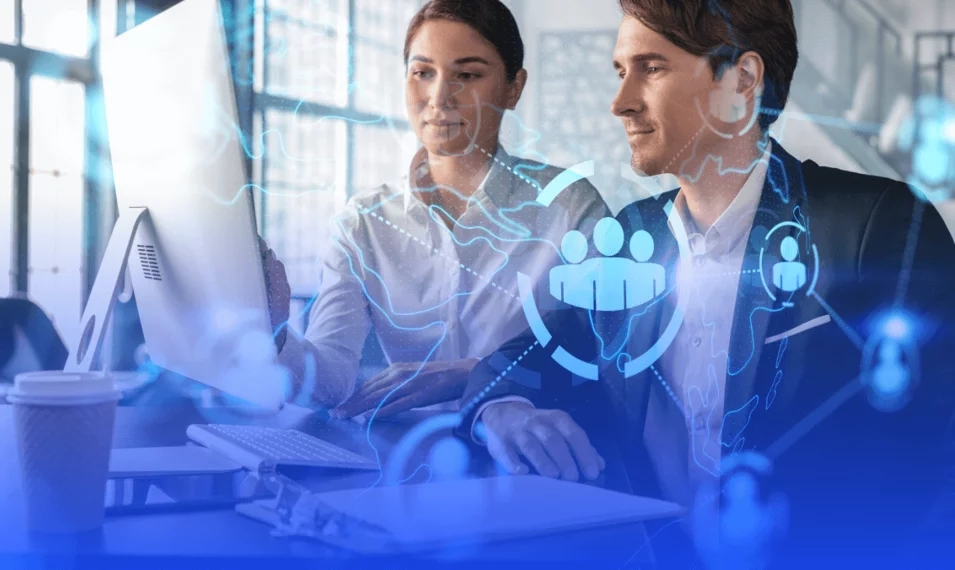
Global , Feb 15, 2021
How to unlock resources with managed services
Outsourcing the management of IT is a proven way to increase services levels, and in many cases decrease costs, but only if it’s done right. Identifying the right managed services partner is crucial, as well as assessing their services, policies and way they conduct business.
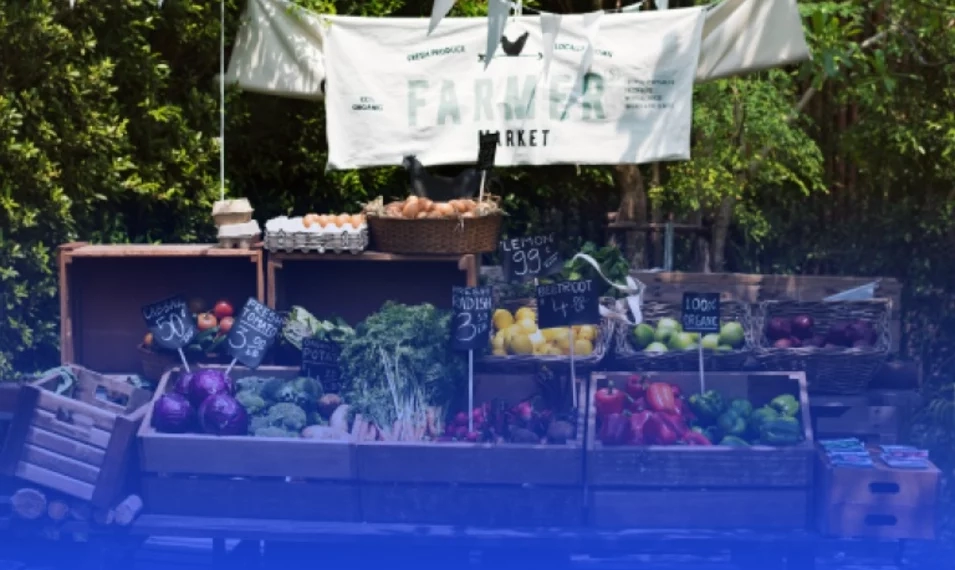
Global , Feb 9, 2021
Supporting local communities across Germany
Discover how Logicalis Germany's local CSR programme is bringing technology, resources, and people together to support community-based initiatives in every region. Learn how our engagement with various charities and initiatives is making a real impact.
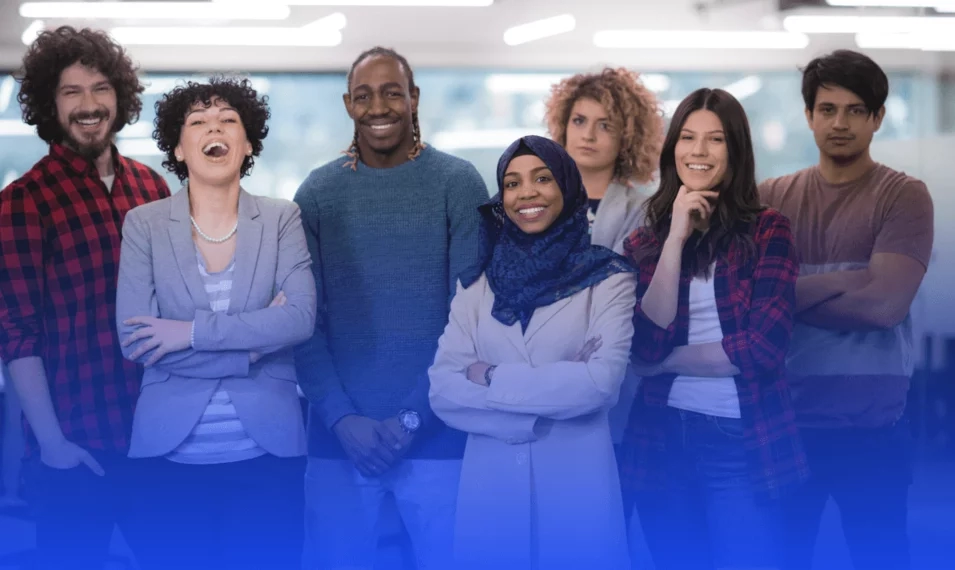
Global , Jan 29, 2021
Building a better world for a brighter future
Discover how our initiatives are improving diversity in the tech industry, supporting disadvantaged youth, and empowering adults transitioning into tech careers. Read about how we're making a grassroots impact
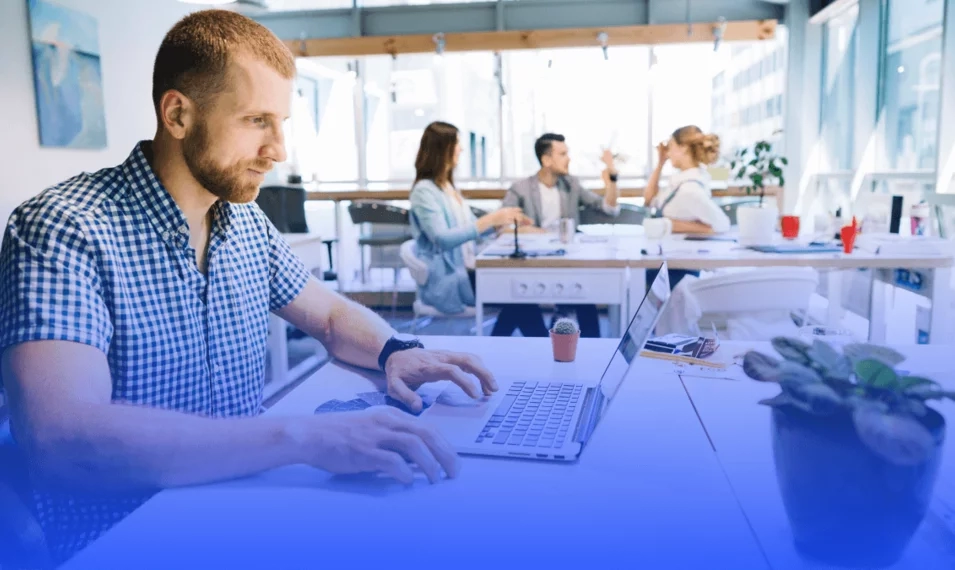
Global , Jan 18, 2021
Unlocking the power of Big Data
Intelligent platforms, evolving technology and digital transformation have increased the potential value of data exponentially. However, to extract the greatest value from the raw material that sits beneath the surface, you need to mine, refine and distribute it effectively, whilst keeping it secure.
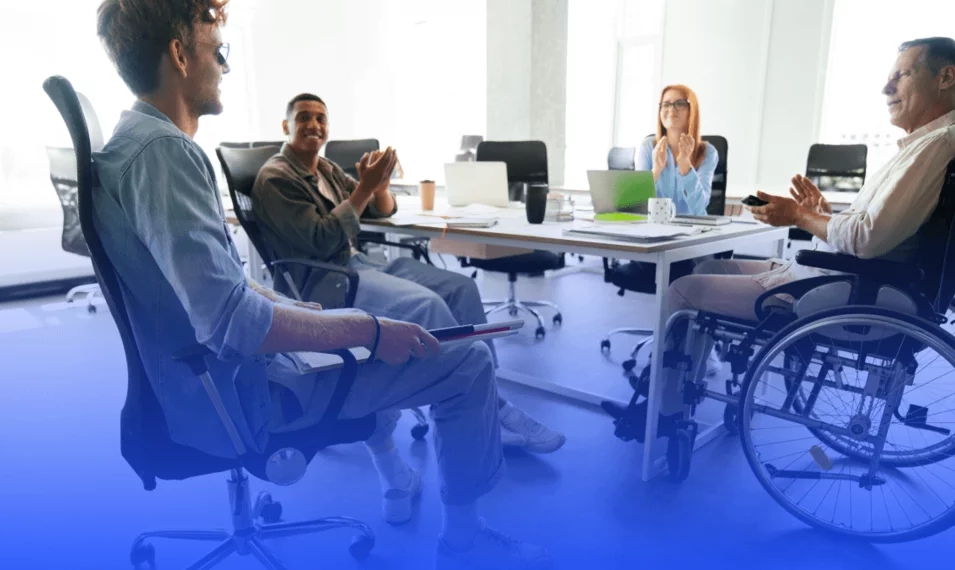
Global , Jan 12, 2021
Protect your business’ most important asset – its employees
Remote working is here to stay, and employees have learnt how to stay productive and proactive. However, the sudden transition to working from home has not been an easy one.
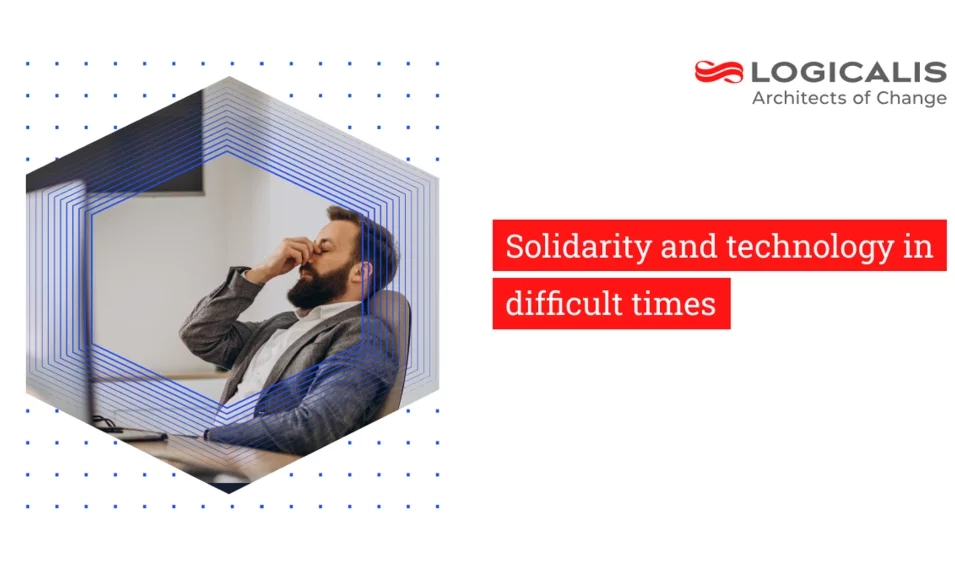
Global , Sep 16, 2020
Solidarity and technology in difficult times
In this article, Rodrigo focusses on the positives from the COVID-19 pandemic and takes pride in the professionalism and dedication of the various teams within Logicalis.
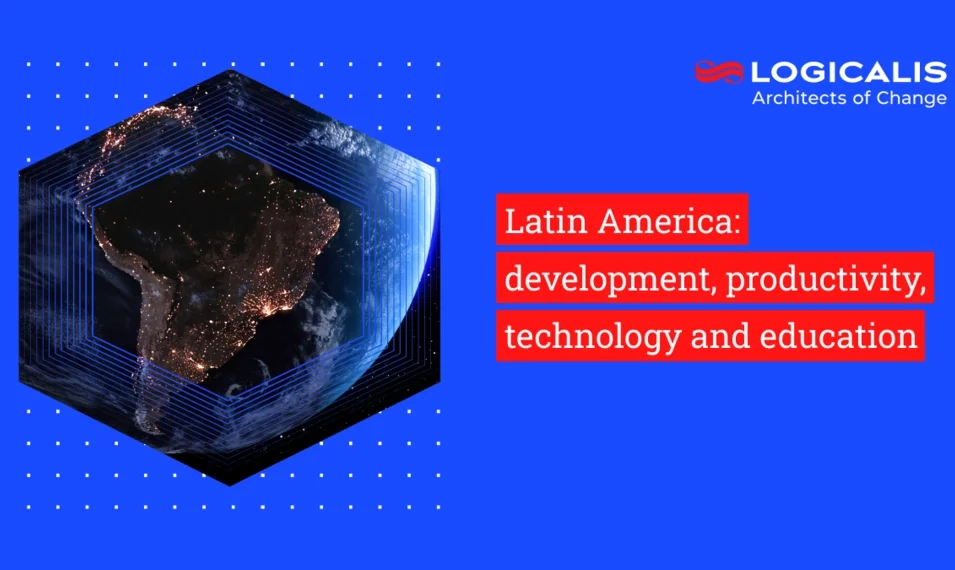
Global , Sep 16, 2019
Latin America: development, productivity, technology and education
Despite its geographical size and abundance of natural resources, Latin America, is an economically small region yet its GDP corresponds to approximately 7% of the world total, a proportion that has remained relatively stable since the 1970s.
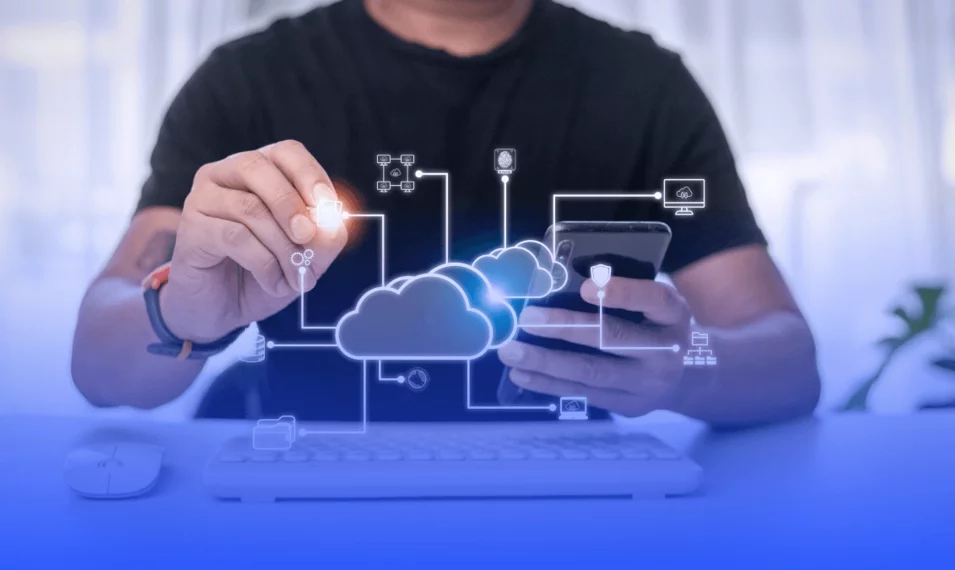
Global , Aug 31, 2017
What is IBM Watson and what can it do?
Discover how IBM Watson, an AI platform for business, combines advanced analytics to provide the ultimate cognitive supercomputer available as a SaaS and APIs for developers.